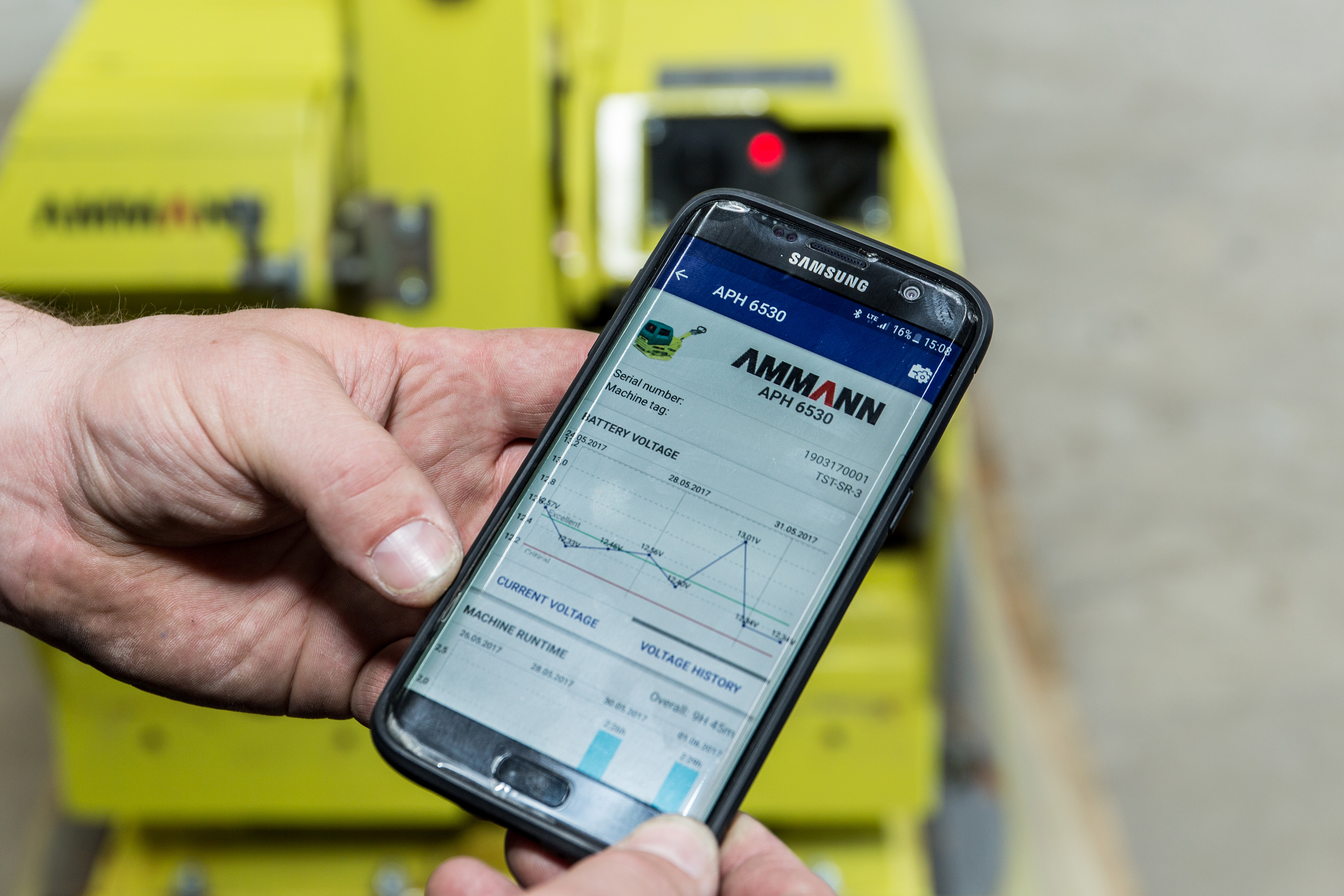
New compaction machines are coming to market from an array of manufacturers, aiming to increase output and efficiency for road contractors. One of the most notable developments is with
From
The ServiceLink relay has been an integral component of all new electric-start compactors worldwide since the beginning of 2018. ServiceLink can also be retrofitted to older machines equipped with a battery up to 30V. The system will also be offered in the firm’s heavy compactors in the future.
Meanwhile
And the compact asphalt rollers in the 3-5tonne class now offer dual amplitudes. This new feature allows the BW 135 AD-5 and
BW 138 AD/AC-5 models to be used for a wider range of applications. A rotary switch allows the operator to switch between amplitude. On a variety of applications, the high amplitude of 0.5mm provides fast and economical compaction. The lower amplitude of 0.2mm in the front and rear drums provides more sensitive compaction of thinner layers and minimises the risk of crushing aggregates. A four-cylinder
From
The company is also offering different vibratory options including Oscillatory Vibration, Dual Amplitude, Dual Frequency, Versa Vibe, and Five Amplitude systems. The Versa Vibe system provides a 2-in-1 machine with four amplitudes and two frequencies. This has two settings for lighter hitting and higher working speeds on thin lifts; and two settings for heavier hitting, and slower speeds, on thick lifts or those with challenging mixes. The five-amplitude system offers a wide range of amplitudes with a single frequency, while the two amplitude, two frequency system offers thin lift, thick lift compaction. These proven vibratory systems are now complemented by the combination of vertical vibration in the front drum and Oscillatory vibration in the rear drum.
The oscillatory system uses a pod-style eccentric weight technology developed by Caterpillar and offers a two-year/2000-hour service interval. The novel belt-drive is said to deliver twice the load capacity of timing belt systems.
Other features include a newly designed centre-articulating hitch said to ensure mat contact and a smoother ride over uneven surfaces. An offset hitch option extends coverage up to 170mm for operation next to obstacles such as kerbs and gutters. Power comes from a Cat C4.4 engine rated at 106kW with Eco-mode and automatic speed control.
Moving down the range, the new CB1.7 and CB1.8 weigh in at 1.7tonnes and 1.8tonnes respectively. The machines are said to be easy to operate and transport, with a single point lifting option and durable hitch design. The foldable ROPS option allows the machine to move under and around low structures. The high amplitude vibratory system combines with large diameter drums and an eccentric weight design to deliver high compaction performance.
One of the most innovative launches for the compaction machine market has come from Hamm, with its novel HD+ 90i PH hybrid tandem roller now being offered as a production model. This follows extensive testing of the hydraulic hybrid package in on-site conditions in various countries. The drive system for this 9tonne compactor combines a conventional diesel with a hydraulic accumulator package. The diesel engine provides most of the power to drive the machine and the hydraulic accumulator then cuts in for peak power requirements. The system offers savings on fuel, as well as operating costs, with the same compaction performance as a standard machine.
Several variants are available, including: double vibration (VV); double vibration with split drum (VV-S); one oscillation and one vibrating drum (VO); one oscillation and one split vibrating drum (VO-S); as a combi roller (VT); and as a combi roller with split vibrating drum (VT-S).
In addition, Hamm is offering an improved version of its GRW 280i rubber tyred asphalt compactor. The company has equipped the new model with a Tier 4 emissions compliant diesel as well as the firm’s sophisticated Easy Drive control system. It has a high seating position, large cab glass area and sloping engine cover, helping to ensure a good field of view.
The firm’s Easy Drive system was first fitted to the firm’s DV+ asphalt compactors but is now being installed on other machines such as the GRW 280i. The system has a small number of switches while all Easy Drive rollers have a steering wheel. Drive control is by joystick with push-button switches on the armrest. All the control systems on the firm’s compactors share a similar layout.
Modifications have been made to the ballast space between the wheel sets and the open-bottomed compartmented frame. Prefabricated steel, magnetite or concrete ballast bodies can be inserted or removed using a fork-lift truck. The machine has a hydrostatic rear-axle drive, allowing precise speed control. The GRW 280i also has a redesigned front steering axle with disc brakes while an optional anti-slip control ensures traction when working on uneven ground as well as on surfaces with varying temperatures. A novel suspension system is said to optimise weight distribution.
Power comes from a Tier 4 Final compliant four-cylinder diesel, delivering 85kW that features DOC and SCR emissions control equipment as well as automatic regeneration. The firm will offer a Tier 3 variant for use in developing markets.