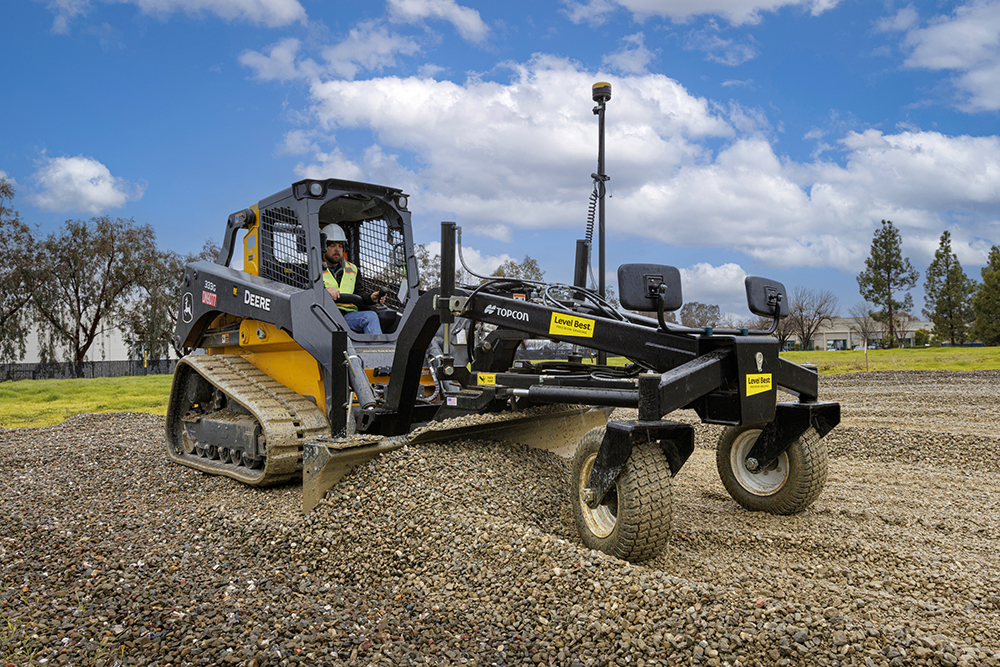
Every now and then, a really, really useful tool arrives on the market, one that will make a big difference to a company’s bottom line because it solves a problem that has been plaguing business for years. One such tool is Aptix, an integration platform that connects various Topcon and third-party software applications (see box).
“There is a challenge in the construction business of mixed fleets on site,” explains Scott Langbein, global director of Business Development and Marketing for the Integration Services team at Topcon Positioning Systems. “Each OEM manufacturer is very good at what they do with their own telematics.
“Aptix allows the telematics from different machines to be visualised and compared together. No longer does a scheduler or project manager have to log into the different manufacturers’ websites to see the data for that particular brand of machinery operating on site. This is the goal of an integration platform,” he says.
The basis for the recently launched Aptix came from within Digital Construction Works (DCW), a joint venture started between Topcon and Bentley Systems in late 2019. Earlier this year, Topcon took full control of DCW and reorganised it as a Topcon business unit, now focused on Aptix and integration services. Langbein, with more than 25 years in the positioning and construction industry, has been heavily involved in developing the global partner network and distribution of Aptix.
Langbein says that up to now, one way of finding out if site work is on track is when the billing gets done.
A subcontractor submits their employees’ timecards for time spent working on its site. If a lot of money is handed out by the client for a project that is not on schedule, this could mean something is not happening as planned. But what is that and when did it happen?
The answer can be found in the telematics of the machines: the name of machine, fuel consumption, location and engine rpm. Aptix can sort visually the work by machine, task, CO2 consumption and more. Often when demonstrating Aptix, this visual is a “stop and stare moment” for them, says Langbein. What may take days, even a couple of weeks, to see - and often on Excel spreadsheets - is now spread out in easily understood graph form. And the information is only about 15-minutes old, “pretty much real time” as far as site work goes, he says.
“For the first time, a fleet or project manager will see that one machine is outperforming the others so in future this machine could be the first choice for similar tasks.” It might be that one operator works much better with a particular manufacturer’s machine as against similar machines from other manufacturers.
“In this way, Aptix is about risk management,” he says. The risk has been reduced of having to re-grade a road or push more earth to another area on site. “It lets the contractor be more competitive because they can fine-tune their normal mode of operation, meaning they bid more accurately.” In the mid- to longer term Aptix can give a contractor a good track record, meaning that for a potential client, they are low risk when it comes to possible cost over-runs for a planned project.
In the driving seat
The companies most likely to be interested in Aptix are specialty subcontractors or a general contractor who is managing several subcontractors. “Ideally, it is the person responsible for the schedule, the planned work versus actual - someone who is concerned about keeping to schedule or a general contractor who is organising subs doing utility work or road grading work with a lot of heavy excavation. Aptix can empower such people who are responsible for this.
“Everyone knows machine telematics, it’s been around for years. Telematics data is not pretty to look at,” he says. It comes on a large Excel sheet, bunches of columns and so-called “Excel jockeys” sift through the numbers, sorting them and finding relationships.
As an integration platform, Aptix sorts the telematics data, the model data and the scheduling, bringing three ingredients into one visualisation. “I can look at all three separately, but it’s only when you combine all three into a single vision that you see relationships. And this allows vision of things that you can’t see when viewing separately. The biggest benefit is near-real time of on-site work on your project.”
CO2 visibility
Langbein readily admits that Aptix as a sustainability tool was not high up on the list of priority goals for the platform. However, after demonstrating Aptix to contractors – especially in Europe - he quickly became aware of how increasingly high up on their priority list it was to measure CO2 and emissions from the machines. Aptix, even in its present form, can be a major enabler for achieving a contractor’s sustainability goals.
At the moment within Aptix, carbon emissions are based on the time that the machine has been running. But that is not as accurate a measurement as Langbein would like. After all, how much of that time running was spent idling for some reason and not actually pushing dirt around? Or the machine could be really working hard, pushing out much more emissions.
“The next step for Aptix will be to have the CO2 emissions based on the telematics data of fuel used,” he says. “In the Netherlands, for example, if the contractor can come in under his CO2 limits as defined in the contract, the company can look forward to performance bonuses. We would like Aptix to be the document of record for the contractor getting a performance bonus. Now I’m excited!”
The future
When a customer sees a demonstration of Aptix, says Langbein, they often ask if Topcon can integrate an ERP (enterprise resource planning) system, can it connect to a billing system, or can it connect to a company’s safety data.
“There are a number of construction companies that have amassed data on their own bespoke in-house systems, for things like inspections or safety that are not the products of boxed off-the-shelf software. If these companies want [their own data] to be integrated, we can do this under integration services and it will be a bespoke solution.”
In the longer term, as autonomous on-site vehicles are developed and proven, there could be a connection. “Aptix pulls in the ingredients that an autonomous vehicle needs to know, like design model and the work schedule. It’s the schedule that has to be broken down into tasks for autonomy to work, far more detailed than for human-level tasks. But it’s going in that direction.” Aptix will follow along the development of AEMP 2.0*, he says, for semi-autonomous and fully autonomous off-road equipment.
Even before the official launch of Aptix, Langbein and his colleagues had been thinking of future refinements. In other words, Aptix is only the beginning. Topcon is looking at using it in a vertical environment, meaning construction projects that rise up from the ground – buildings, arenas, factories – and integrating it into Building Information Modelling, BIM. Data about electrical work, steel material supply, fire suppression, ventilation and other functions will need to be collected and integrated - a huge task, he notes.
*The US-based AEMP (Association of Equipment Management Professionals) has created a telematics standard to provide structure and benchmarking for the sector. It says: “The AEMP Telematics Standard, was first published as ISO 15143-3, in 2016 by the International Organization for Standardization (ISO). The standard specifies the communication schema designed to provide mobile machinery status data from a telematics provider’s server to third-party client applications via the Internet. AEMP provides this Telematics Standard Support website as a resource to help its members integrate and utilise the ISO standard for their business.”
For additional information, please go to: https://www.aemp.org/news/321367/Another-technology-step-for-AEMP-Telematics-with-newly-published-ISO-Standard.htm
Key terms/definitions
- API: An application programming interface is a computing interface which defines interactions between multiple software intermediaries. It defines the kinds of calls or requests that can be made, how to make them, the data formats that should be used, the conventions to follow, etc.
- OAuth2: OAuth is an open standard for access delegation, commonly used as a way for Internet users to grant websites or applications access to their information on other websites but without giving them the passwords.
- OEM: Original equipment manufacturer
Inner workings of Aptix
Today, GPS, sensor technology, guidance, in-cab visual control panels and telematics all help machine operators do the best job and get the best out of their equipment. Now comes Aptix, an agnostic integration platform launched globally this month as a subscription service.
Aptix raises the bar for improving project and risk management. It allows clear near-real time visualisation of machine and operator performance for project managers and project schedulers in a site office and the machine operators in the field – no matter what machines are used and from which manufacturer.
Importantly, it does this automatically by connecting various data sources on the machines to back-office analytics.
Aptix does three things. It automates distribution of schedule changes, automates distribution of model changes and automates reporting (feedback from the field) on planned versus actual work – the most challenging and most important aspect.
It is a drag-and-drop solution, via an Autodesk Construction Cloud, meaning messages are sent out to machines via the cloud. Autodesk alerts Aptix that a new schedule exists. Aptix consumes the new schedule and puts it into machine control format for distribution into the field.
With a design model change, somebody has to send out a work plan change to machines operating on site. Manually, somebody must tweak the model change data into machine change format and then physically go out into the field, with a USB stick to each machine.
Aptix automates this in a similar drag-and-drop process by dragging the design model change data into Autodesk construction cloud. Aptix engages an automatic workflow engine and automatically distributes information. The machine driver is sent an alert on their in-cab screen that the task has been updated. This process also eliminates the possibility of the operator choosing the wrong work plan or an incorrect surface model to follow due to driver distractions or even machine operation during the moment of choosing.
Aptix, as an agnostic environment, will work with all machines, thanks to Topcon’s Tierra Blend+, a tool for gathering remote machine locations, operating hours and machine information. It also allows Aptix to work with the leading construction equipment manufacturers. Visually, Aptix allows the site office to see which machine is working according to a new schedule and design and which is not. This is a quick way to alert those operators not on schedule to check their schedule.