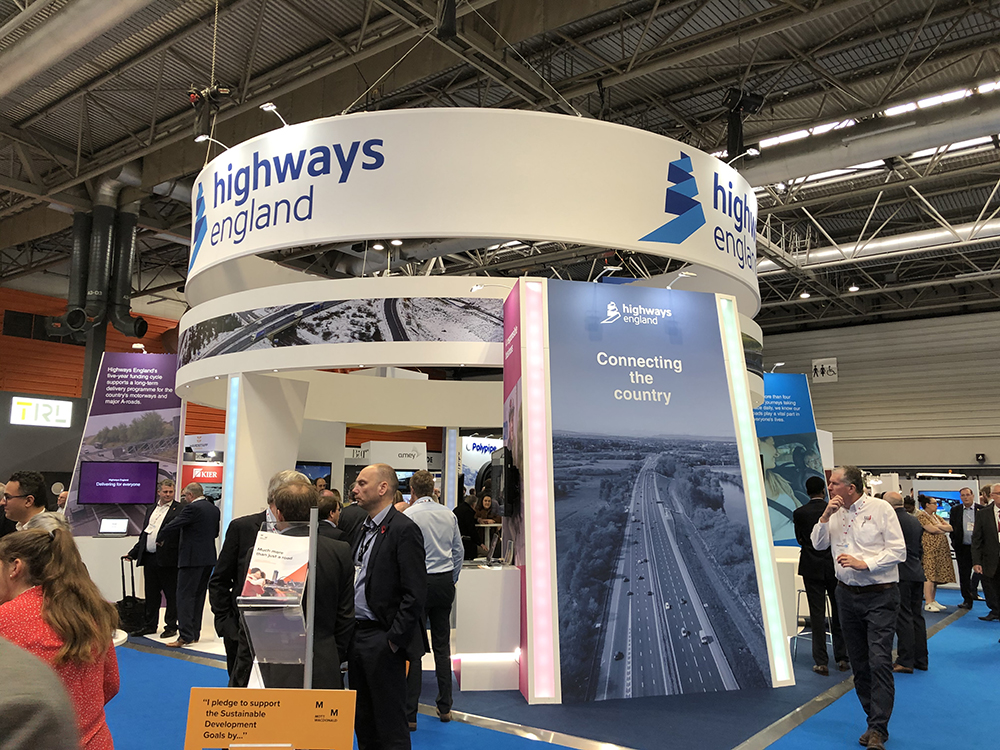
Safety concerns over smart motorways and climate change issues were key features of this year’s two-day Highways UK conference and exhibition.
Many of the “Big Thinking” presentations on day one, including opening speeches, focussed on environmental issues.
A number of presenters highlighted the performance of the UK’s several national highways agencies and organisations. Much scrutiny took place of England’s national road agency Highways England (HE) over the past four years. The government’s stand-alone company is nearing the end of the first five-year Road Investment Strategy (RIS 1) in which £15 billion (US$19.25 billion) was ringfenced for Highways England use. There was no longer to be any poaching of monies by the UK’s rail authorities to maintain the train network at the expense of the road network.
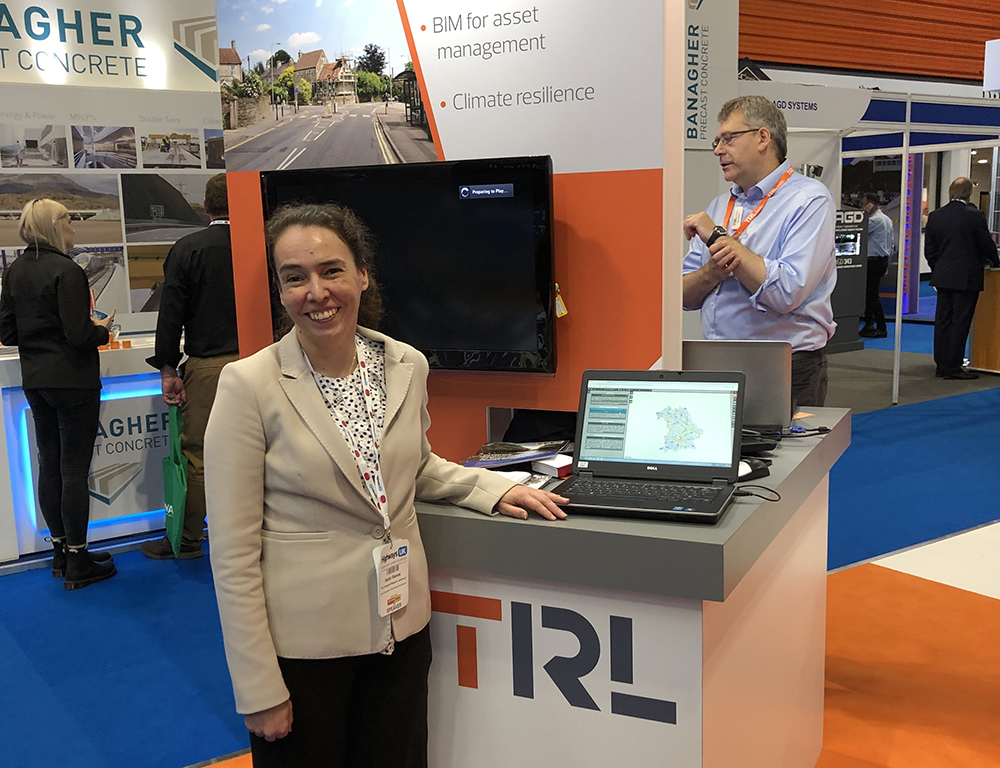
An increasingly important – “tricky” – issue for HE is the move towards so-called smart motorways, said Anthony Smith, chief executive of Transport Focus, a watchdog for road users throughout all the UK. But how safe is safe when the hard shoulder becomes another running lane? That question hits at the raison d’etre of Highways England with its remit to provide an Strategic Road Network (SRN) of safe, reliable and smoothly running roads.
Smith noted that a portion on the public needs more evidence and convincing that smart motorways are safe, especially in light of media reports of deaths on them. Even so, he says, surveys show an 83% satisfaction rate for the condition of England’s SRN. Contractors, too, are increasingly happy with the relationship between them and their HE client.
Innovation
Climate change issues were key themes in many of the smaller presentation venues. In 2010, there were around 300 transport research papers looking at resilience – mostly from a terrorist attack perspective. That number has risen dramatically says Sarah Reeves, senior consultant with the UK-based research group TRL. The term resilience now includes much more than terrorism - increasingly it includes climate change. There have been more than 2,100 papers on resilience published in the past year or so, says Reeves, pointing to a graph in the recently published TRL primer called Roads: an industry guide to enhancing resilience (of which she was a co-author).
With regards to climate change and transportation strategies, action must be taken today to mitigate severe weather patterns in the future, but envisioning five years down the line is not enough anymore. “We have to get people to think much longer term,” says Reeves. By longer term, she means up to the year 2100 and TRL is in the final stages of readying a software package to do just that.
Reeves was demonstrating on the TRL stand the DeTECToR package (Decision Support Tools for Embedding Climate Change Thinking on Roads). DeTECToR is a risk assessment tool funded under the Conference of European Directors of Roads (CEDR) transnational research programme and co-ordinated by herself at TRL. It should be available by the middle of next year as a service to European road authorities that are members of CEDR.
Based on data collected over time, the package can draw up risk assessments of possible climate scenarios that could affect transportation infrastructure. Landslides blocking roads and flooded highways after heavy rain storms, deterioration of assets due to heavy snowfall and pavement cracking because of heatwaves are considered in extrapolated scenarios.
Redefining road barriers
Polysolar is a Cambridge, UK, manufacturer of photovoltaic glazed panels for buildings since 2007. The company recently took its tried-and-tested technology and applied it to a sound and pollution barrier prototype, according to Hamish Watson, Polysolar chief executive.
A 10m section of Polysolar barrier is being tested in front of a roadside picnic area in the southern US. The barrier reduces sound – a 13dB drop - across the rest area. Because of its shape, the barrier also guides back onto the road the airborne particulate matter that otherwise would drift into the picnic site.
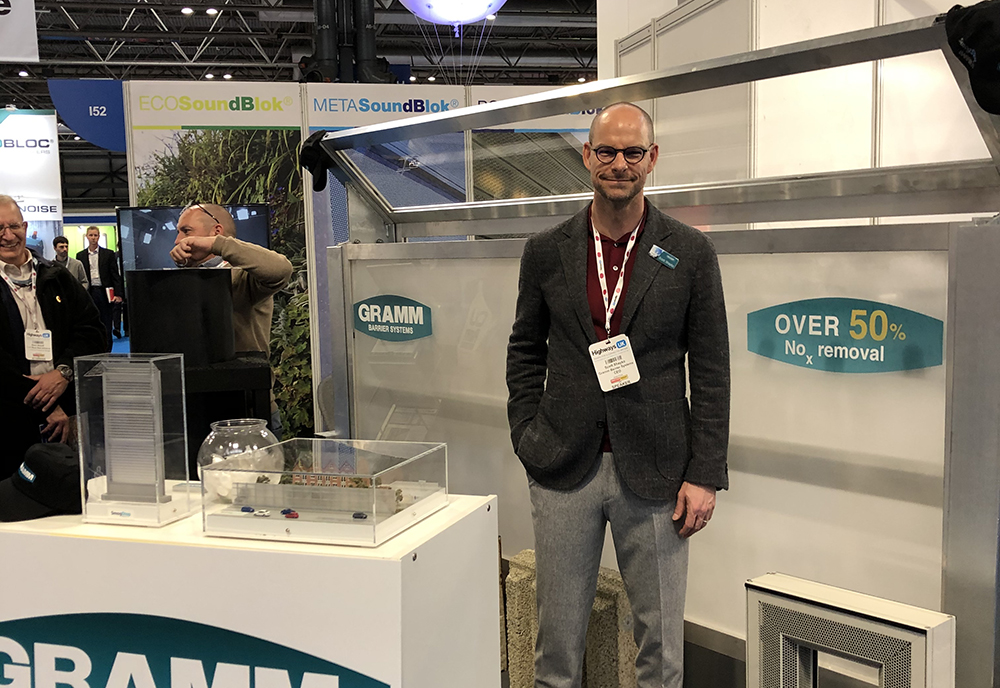
The third and most important aspect of the barrier, says Watson, is that a length of the barrier will generate enough electricity to constantly feed several nearby electric vehicle refuelling stations. A 1km-long 4-5m-high barrier is estimated to constantly generate up to 400kW of electricity. Given the fact that electricity is sold, the barrier will have a return-on-investment period, says Watson. It would then be a profit centre for road authorities, depending on how much barrier is installed and how much electricity is sold to electric vehicle drivers.
Much emphasis has been placed on reducing noxious emissions (NOx) from road engines and much progress has been made, says Ross Hunter, a researcher with environmental consultancy Temple Group, during his presentation. But there remains the growing problem of particulate matter – not from engines but from non-exhaust sources such as tyre wear, road abrasion and brake use, says Hunter.
Particulate matter of 2.5 microns (PM2.5) is light so it is carried far afield. Unfortunately, it is also extremely harmful for people, triggering or worsening chronic disease such as asthma, heart attack, bronchitis and other respiratory problems. Overall PM2.5 emissions have dropped drastically since 1990, from 29.5kt (kilo tonnes; 1,000 tonnes) to around 13kt in 2017. This is because of reduced exhaust emissions, thanks to government legislation.
However, the amount of PM2.5 from non-exhaust sources has risen in that time, from 6.5kt to just over 8kt. Across Europe there is no legislation – nor is any planned – to reduce PM2.5 from tyre wear, road abrasion and brake use. This has to change, says Hunter.
Helping to resolve that dire situation is one Canadian company that uses photocatalytic technology to break down NOx and particulate matter. Wind tunnel tests have shown that the SmogStop barrier can reduce monthly NOx levels by up to 54%, according to Scott Shayko, chief executive of Envision², based in Guelph, Ontario.
SmogStop – marketed in the UK by UK-based Gramm Barriers – also acts as a sound barrier, thanks to its acrylic material. The barrier’s design directs emissions into a channel and over a photocatalytic coating that treats the pollutants. The design also generates vortexes to boost the mixing of emissions with clean air to reduce pollution concentration levels.
Pedal power
As local road authorities install more cycling lanes, there is an increasing number of kilometres that have to be inspected, explains Robert Fox, commercial manager with surveying specialist Ginger Lehmann - the former transportation surveying division of asset software company Yotta and based in Warwickshire, northern England. On display at the company’s stand was a recumbent tricycle equipped with cameras and data collection systems for visual surveying of cycle paths.
It was the first time on display in the UK for the trike that came from Germany where it is seeing service with many local authorities. An easy pedal rate is around 20km/h and the machine is adjustable to fit any size of person, said Fox. Cameras front and back focus on the ground and also give rear and frontal drive views. They can also take in street furniture as the trike passes along a path.
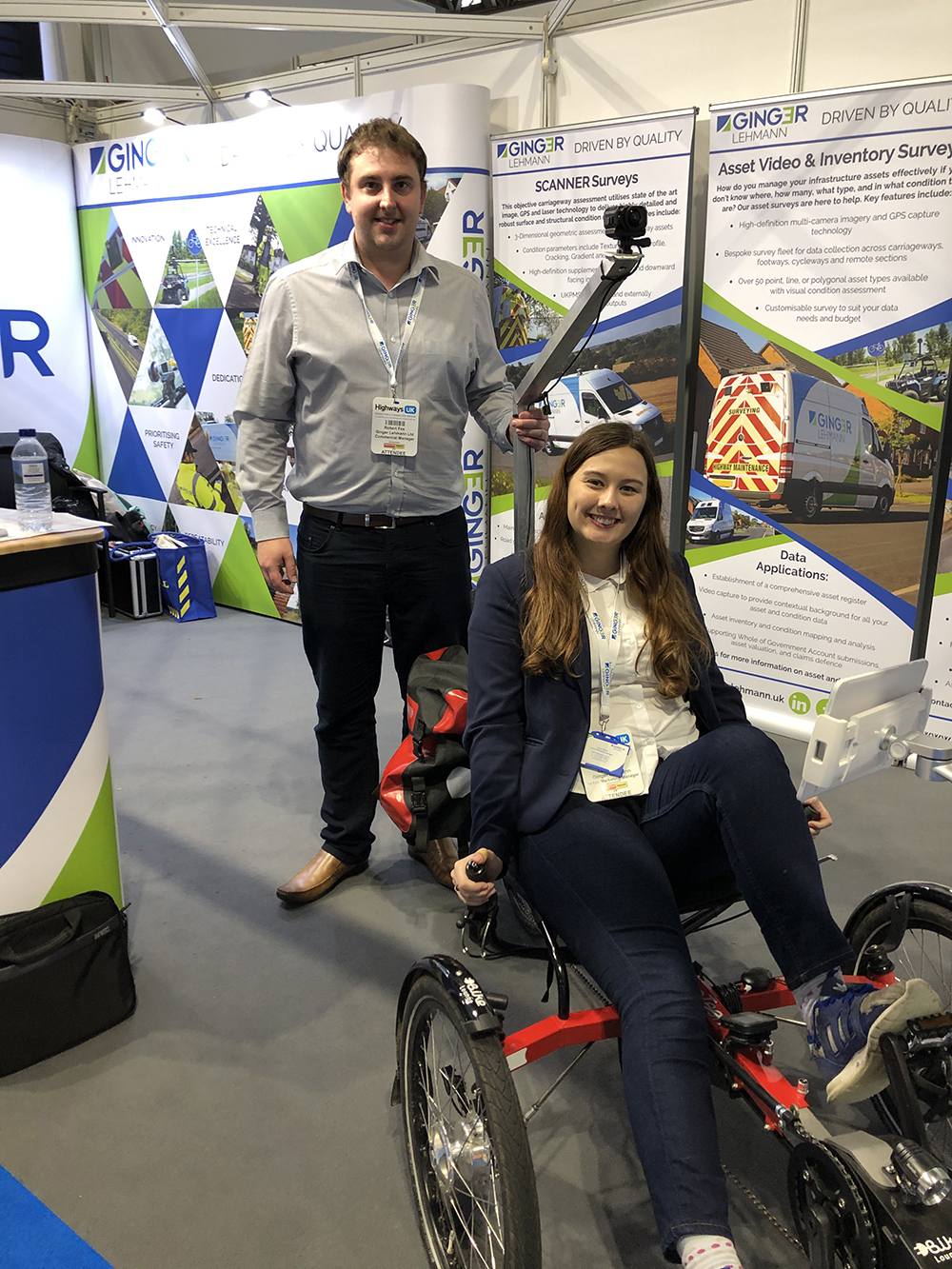
With the apparent increased risk to roads from flooding – a major flood occurred in England a week after Highways UK ended – drainage companies were in obvious attendance. Shimpac was highlighting its proven drainage cover system. Its boasts environmentally friendly material composition, notes Ian Wallington, business development manager.
Shimpac planks, collars and bungs are a combination of compressed cement (70%), treated wood fibres (15%) and propriety bonding materials. Cement is the predominant material by weight. Small amounts of chemicals are added to the wet mix cement mainly for accelerating setting.
For roadside drainage systems, UK-based Concrete Canvas had a flap of its “concrete-on-a-roll” for visitors to its stand to pick up and examine. While ideal for roadside installation, it also has been used extensively for landslide prevention as a reinforced soil wall next to highways, says Gavin Adams, a technical expert with the company. Once laid down, hydration is done by spraying water over the surface.
Adams said around 80% of production is exported from the UK and the system is especially useful for projects in remote areas. For example, helicopters can fly rolls of the material into regions where few if any roads exist. Ordinary power tools will cut the material to specification size and steel pegs secure the mats before water is applied.
Meanwhile, Stanton Bonna - part of the Consolis group based in the UK – has developed an offsite manufactured modular linear drainage system. The Aqua-Slot is made of precast concrete, explains Neil O’Sullivan, business development manager at Stanton Bonna. The system has been especially efficient when traditional slipforming on site is difficult because of traffic circulation around the works areas.
A crane lifts the sections into place and aligns the joins. Also, situating Aqua-Slot can be done in practically any weather – hot, cold, dry, wet. A well-practiced team of three can lay around 200m per day. Sump unit and associated ironworks are built into the precast section, meaning there is little follow-up work.