Sinoma Cement is one of the largest cement manufacturers in the Peoples Republic of China. In 2012 the company decided to boost its aggregate production, both for its own use in cement production, and to supply aggregates to the local construction market. In order to do this Sinoma Cement invested in two aggregate plants supplied by Sandvik Construction, consisting of feeders, screens, jaw and impact crushers.
The firm’s extensive production of clinker cement is facilitated through three production lines
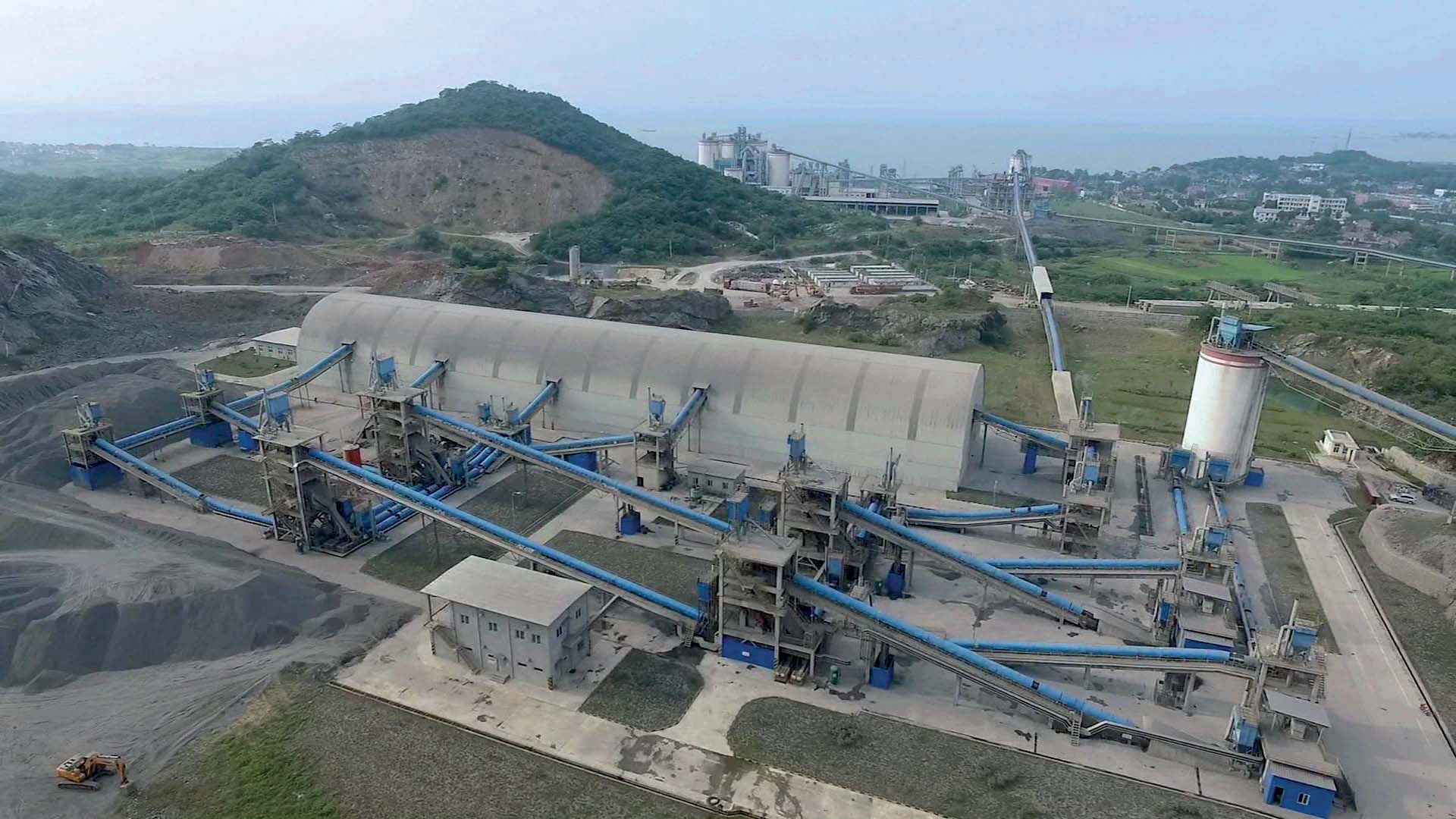
The new Sandvik equipment is helping Chinese producer Sinoma Cement meet its output needs
Sinoma Cement is one of the largest cement manufacturers in the Peoples Republic of China. In 2012 the company decided to boost its aggregate production, both for its own use in cement production, and to supply aggregates to the local construction market. In order to do this Sinoma Cement invested in two aggregate plants supplied by 2403 Sandvik Construction, consisting of feeders, screens, jaw and impact crushers.
The firm’s extensive production of clinker cement is facilitated through three production lines each with a daily output of 4,500tonnes, and with a total annual production of 5.4 million tonnes. In addition over 5 million tonnes of aggregates, in a variety of sizes, are produced annually. The firm has its own specialised wharf located at Lake Chao, which handles 3.8 million tonnes/year of a variety of aggregates and other materials for shipping to the Yangtze River delta.
Aggregate production began at the firm’s quarry site in February 2012, with the company keen to see production ramped up to 5 million tonnes annually. This would involve producing a variety of sizes for use in both cement manufacturing, and for sale to the construction industry. The plan was to construct three aggregate production lines, with two being fully operational and the third being used depending on specific market conditions.
When Sinoma (Anhui) Cement set about ramping up its aggregate output the company set high standards, both for its own operations, and from the equipment it wished to use. The designated supplier of the aggregate plants would have to supply the plant, as well as aftermarket support, proactive servicing, and plant design. The supplier had to be able to deliver the production required, deliver low energy consumption and environmental protection, as well as operator training and efficient transportation and stockpiling.
Over the period of a year the company met with various manufacturers of aggregate plant, inspecting various facilities, and meeting with technical, service, aftermarket and planning experts. Following this extensive process the final contract for all elements of the new aggregate plants was awarded to Sandvik Construction in China. This resulted in an order being placed for Sandvik to supply all the equipment, plan the processes, and support the equipment for two aggregate production lines. This comprised of two SV1562 grizzly feeders, two CJ613 jaw crushers, two CI225 impact crushers, two SC3062 circular vibrating screens and two SC3063 circular vibrating screens. With this plant installed and commissioned Sinoma (Anhui) Cement is now able to produce five aggregate products consisting of: 31.5-16mm, 16-10mm, 10-5mm, 5-3mm and 3-0mm.
As well as being able to provide accurately sized aggregates for the construction industry, Sinoma is also using the materials produced by the aggregate plants for its cement manufacturing. As the material for both aggregates and cement are being produced from the same quarry, the blasted rock is quite often of a large size, being around a 1m diameter. This necessitated the use of a primary jaw crusher that would be able to accept a large feed size, but at the same time be able to reduce the fed rock prior to being fed into a secondary crusher.
The CJ613 jaw crusher has proved to be well suited to the task as it is purpose-built for tough quarrying applications due to its heavy-duty design. Secondary crushing is then provided by the CI225 impact crushers, which have proved suitable for producing the next stage with the required shape. The CI225 has been developed for the secondary crushing of non-abrasive rocks in aggregate production.
Following on from the crushing process the material is then sent for screening to produce the finished fractions. This is carried out by two SC3062 and two SC3063 circular vibrating screens. Sandvik’s SC screens can be used on a variety of screening applications, but being of a more robust construction allow the feeding of a more coarse feed material size. Versatility is said to be ensured due to the choice of screening media.
Following screening and stockpiling the finished aggregates are then distributed across the area. This is accomplished due to efficient local waterway transport. This enables the material to be sent exactly where it is needed, being used on commercial concrete mixing plants in the major cities around Lake Chao and the lower-and-middle sections of the Yangtze River.
The firm’s extensive production of clinker cement is facilitated through three production lines each with a daily output of 4,500tonnes, and with a total annual production of 5.4 million tonnes. In addition over 5 million tonnes of aggregates, in a variety of sizes, are produced annually. The firm has its own specialised wharf located at Lake Chao, which handles 3.8 million tonnes/year of a variety of aggregates and other materials for shipping to the Yangtze River delta.
Aggregate production began at the firm’s quarry site in February 2012, with the company keen to see production ramped up to 5 million tonnes annually. This would involve producing a variety of sizes for use in both cement manufacturing, and for sale to the construction industry. The plan was to construct three aggregate production lines, with two being fully operational and the third being used depending on specific market conditions.
When Sinoma (Anhui) Cement set about ramping up its aggregate output the company set high standards, both for its own operations, and from the equipment it wished to use. The designated supplier of the aggregate plants would have to supply the plant, as well as aftermarket support, proactive servicing, and plant design. The supplier had to be able to deliver the production required, deliver low energy consumption and environmental protection, as well as operator training and efficient transportation and stockpiling.
Over the period of a year the company met with various manufacturers of aggregate plant, inspecting various facilities, and meeting with technical, service, aftermarket and planning experts. Following this extensive process the final contract for all elements of the new aggregate plants was awarded to Sandvik Construction in China. This resulted in an order being placed for Sandvik to supply all the equipment, plan the processes, and support the equipment for two aggregate production lines. This comprised of two SV1562 grizzly feeders, two CJ613 jaw crushers, two CI225 impact crushers, two SC3062 circular vibrating screens and two SC3063 circular vibrating screens. With this plant installed and commissioned Sinoma (Anhui) Cement is now able to produce five aggregate products consisting of: 31.5-16mm, 16-10mm, 10-5mm, 5-3mm and 3-0mm.
As well as being able to provide accurately sized aggregates for the construction industry, Sinoma is also using the materials produced by the aggregate plants for its cement manufacturing. As the material for both aggregates and cement are being produced from the same quarry, the blasted rock is quite often of a large size, being around a 1m diameter. This necessitated the use of a primary jaw crusher that would be able to accept a large feed size, but at the same time be able to reduce the fed rock prior to being fed into a secondary crusher.
The CJ613 jaw crusher has proved to be well suited to the task as it is purpose-built for tough quarrying applications due to its heavy-duty design. Secondary crushing is then provided by the CI225 impact crushers, which have proved suitable for producing the next stage with the required shape. The CI225 has been developed for the secondary crushing of non-abrasive rocks in aggregate production.
Following on from the crushing process the material is then sent for screening to produce the finished fractions. This is carried out by two SC3062 and two SC3063 circular vibrating screens. Sandvik’s SC screens can be used on a variety of screening applications, but being of a more robust construction allow the feeding of a more coarse feed material size. Versatility is said to be ensured due to the choice of screening media.
Following screening and stockpiling the finished aggregates are then distributed across the area. This is accomplished due to efficient local waterway transport. This enables the material to be sent exactly where it is needed, being used on commercial concrete mixing plants in the major cities around Lake Chao and the lower-and-middle sections of the Yangtze River.