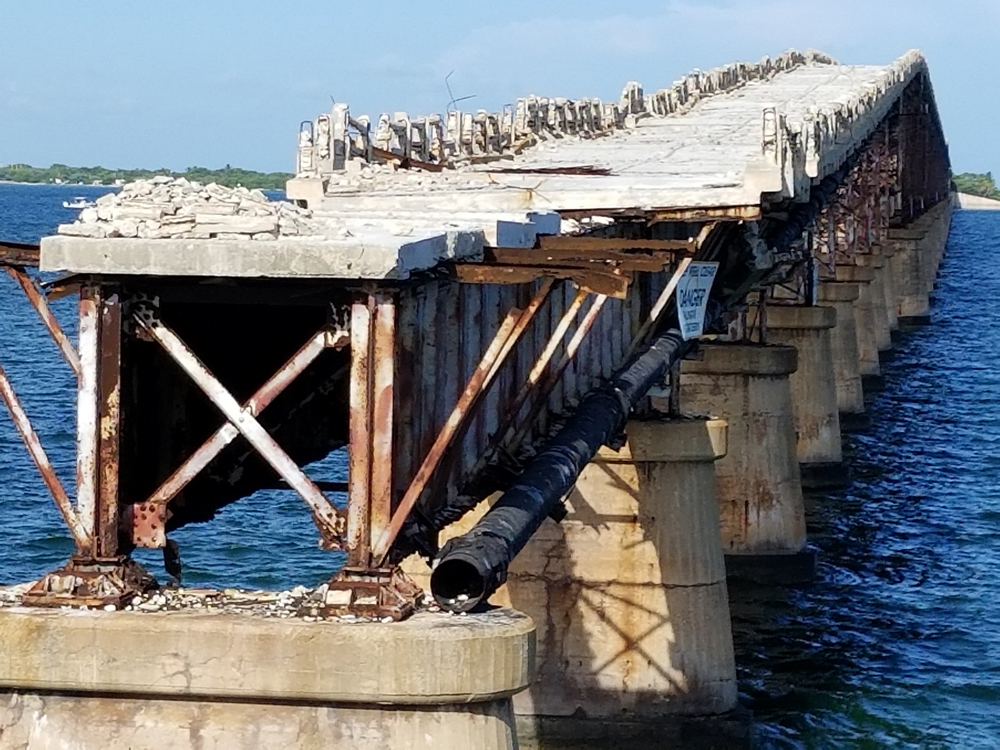
Bitumen and bituminous products such as asphalt soften as the temperature increases and can lead to road surface deformation. However, a couple of degrees in pavement temperature plays a relatively minor role in the overall performance of bitumen.
To put it in perspective, in the US bitumen specification system, the temperature differences between two grades of bitumen is 6°C, as measured during the hottest week of the year. This means it would take a significant rise in temperature as a result of climate change for different grades of bitumen to be necessitated.
In many regions of the world, the increase of moisture in road structures and more frequent flood events, whether due to increase in rainfall, or sea level rise, pose the greatest threat to road infrastructure.
Moisture-related pavement and road failures following severe rainfall events or floods can be costly to repair. As an example, the 2010–2013 floods in the Australian state of Queensland cost the government nearly US$5 billion in road repairs - half for reconstruction of pavements.
Other more localised climate change-related risks to road infrastructure include increases in the occurrence of landslides, rockfall and avalanches, drought, bush fires and loss of physical support due to melting of permafrost.
Mitigation strategies are highly dependent on local conditions and the original structure of the road. Thick road structures in urban areas are typically more flood and moisture resistant than rural roads. However, there may still be a need to improve drainage or increase the road level to new flood safe levels. This is because critical rainfall patterns and flood risk for which the road was built may have changed since the original design.
In rural settings where roads carry less traffic, road structures tend to be shallow and more prone to moisture and flood damage. For these roads appropriate drainage is even more important than for their urban counterparts.
Many countries, especially in the developing world, have a large proportion of unpaved gravel roads in rural areas. These are particularly vulnerable and climate adaptation strategies include paving the road surface, often with a sprayed seal.
Cost-effective measures to improve the flood resilience of rural roads include stabilising the road base using foamed bitumen. In Queensland, this technology is used in regions receiving more than 500mm of rainfall annually. This measure proved its worth during Cyclone Debbie in 2017 with only minimal remedial works required on pavements stablised with foam bitumen.
Australia is not alone in this regard; Governments across the world are developing strategies to mitigate the impact of flooding. But to achieve the most successful and desirable long-term outcomes, companies such as Puma Bitumen must work in partnership with transport departments.
To avoid the bitumen industry contributing to climate change itself, it is hugely important that the industry looks at ways it can reduce carbon emissions. It is encouraging to see the continued transition of our economy from a linear model (take – make – use – dispose) to a circular one (make – use – reuse – remake – recycle). Given asphalt is 100% reusable, we are well on our way to achieving the goal of a truly circular economy within the sector.
One of the best examples that demonstrates how the industry is recycling other waste materials is the use of tyre-derived crumb rubber modified binders. Puma Bitumen has been using this sustainable and resilient technology to provide improved performance in sprayed seals and asphalt, especially in severe and challenging conditions.
Increasingly, road authorities are investigating opportunities to use these high-performance crumb rubber binders on their road networks. It reduces waste while maintaining good quality infrastructure.
Puma Bitumen is continually striving to make our operations and materials more sustainable. We recently created OLEXOCRUMB, a binder that combines tyre-derived rubber with styrene-butadiene-styrene. It performs as strongly as conventional polymer modified binders and was used in multiple Australian state road and local government trials last year. It has now become a standard binder.
Importantly, this asphalt binder solution is sustainable, as it incorporates 10% recycled tyre rubber. Furthermore, for every tonne of OLEXOCRUMB binder produced, the equivalent of 15 passenger tyres will be recycled.
Erik Denneman is the technical manager for the Middle East and Asia Pacific with Puma Bitumen. He is a leading expert within the company’s Global Technology Centre in Altona, Melbourne, Australia. Before joining Puma, he was director of technology and leadership with the Australian Asphalt Pavement Association.