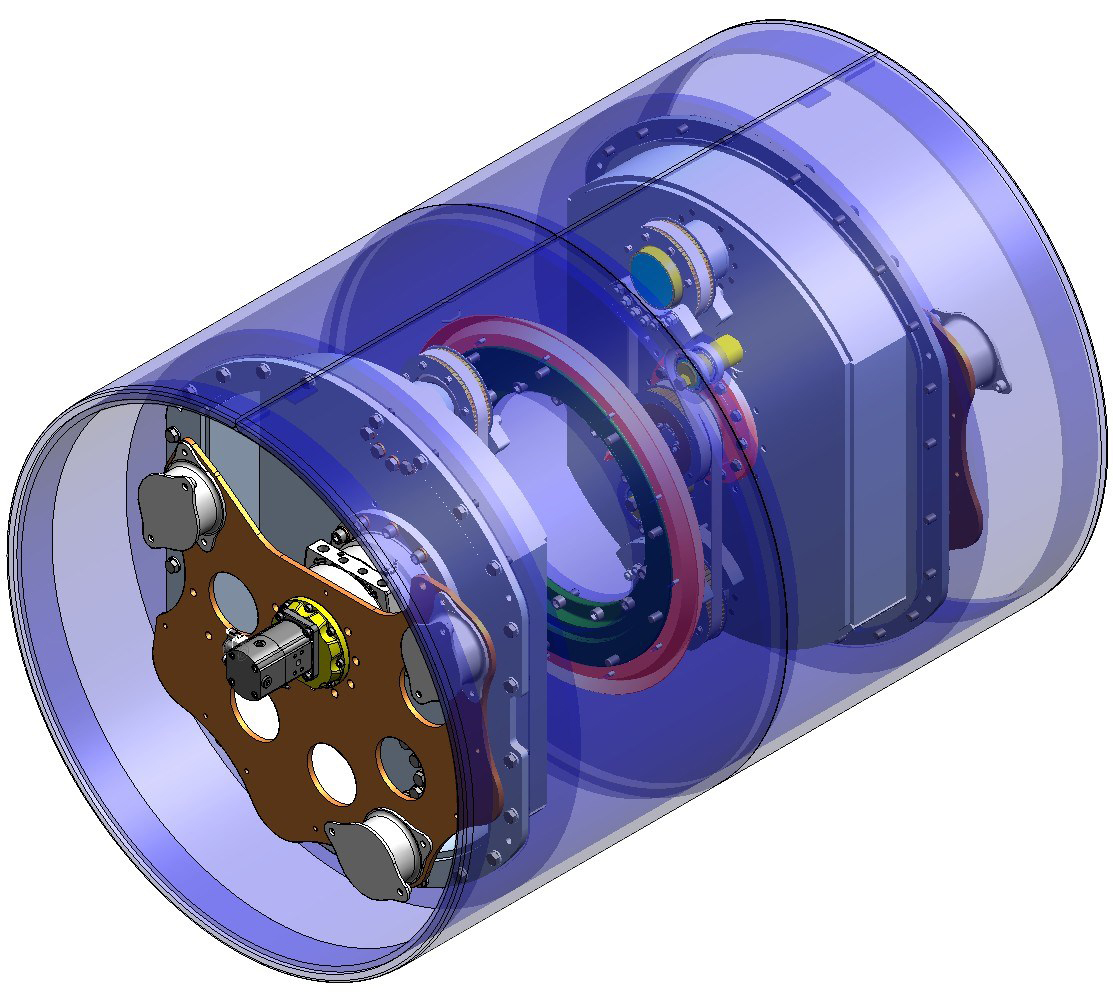
Oscillation type compaction is particularly well suited to use on bridge decks as the forces are directed at the area being worked on and are not transmitted. For the same reason, oscillation type compactors are also favoured in urban areas as the compaction forces will not generate resonances in nearby structures. Gottfried Beer is head of marketing at Hamm and said, “It’s better for thin lifts. It’s also a quality issue for on cooling asphalt. If you use vibration on cooling asphalt you’ll crush the stone, but oscillation won’t break the aggregates.”
Oscillation also suits use with mixes containing polymers that would otherwise be hard to compact, as well as in applications with faster cooling (due to high altitude or wind chill) or lower temperatures. And in addition, compactors using oscillation can work directly behind an asphalt paver as well as when the asphalt temperature drops, without risk of the aggregate being crushed.
The range of asphalt compaction machines available with oscillation now runs from the 2.5tonne compact machines, through the DV+ models up to the highway class 15tonne unit.
The system varies from the conventional vibration technology. With Hamm’s oscillation system, the drums have two unbalanced shafts rotating synchronously, driven by a toothed belt. The unbalances are offset by 180° relative to one another. As a result, the drum performs a rapidly alternating forward/backward rotary movement.
This allows the drum to direct compaction forces into the substrate tangentially to the front and rear in the form of shear forces. Unlike with vibrating drums, the compaction force acts continuously on the substrate because the drum is in contact with the ground at all times. This is why, throughout, oscillation rollers compact dynamically as well as statically with their intrinsic weight.
A new development is the availability of oscillation type machines featuring split drums. These are intended for use in urban areas where space is tight and sharper turns are required. The split drums prevent crack formation in the asphalt surface when compacting in tight curves and making pronounced steering movements. In the patented Ham system, two complete, separately powered oscillation units operate in each drum. The two drives are synchronised so that they vibrate in phase. The firm’s split oscillation vibrates with a comparatively high amplitude, delivering the same high compaction power as an undivided oscillation drum. Hamm’s split oscillation drum is said to combine all the advantages of efficient oscillation compaction with the optimised driving and steering characteristics of a split drum.
Other design benefits of the Hamm oscillation type compactors include the use of high quality steel in the drums to cope with the higher mechanical stresses on the units than for vibration type compaction. In addition, the drum edges are chamfered so as to prevent marks being left in the asphalt surface. And the exciter drive in the oscillation type compactor is also said to have low maintenance needs, lowering running costs.
Beer added, “It took 10 years before oscilaltion came through to the market but today it’s a standard technology.”