A bespoke waste water drainage system saved time and money on a recent UK motorway scheme
Work on the London’s M25 motorway Junction 30/A13 Corridor Relieving Congestion Scheme is being undertaken by joint venture contractor Balfour Beatty/Skanska. The project is valued at nearly €91 million and completion is for autumn 2016.
There has been a successful continual programme of clean-up using road-sweeper/gulley cleaning trucks to remove detritus from the works areas.
Disposal of this type of waste w
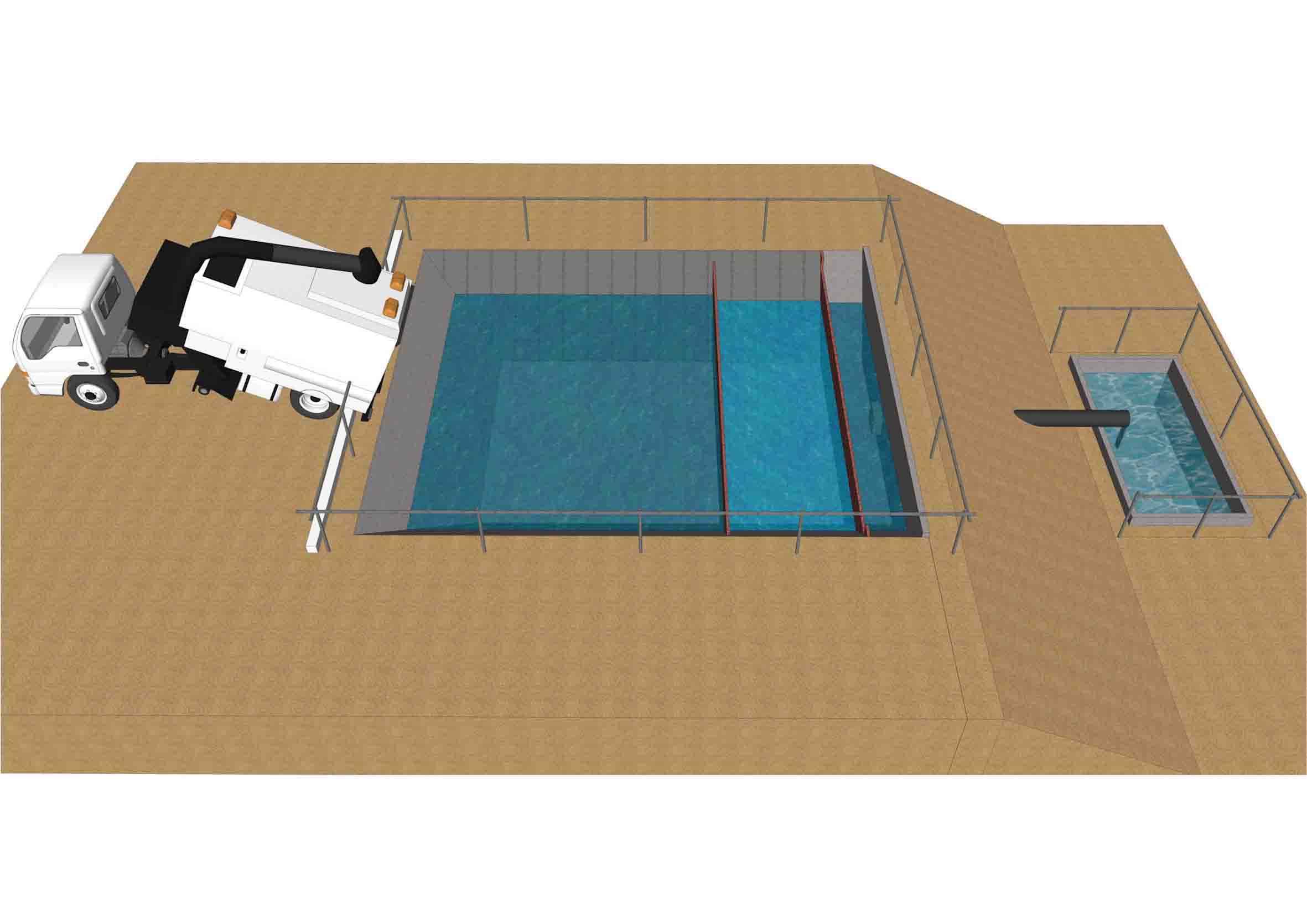
Schematic of the water treatment facility
A bespoke waste water drainage system saved time and money on a recent UK motorway scheme
Work on the London’s M25 motorway Junction 30/A13 Corridor Relieving Congestion Scheme is being undertaken by joint venture contractor1146 Balfour Beatty/2296 Skanska. The project is valued at nearly €91 million and completion is for autumn 2016.
There has been a successful continual programme of clean-up using road-sweeper/gulley cleaning trucks to remove detritus from the works areas.
Disposal of this type of waste would have involved costly road transportation in the trucks to a designated contaminated landfill site. On the M25 project, each lorry load would have had to travel a round trip of around 116km. As each load is treated as a separate cargo, each would also have required an Environment Agency (EA) regulatory position dewatering statement, at significant cost to the project.
To negate this, project managers and environmental advisors investigated alternatives, including one from Naylor Environmental that used its Smart Sponge and HydroBlox technology.
Smart Sponge offers a host of environmental, money saving uses in a variety of areas of water contamination. The standard Smart Sponge material is effective in absorbing and locking in polluting hydrocarbons and oil derivatives from surface water, while still allowing high flow-through rates. Smart Sponge can remove up to 95% of all oil contaminants present in storm water run-off or similar waste water flows and can, dependent on viscosity, absorb up to five times its own weight of hydrocarbons, thereby transforming the contaminant into a solid waste with lower disposal costs. This was the potential area of relevance to the project in hand. In addition to absorbing oil, the material can also treat pathogens as well as adsorb heavy metals.
The HydroBlox product - 100% manufactured from end-of-life recycled thermoplastics – provides a permanent solution for land drainage, ground stabilisation, green infrastructure and filtration. Naylor says that it does not clog, is easy to install and handle, requires little to no maintenance and is high strength and long lasting.
Naylor’s engineers created a system to handle, filter and provide reusable water on site instead of transporting the waste large distances.
The design of the M25 Junction 30 A13 CRCS Road Sweeper Water Treatment Facility was a surprisingly ‘low-tech’ solution given the amount of waste it was required to handle.
The facility comprised a concrete base ‘tank’ incorporating two separating walls which effectively created varying size settling tanks. Separating the various settling tanks were two porous walls built using the Naylor HydroBlox product in the form of HydroBlox planks.
The first wall allowed water offloaded from the road sweepers to pass through with solids of 5mm or less. Heavier solids settled in the holding tank under gravity before reaching the porous wall.
Flows through the first wall entered the second tank area which had a second HydroBlox wall as its lower outlet. This wall allowed flows through the porous barrier with particles of no more than 30microns. Flows then entered the third tank where these fines settled out.
Run-off from the final holding tank area was then taken off via a small-diameter pipe that led into an Ultra Urban Filter which contained the Naylor Smart Sponge element of the process. The hydrocarbon and heavy metal elements of the water flow were thereby removed before the water entered a final holding tank from which it could be recycled.
At the second HydroBlox wall, the facility handles significant throughput of up to 27 litres per second per m². System design can be modified to handle any input rate simply by changing the base tank size to be big enough to take the correct size HydroBlox walls.
According to necessary EA tests, the final water output was sufficiently clean for use in road sweeper activities during the works or for purposes such as site soaking, wash-down, dust suppression or for mixing with other products used during construction work. Testing of the solids showed they could also be disposed of more cost effectively as they did not require the EA regulatory position dewatering statement. A single statement covering the water treatment plant as a whole was locally approved by EA without a permit.
In April alone, around 28,000 litres of water were treated and reused – water which otherwise would have had to be sourced elsewhere. The on-site treatment plant provided considerable savings in diesel, time and waste disposal costs as the road sweepers undertook zero journeys to tip at an offsite waste facility. The facility offered savings in excess of €126,000 over one year.
The facility has a further environmental advantage. Once decommissioned, all concrete and masonry can be crushed and recycled for use in a new project. The HydroBlox plank sections, Smart Sponge and pipe can be reused on a similar site or project elsewhere.
Work on the London’s M25 motorway Junction 30/A13 Corridor Relieving Congestion Scheme is being undertaken by joint venture contractor
There has been a successful continual programme of clean-up using road-sweeper/gulley cleaning trucks to remove detritus from the works areas.
Disposal of this type of waste would have involved costly road transportation in the trucks to a designated contaminated landfill site. On the M25 project, each lorry load would have had to travel a round trip of around 116km. As each load is treated as a separate cargo, each would also have required an Environment Agency (EA) regulatory position dewatering statement, at significant cost to the project.
To negate this, project managers and environmental advisors investigated alternatives, including one from Naylor Environmental that used its Smart Sponge and HydroBlox technology.
Smart Sponge offers a host of environmental, money saving uses in a variety of areas of water contamination. The standard Smart Sponge material is effective in absorbing and locking in polluting hydrocarbons and oil derivatives from surface water, while still allowing high flow-through rates. Smart Sponge can remove up to 95% of all oil contaminants present in storm water run-off or similar waste water flows and can, dependent on viscosity, absorb up to five times its own weight of hydrocarbons, thereby transforming the contaminant into a solid waste with lower disposal costs. This was the potential area of relevance to the project in hand. In addition to absorbing oil, the material can also treat pathogens as well as adsorb heavy metals.
The HydroBlox product - 100% manufactured from end-of-life recycled thermoplastics – provides a permanent solution for land drainage, ground stabilisation, green infrastructure and filtration. Naylor says that it does not clog, is easy to install and handle, requires little to no maintenance and is high strength and long lasting.
Naylor’s engineers created a system to handle, filter and provide reusable water on site instead of transporting the waste large distances.
The design of the M25 Junction 30 A13 CRCS Road Sweeper Water Treatment Facility was a surprisingly ‘low-tech’ solution given the amount of waste it was required to handle.
The facility comprised a concrete base ‘tank’ incorporating two separating walls which effectively created varying size settling tanks. Separating the various settling tanks were two porous walls built using the Naylor HydroBlox product in the form of HydroBlox planks.
The first wall allowed water offloaded from the road sweepers to pass through with solids of 5mm or less. Heavier solids settled in the holding tank under gravity before reaching the porous wall.
Flows through the first wall entered the second tank area which had a second HydroBlox wall as its lower outlet. This wall allowed flows through the porous barrier with particles of no more than 30microns. Flows then entered the third tank where these fines settled out.
Run-off from the final holding tank area was then taken off via a small-diameter pipe that led into an Ultra Urban Filter which contained the Naylor Smart Sponge element of the process. The hydrocarbon and heavy metal elements of the water flow were thereby removed before the water entered a final holding tank from which it could be recycled.
At the second HydroBlox wall, the facility handles significant throughput of up to 27 litres per second per m². System design can be modified to handle any input rate simply by changing the base tank size to be big enough to take the correct size HydroBlox walls.
According to necessary EA tests, the final water output was sufficiently clean for use in road sweeper activities during the works or for purposes such as site soaking, wash-down, dust suppression or for mixing with other products used during construction work. Testing of the solids showed they could also be disposed of more cost effectively as they did not require the EA regulatory position dewatering statement. A single statement covering the water treatment plant as a whole was locally approved by EA without a permit.
In April alone, around 28,000 litres of water were treated and reused – water which otherwise would have had to be sourced elsewhere. The on-site treatment plant provided considerable savings in diesel, time and waste disposal costs as the road sweepers undertook zero journeys to tip at an offsite waste facility. The facility offered savings in excess of €126,000 over one year.
The facility has a further environmental advantage. Once decommissioned, all concrete and masonry can be crushed and recycled for use in a new project. The HydroBlox plank sections, Smart Sponge and pipe can be reused on a similar site or project elsewhere.