Keestrack’s full product range of crushing and screening units are deployable in mobile processing technology for recycling applications and aggregate production.
Its current versions offer proven models while brand new plants are available from the international manufacturer
“A high level of mobility on-site and between deployments; considerable ease of operation, and maintainability and superior cost-effectiveness, have for many years been the guiding principles in cross-technology development of m
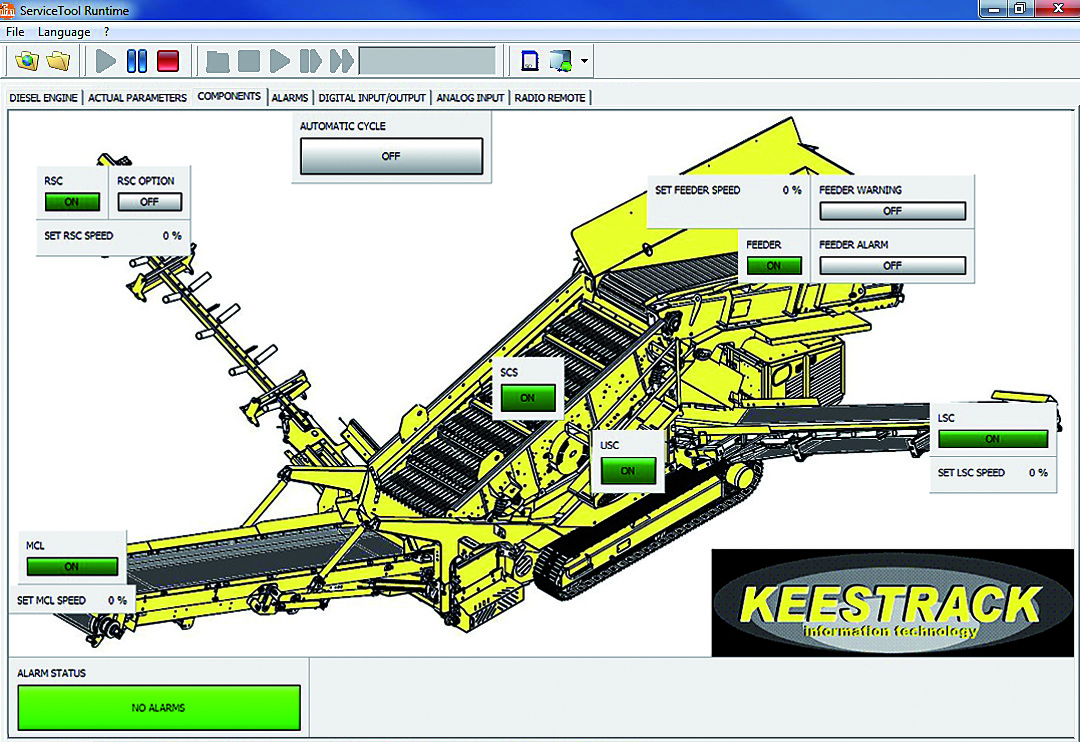
Linked to the Relytec controls of Keestrack machines are the new GSM/UMTS-supported machine remote monitoring systems. (Pic: Keestrack)
Its current versions offer proven models while brand new plants are available from the international manufacturer
“A high level of mobility on-site and between deployments; considerable ease of operation, and maintainability and superior cost-effectiveness, have for many years been the guiding principles in cross-technology development of mobile processing technology at Keestrack,” says the company.
“Especially in the medium output range between 250-300tonnes/hour, with frequently changing construction-site deployments, Keestrack plants lie primarily within transport weights and dimensions not requiring authorisation and guaranteeing operators good machine performance thanks to a high level of flexibility and low transport costs.”
The company says that modern, specially adapted Relytec-SPS systems, control and monitor all operating functions reliably, and it is now offering the option of GSM/UMTS-supported remote monitoring with GPS satellite positioning for all its machines, permitting real-time access to the machine data and functions.
Its own web portal enables the management of machine and location data and the operational recording of operating sites (geofencing).
“Keestrack’s offering of economically efficient and environmentally friendly alternative drives are currently state of the art in the segment of track-mounted processing technology of up to 60tonnes: Today, a total of seven series of crushers, screeners and track-mounted stockpile conveyors have modern ECO FS diesel drives with efficient load-sensing hydraulic modules for power units and crusher functions.”
According to Keestrack, these potential fuel savings of approximately 30% over conventional drives. Currently five screening plants, two stockpile conveyors and two crushing plants are also available in a diesel-hybrid ECO-EP version with a diesel generator and electrical operating gear, or in an ECO-EP+ version with an additional mains connection (plug-in).
“While the fuel savings of the ECO-EP package compared to conventional machines are approximately 53% (internal vs ECO-FS: approximately 33%), the ECO-EP+ machines save up to 79% in all-electric operational mode compared to conventional diesel-fuelled machines (vs ECO-FS: 70%),” says Keestrack.
“If the clearly lower maintenance costs compared to diesel drives are factored into this, the moderate additional costs of the ECO-EP drive packages will pay for themselves very rapidly, particularly as the flexibility of all plants as a result of which the potential on-board diesel drive is not diminished.”