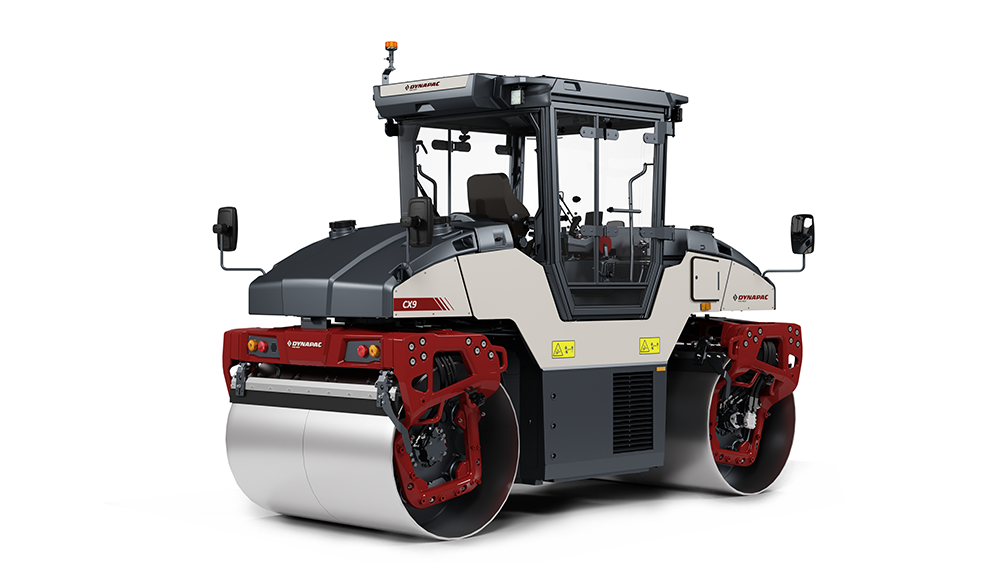
He explained that as temperature is a critical factor for stiffness in asphalt compaction and because the material is in layers, the system required heat sensors to be installed and more complex algorithms to be developed. As with the system for soil compaction, the technology allows drum vibration to match the resonant frequency of the asphalt course to provide optimum compaction. Because the system matches the compaction forces required to the characteristics for a specific section of surface, it also offers another important benefit as the spokesperson said, “You will never damage the aggregate.” This avoids the risk of aggregate being cracked or crushed by compaction forces. He added, “The seismic system adjusts the frequency every 0.2 seconds.”
The system is now offered as an option on the new rigid frame CX 8C and CX 9C models, which have drum widths of 1.5m and 1.7m and weights of 8tonnes and 9tonnes respectively. These models have also now been upgraded to the Generation 6 level seen earlier on the 6, 10 and 13tonne class machine. Meanwhile, the 6, 10 and 13tonne Generation 6 models will be made available in Seismic form as an option later in the year.
To meet French requirements these Generation 6 drum steer machines deliver 0.8mm of amplitude and benefit from larger eccentric weights and reinforced bearings. This specification is now the standard for the CX models. The vibration system itself is conventional though and does not require any special maintenance as the core of the technology is in the control unit, while it is said to be simple for the operator to use.
Other key benefits for the Seismic option are reduced operating noise, less vibration for the machine (in turned reducing wear and tear and fatigue for the operator) and lower fuel consumption. The spokesperson said, “We estimate around 10% fuel savings.”