It was reportedly a logistical challenge to collect a massive front shovel excavator from the open pit coal mine Calenturitas de Prodeco in north-eastern Colombia.
The twin engines of the 290-tonne O&K RH 120-E mining excavator had given up the ghost and could not be repaired on site, leaving the monster stranded atop a high mound of earth.
So the mining company contracted heavy haulage specialist Boom Logistics to collect the excavator and transport it to the repair shop 22km away.
http://www.goldho
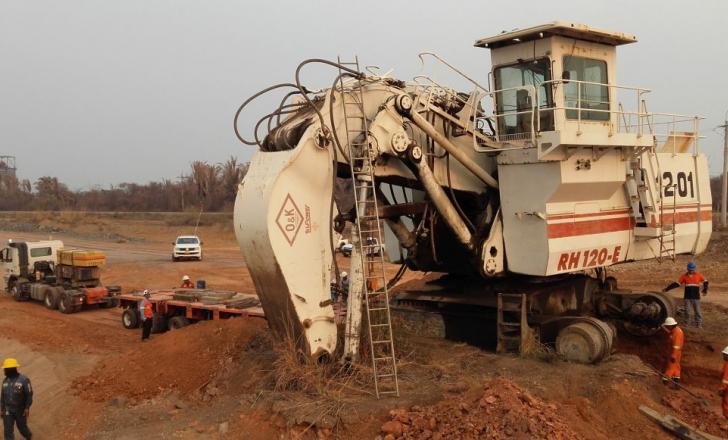
Maneuvering the module underneath the shovel
It was reportedly a logistical challenge to collect a massive front shovel excavator from the open pit coal mine Calenturitas de Prodeco in north-eastern Colombia.
The twin engines of the 290-tonne O&K RH 120-E mining excavator had given up the ghost and could not be repaired on site, leaving the monster stranded atop a high mound of earth.
So the mining company contracted heavy haulage specialist %$Linker:2 External <?xml version="1.0" encoding="utf-16"?><dictionary /> 0 0 0 oLinkExternal Boom Logistics Visit www.goldhofer.de website false http://www.goldhofer.de/en/rescue-for-a-mining-excavator,320.html false false %> to collect the excavator and transport it to the repair shop 22km away.
The job required a 12-axle THP/SL heavy-duty combination from1449 Goldhofer. Goldhofer is a German-based manufacturer of heavy-duty modular trailers and hydrostatically powered modular transporters. It products can shift loads weighing between 50-10,000 tonnes.
First off, extensive preparations were needed for loading the axle lines because of the difference in height between the mining excavator and the transport system.
As a first step, the earth had to be extracted from under the excavator – with the greatest possible care – to create enough space for the heavy-duty module to be maneuvered into place ready to take the load. When enough material had been removed, the excavator was left standing with just the wheel hubs sitting on the earth, while the rest of the pile had all but disappeared.
The next step was to position the THP/SL underneath the excavator and use the hydraulic suspension stroke to take the load. With the excavator safely loaded, the remaining earth was removed on either side so that the heavy-duty module was left standing free.
A dump truck and a pusher were then used to maneuver the transporter with its load across the uneven ground to the road where two tractors were waiting to tow the mining excavator to the Calenturitas de Prodeco repair shop.
Such transports are made possible by the use of so-called axle lines, such as made by %$Linker:2 External <?xml version="1.0" encoding="utf-16"?><dictionary /> 0 0 0 oLinkExternal China Heavy Lift Visit Youtube page false http://www.youtube.com/watch?v=5kr4I2hQoKY false false %>.
The 120-E machine was built by Orenstein & Koppel, a heavy equipment manufacturer that also produced railway rolling stock. The business was founded in Berlin in 1876 but by the 1960s its sales had declined. Canadian transport manufacturer Bombardier picked up its rail business while in 1999 its construction equipment division was sold to the New Holland Construction, then part of the1243 Fiat Group.
In 1998,1222 Terex bought O & K Mining, the division %$Linker: 2 External <?xml version="1.0" encoding="utf-16"?><dictionary /> 0 0 0 oLinkExternal making large hydraulic mining shovels Visit www.youtube.com false http://www.youtube.com/watch?v=Na42gfexwkU false false %>, including the RH120-E.
The twin engines of the 290-tonne O&K RH 120-E mining excavator had given up the ghost and could not be repaired on site, leaving the monster stranded atop a high mound of earth.
So the mining company contracted heavy haulage specialist %$Linker:
The job required a 12-axle THP/SL heavy-duty combination from
First off, extensive preparations were needed for loading the axle lines because of the difference in height between the mining excavator and the transport system.
As a first step, the earth had to be extracted from under the excavator – with the greatest possible care – to create enough space for the heavy-duty module to be maneuvered into place ready to take the load. When enough material had been removed, the excavator was left standing with just the wheel hubs sitting on the earth, while the rest of the pile had all but disappeared.
The next step was to position the THP/SL underneath the excavator and use the hydraulic suspension stroke to take the load. With the excavator safely loaded, the remaining earth was removed on either side so that the heavy-duty module was left standing free.
A dump truck and a pusher were then used to maneuver the transporter with its load across the uneven ground to the road where two tractors were waiting to tow the mining excavator to the Calenturitas de Prodeco repair shop.
Such transports are made possible by the use of so-called axle lines, such as made by %$Linker:
The 120-E machine was built by Orenstein & Koppel, a heavy equipment manufacturer that also produced railway rolling stock. The business was founded in Berlin in 1876 but by the 1960s its sales had declined. Canadian transport manufacturer Bombardier picked up its rail business while in 1999 its construction equipment division was sold to the New Holland Construction, then part of the
In 1998,