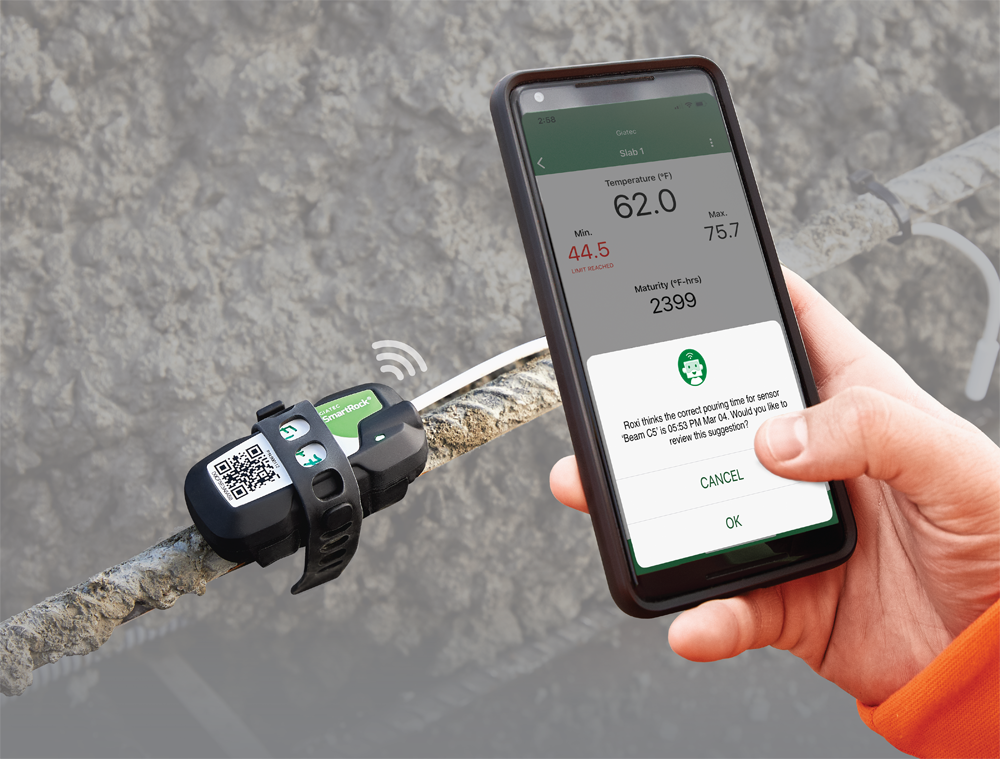
Concrete technology testing company Giatec has updated it artificial intelligence (AI) programme, Roxi, with the ability to spot unexpected changes in a concrete mix. Roxi is linked up to Giatec’s SmartRock maturity sensors, so if the concrete is curing in a way that doesn’t match the curing pattern of the designed mix, it will send out an alert.
Giatec worked with three concrete suppliers – Stoneway Concrete, Central Concrete (a US Concrete company), Maschmeyer Concrete Company of Florida, Hilltop Concrete, and Tomlinson – on its development. Roxi is reducing the time needed for testing and giving early alerts if something about the mix changes; for instance, if one of the components is slightly different.
Giatec plans for Roxi to keep gaining intelligence. “Roxi is the Alexa of concrete,” said Aali Alizadeh, co-founder, president and CTO at Giatec. “We launched this product last year with a bigger vision in mind.”
Giatec introduced its SmartRock sensors to the industry back in 2015. They work by measuring the temperature of the concrete pour as it heats up and cures and correlating that to the concrete’s strength. Each SmartRock sensor sends information back to a node and the strength and temperature can be viewed by users via an app.
The idea behind maturity sensors such as SmartRock is that they give contractors a more accurate picture of strength build-up in a concrete pour. This can allow them to strike formwork earlier than planned, potentially cutting time from the duration of a project and, hence, saving money. To date, SmartRock has been deployed on over 6,000 projects in North America, East Asia, South Africa, South America and Europe.
However, many contractors lack confidence in using concrete maturity sensors. “People don’t trust it,” said Alizadeh. “They say ‘What if the calculation is wrong? What if the sensor is wrong?’” By training Roxi to spot anomalies and errors, Giatec hopes to win over distrustful contractors.
The first development phase for Roxi was to train it to automatically know when to start measuring from: that is the time the sensor is completely enveloped in concrete. Giatec partnered with leading AI institution the Montreal Institute of Learning Algorithms (Mila), creating an algorithm which could spot when the temperature of the sensor started to rise and hence log the start time for measurement.
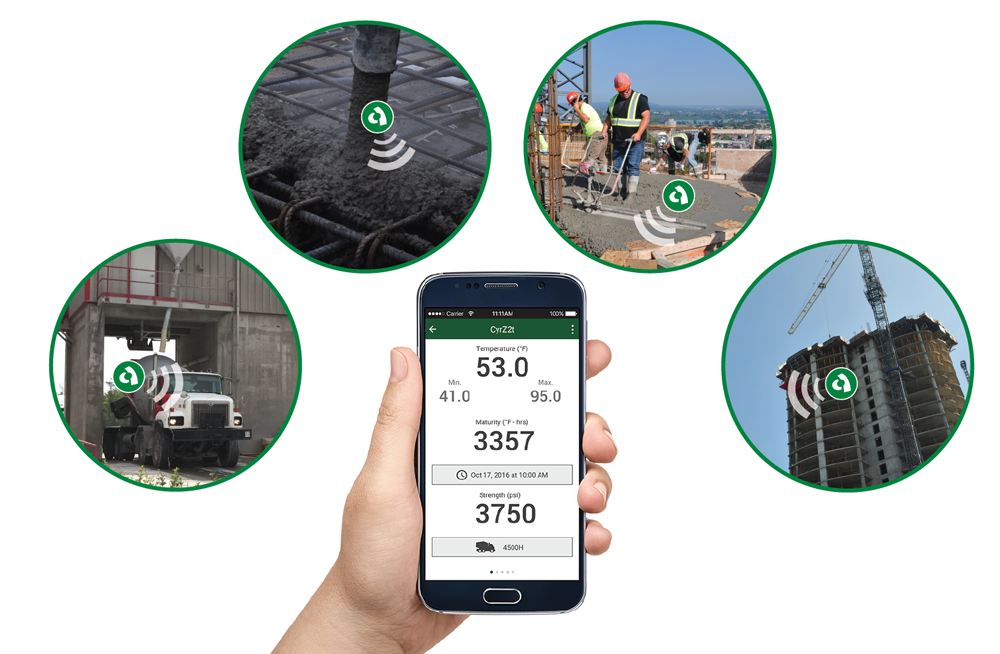
At the time, Roxi had data from around 2,000 projects to learn from. “The algorithm looked at the set of data points and learned what ‘pouring time’ means,” said Alizadeh. “It learned how the temperature looked before and after the pouring time.”
Roxi also surprised her parents. “Roxi learned things we could not believe,” said Alizadeh. “For instance, specialist cases where the concrete only generates low heat, where we couldn’t see from the curve where the pouring time was, Roxi can detect it.”
Before Giatec introduced Roxi, its SmartRock app would prompt users to input the start time for each sensor. Now Roxi suggests what it believes the smart time to be so that users can agree or correct – all information which is fed back into the machine learning.
“Initially, some of our users noticed that before they had selected the pouring time, Roxi gave a good answer,” said Alizadeh. “Now, some don’t even enter the pouring time, they just leave it to Roxi. That was really exciting to us…to find out that a conservative industry was trusting an AI algorithm to do the thinking for them.”
The second phase of development for Roxi, announced by Giatec in March 2020, allows the algorithm to look at the maturity calibration – the way the heat of hydration is supposed to develop against time – and compare it to what is actually happening onsite. If there is a significant difference, Roxi raises the alert.
Differences could be due to small changes in the composition of the cement, the aggregate or even additives. Or, it could be that a new mix was being used, but the maturity calibration had not been updated due to human error.
Giatec worked with its concrete supplier partners because it needed good data to be able to train Roxi accurately. “In any AI development, the challenge is the data, to have a large enough amount of clean data,” said Alizadeh. “As the saying goes, if you put garbage in, you get garbage out.”
Giatec sells its SmartRock sensor package directly to contractors, but it also sells them through concrete suppliers via its Smart Plus Platform. This means that the suppliers take responsibility for calibrating the sensors to match the mix and checking that their mixes conform.
“They are responsible for keeping the maturity calibration up to date,” explained Alizadeh. “Roxi is now enabling them to check the calibration on an ongoing basis.”
“It is a value added for the mix producers when they compete against each other,” added Dobrila Moogk, Giatec’s VP of marketing. “They have these tools at their fingertips that can provide peace of mind.”
Giatec now has in-house AI experts and is already working on the next phase of Roxi’s development. In the future, the algorithm will be able to compare readings from different sensors in a pour and provide information based on differences it finds.
Looking at the bigger picture, there is even more value to be found from linking up data from the different parts of the concrete supply chain. “As the largest industry in the world, there’s an abundance of data, billions and billions of data, but there’s not enough integration between all the data we collect as an industry,” said Alizadeh. “That’s a huge opportunity.”