Ever tightening aggregate specifications for road surfacing materials is driving more quarries to wash their materials. Claire Symes looks at the technology and the implications for the industry Stricter aggregates specifications for both asphalt and concrete surfacing materials and the need to make the best use of all extracted material is driving greater use of washing equipment in the quarrying industry. But the latest washing and recycling technology means that this growth does not have to significantly
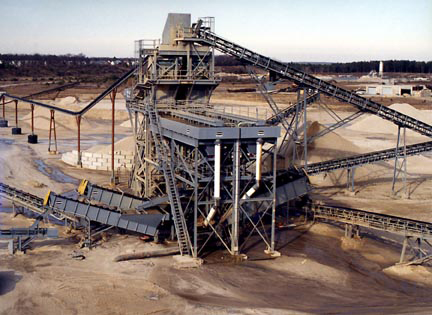
Ever tightening aggregate specifications for road surfacing materials is driving more quarries to wash their materials. Claire Symes looks at the technology and the implications for the industry
Stricter aggregates specifications for both asphalt and concrete surfacing materials and the need to make the best use of all extracted material is driving greater use of washing equipment in the quarrying industry. But the latest washing and recycling technology means that this growth does not have to significantly impact on energy or water consumption."Washing is enabling quarries to meet demand for sand, as well as improve the quality of other aggregate products. Many sand reserves are running out but modern washing techniques mean that dust can be treated to replace sand content," said Greystone vice president John Bennington. "Also as quarries progress, the more easily extracted is less available and quarries are having to process material with a higher level of clay and silt."
Finedoor commercial director Jim Blanchard has also witnessed the growth of the washing industry. "There is also greater need to wash hard rock material where previously it would have been considered waste," he said. "Now there is a general move to make better use of 6mm product that would have had a very low value before or been disposed of as waste.
"One customer in Aberdeen, Scotland had a large stockpile of dumped material that they needed to treat or would be charged to dispose of as waste. The site also used to import fine material for its coating plant but is now washing its waste material instead. More quarries are looking to specialise and make the best from both primary and secondary aggregates."
However, the decision on what equipment a quarry needs has to be considered in the context of both the feed material and the final product, as well as understanding the normal production volumes and realistic future targets. "There is no one size fits all when it comes to washing and quarries need to be careful they have the right advice and not just buy on price," explained Blanchard. "One thing that does help is that if borehole information is available, then the design can be based on future reserves rather than just on current production."
"What has changed over the last five to 10 years is the growth in water treatment," said Blanchard. "Dewatering screens have also become more popular as quarries have recognised that a drier product is more profitable and it also allows more water to be recycled."
Bennington added, "There is a big trend towards consideration of the environmental impact of quarrying and that includes reducing run off, which has driven wider use of dewatering screens. But there is also a focus on more energy efficient techniques, so some quarries now use a standard dewatering screw to discharge onto a dewatering screen to reduce the moisture content to 10% but returns any material that falls through the screen back onto the screw to remove the need for a cyclone. This uses 30 to 50% less energy."
The rise and rise of aggregate washing means that quarries are using more water, which in turn has driven wider use of water reclamation and recycling technology. "Demand for clean, high quality aggregates and the processing of more difficult material is driving increased washing, which in turn calls for more water and a greater need for water treatment," said Andrea Giglioli, area manager for water treatment specialist Fraccaroli and Balzan.
Water is a difficult issue for many quarries - either they are too remote to tap into the mains supply or, if they can, it is just too expensive. Add into this the need to treat before using it on site or returning it to the open environment, and quarry operations are facing a significant challenge.
It is for this reason that ever increasing numbers of quarries - both new and old - are turning to filter presses to treat waste water. This approach is gaining ground because it speeds up the rate of returning water to the washing cycle, but it also removes the need for settlement ponds.
"The demand for water treatment technology is partly being driven by legislation," said Giglioli. "In Italy all quarries are required to have water recycling facilities and it is just starting in Germany as well, but quarries all over the world are starting to invest ahead of legislation.
"Nonetheless, the main driver is the high cost of water - water treatment saves water and also gets around the problem of not being able to discharge wastewater directly into rivers these days.
"The growth of filter presses over settlement ponds is a result of a number of factors. Such ponds take up a lot of space on site, plus they can be costly to excavate when they become full, which can be twice a year for some larger quarries."
According to Giglioli, the basic concept of using a separating tank to remove the bulk of the solids and then a filter press to recover the remaining water from the sludge has not advanced significantly in recent years. "But what has changed is the flocculants that can be used to treat the water and enhance sediment removal," he said.
According to Fiorenzo Baietti, factory manager Technoidea Impianto which also builds bespoke water treatment systems, there is a wider range of flocculent types available that are also biodegradable. "There are now flocculents available to stabilise the PH of the water as well as accelerate the sediment removal," he said. "The technology to automate the addition of flocculants to take account of the actual volume of sediment has also improved, as has the automatic press washing that helps to ensure continuous performance."
Between 95 and 97% of water can be recovered through filter press treatment and the cycle time to return the water to the washing process can be less than an hour. "We carry out tests on materials from the quarry before designing a water treatment plant to ensure it can meet the on-site demand," said Baietti. "Some sites have sediment with a high clay content, so we design a system that adds lime to the sludge to speed up the filter press cycle time."
One quarry that is benefitting from hi-tech wastewater treatment is the Vitali Quarry in Caponago, It was established mainly as a processing site close to the motorway network, but quarry manager Giovanni Bonaiti said that while it was a strategically good location in terms of the market for aggregates, the access to water was limited.
The Vitali site has a Technoidea plant capable of processing 5,000m³ of water per day. Like many quarries, the site uses storage tanks for the wastewater and operates the settlement tanks and filter presses 24hours a day. "Electricity costs are lower at night and this approach also means the quarry does not require such a large plant," explained Baietti. "This is where the increase in automation has helped improve operation and GSM technology means that the plant can be remotely monitored."
Nonetheless, Vitali has installed the civil works ready for a second filter press to ensure it has the capability to cope with increased wastewater when demand for aggregates increases."
It is clear that advances in aggregate crushing to meet the need for high cubicity materials is being closely matched by developments in washing and water recycling technology.