Marini’s new eTOWER asphalt plants are said to complete the firm’s Top Tower line-up. The existing Top Tower plants offer capacities of 280-400tonnes/hour and the eTOWER machines are designed with output of 150 and 180tonnes/hour. The units benefits from features used in the Top Tower range such as the drying/filtering tower system. This features as innovative location for the filter and under-filter hopper, above the dryer drum, which is said to help reduce energy consumption. This modular plant can be sup
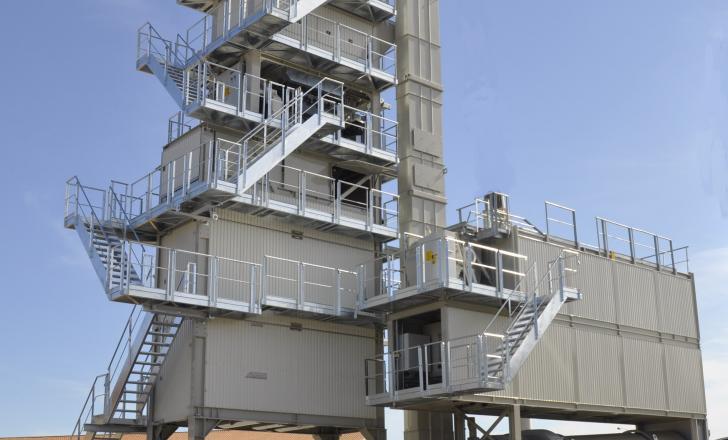
Marini’s sophisticated new eTOWER plant offers high versatility
The design of the heating system optimises the gas circuit and unlike conventional systems, the duct between the dryer and filter is short and insulated, which minimises energy loss. The recovery fines circuit is said to be highly efficient. The fines are collected in the under-filter hopper by gravity and then conveyed to the fines weighing hopper either directly by screw or by a fines elevator. The bigger fines collected in the pre-separator are conveyed by gravity to the inlet of the hot elevator. Both these innovations eliminate the need for many screw conveyors and therefore result in considerable savings both in terms of power consumption and maintenance costs.
Efficiency is further improved as the energy given off by the dryer is recovered. Captured by the under-filter hopper, the energy released by the dryer drum keeps the recovered fines in a hot atmosphere. The eTOWER is also fitted with a new-generation screen designed with ergonomics and safety constantly in mind. Access to the screen grids is easy and, above all, each grid can be replaced without having to dismantle one or more of the other grids beforehand. This exclusive advantage means that these maintenance operations can be carried out in record time, without encroaching too much on operating time.
A highly important feature is that the eTOWER can use all modern recycling systems. There are two systems for introducing RAP: a recycling ring and direct introduction in the mixer via a specific elevator. Their combined use means that recycling rates of nearly 50% can be achieved. For even higher recycling rates, the plant can be equipped with an additional parallel dryer drum for RAP. Another important capability is warm-mix asphalt production, whether involving the injection of liquid or solid additives, foam bitumen generation or specific introduction cycles of materials. The eTOWER 2500 is fitted with the AQUABlack foam bitumen production system, so the final asphalt temperature can be cut by more than 30°C due to its patented Foaming Gun, in complete serenity.
Highly versatile, the machine comes with factory-integrated electric wiring and is in compliance with the new European safety requirements. The model presented is a storage-under-mixer design, equipped with ProfiBus technology and mounted on metal foundations for quick assembly and dismantling.
Stand: F10.1008/1
%$Linker: