Transport infrastructure is taken for granted in many, if not most, developed countries. This has resulted in a shortage of investment in maintenance, posing potential long term cost issues. In many developing nations transport networks are expanding fast, but insufficient thought is also being given to how these will be maintained.
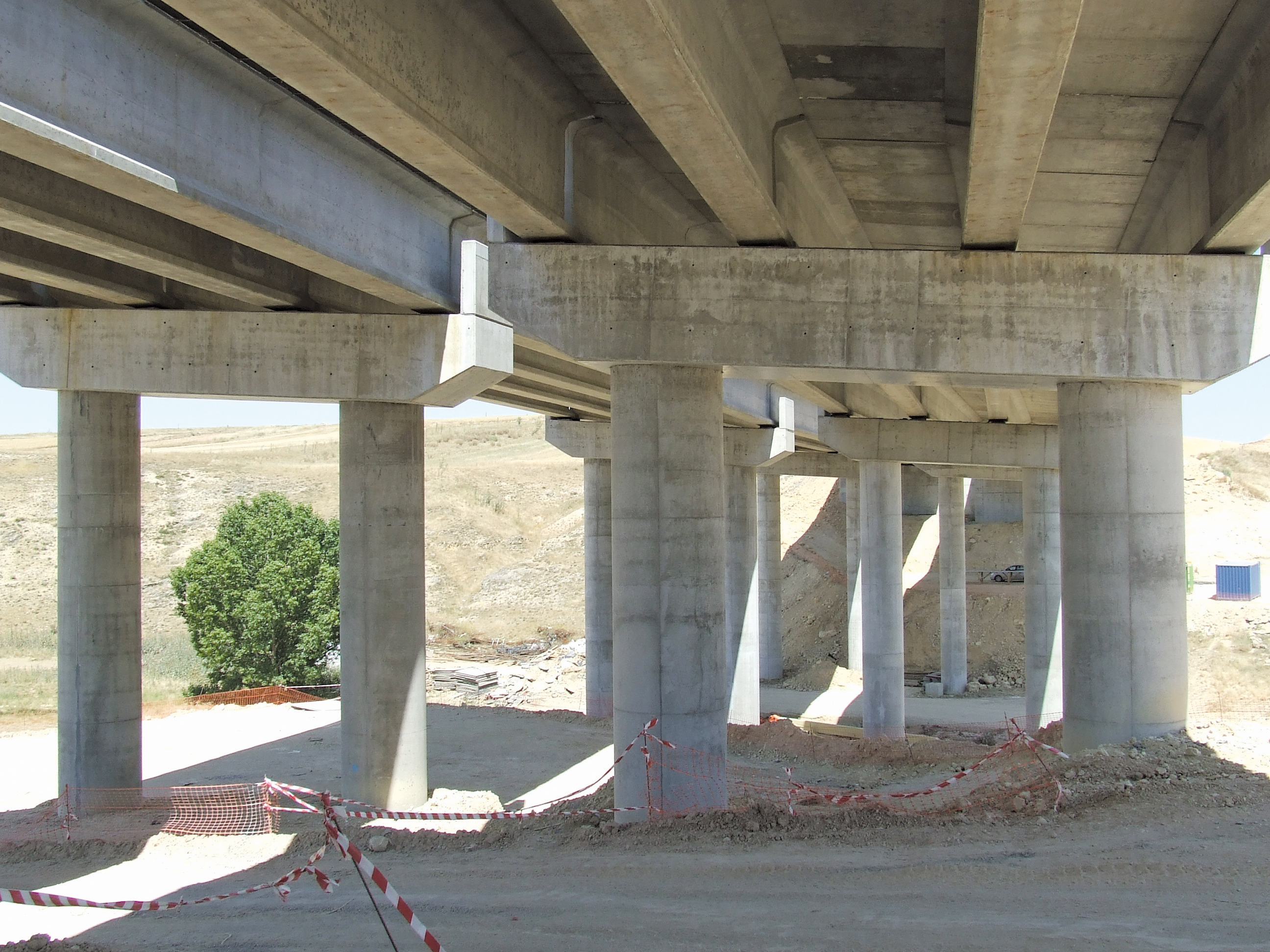
Pre-cast bridge design has to take account of issues such as protecting reinforcing elements from future corrosion
Earlier this year Fugro organised an event focussing on managing infrastructure assets - Mike Woof writes
Transport infrastructure is taken for granted in many, if not most, developed countries. This has resulted in a shortage of investment in maintenance, posing potential long term cost issues. In many developing nations transport networks are expanding fast, but insufficient thought is also being given to how these will be maintained.
6202 Fugro’s asset management event, held in Birmingham, focussed particularly on problems being seen in developed countries such as the UK and the US. However many of the same issues are also being seen in developing nations that are investing in infrastructure at present and these countries also need to develop long term maintenance strategies to protect their assets. An array of speakers presented on a range of key topics focussing on improving the efficiency of infrastructure management, taking note of problems such as shrinking budgets.
Pascal Laumet is director of product development, infrastructure asset management,3293 AgileAssets in the US. AgileAssets is a leading provider worldwide of solutions for integrated asset management solutions and the firm has a number of major contracts in the US. The company says that there is a need for better use of maintenance resources and Laumet said, “The networks are ageing and have to be managed safely.” He explained that better coordination of resources can be enormously beneficial and said, “What we’ve seen is a slow move to integration.”
But some asset owners are still proving sluggish in this regard and Laumet said, “Data mobility is a big question as well. These systems are in silos and they’re not talking to each other.”
He said that asset owners need to use the right tools for the job. “If you try to optimise your bridge programme, you can save more if you choose the right project. The higher you go, the more the potential for saving is significant.”
AgileAssets has several contracts with state departments of transport and one of its customers, Newark, optimised its limited budget using advice from the firm. He said, “They saved $9 million over a four-year period. They changed the way they did business.”
He added that the firm’s other clients have also revised their operations. “The whole idea was to fight the silo effects and do asset management as a whole. There is a big advantage to thinking strategically. “Better analytics matter and executives need to see the bigger picture. We can achieve further savings by coordinating projects.”
Alex Wright is group manager at the Transport Research Laboratory (777 TRL)’s technical division and he discussed the benefits of using light distance and ranging (LIDAR) technologies for gathering data. He said, “It can be used to measure a wide variety of assets.”
Wright explained that while traditionally, LIDAR has been an airborne technique using helicopters flying at low level at altitudes of 100-400m for scanning purposes, there are new technologies coming to market. The cost of using a helicopter has been a barrier to more widespread use of LIDAR systems in the past and Wright said, “The main thing is, they’re quite expensive and it isn’t commonly used due to the cost. But mounted on a vehicle, it’s cheaper and more versatile.”
He explained the new generation vehicle-mounted systems offer several benefits over aerial surveys and said, “You can survey under bridges and in tunnels, which you can’t do from the air.” He continued, “You can take LIDAR over the whole width of the road to get a 3D model and you need an inertial system to provide pitch and roll also. There are lots of applications such as the identification of signs and signals and overhead gantries and you can identify unsafe features.”
Accuracy can be an issue but he added, “You can get increases in accuracy if you use post-processing, base stations or use reference points.” Wright explained that when work had to be carried out on the UK’s busy M25 motorway, it was necessary to measure the distance from the white lines to the barrier so as to determine how much space was available for traffic management purposes. Wright noted that that LIDAR technology proved valuable in this application and said, “We reckoned it was accurate to a few centimetres.”
Jørgen Krarup is senior engineer at2283 Greenwood Engineering TSD, a firm that specialises in deflectomer technology and which has considerable potential for assessing road condition. The firm has developed its traffic speed deflectometer (TSD) system over a number of years and this can be used for mechanistic pavement analysis and is able to assess horizontal stresses and vertical deflection in a surface asphalt layer. This rolling wheel deflectometer can be used to determine the loads the asphalt will take before it cracks, highlighting areas that will require repair and allowing maintenance work to be carried out before failures occur, and cutting costs. Krarup said that a patented Doppler laser sensor system measures the velocity of deflection rather than the displacement. This allows the displacement to be calculated accurately and he commented, “At 2m loadings you can see 2mm deflection on a highway in California.”
According to Krarup, this system is more efficient and also more versatile than rival technologies that can only measure at lower speeds as it can record data at speeds of up to 80km/h. The system has been well-proven and recorded data on 18,000km of roads in Australia over a 5-month period for example. The units have been supplied to the UK, Denmark, Italy, Poland, South Africa, China and the US.
As the TSD measures the vertical pavement velocity at each Doppler laser position, it is the dynamic response to the authentic design axle load that is recorded according to Krarup. And he explained that instead of trying to simulate the load pulse from a truck, it is the axle load of rolling wheel that generates the deflection velocities. He explained that as most pavement works are focused on pavement preservation, the benefit from the data this equipment recovers will be enormous as it can provide the exact location of sections where damage will develop fastest.
Rod Eddies is regional service line manager geophysics at Fugro and he explained that managing ground risks is of key importance, particularly in the UK due to decades, and in some instances centuries, of industrial activity. He said, “This little island is peppered with former mines and quarries, which means it is not conducive to a good road surface structure.”
Eddies said that this cultural legacy leaves a great Deal of uncertainty as there is a lack of sub-surface information, “We need to reduce uncertainty in geophysics as a rule. By understanding how the ground varies we can understand the physics. Geology can be particularly unkind to our road surfaces.”
To address maintenance issues, the company has developed surface wave seismic technology, which Eddies says offers high accuracy. He said, “Geotechnics has come a long way. Now in 3D we can map ground stiffness.” And Eddies said that the systems are improving also, “There will be a continuation in the development of GPR technologies.”
Bridge condition poses major concern for transport infrastructure in many countries and there are many older structures that are not performing well or which may be reaching the end of their design life. Dr John Broomfield is international corrosion specialist at Broomfield Consultants and he said, “We have ageing bridges and we have to live with them.”
Broomfield used the condition of reinforced concrete bridges as a Case study for the built highway environment. He explained that in the UK, road bridges are traditionally designed for a 100-year working life and that many (if not most) of the 3,200 or so structures the Highways Agency is responsible for are well into their middle age, meaning that maintenance is a key issue. He said, “One of the problems is that bridges won’t be replaced so we’ve got to repair them so they’ll last indefinitely.”
If anything, the situation may be even worse in the US as Dr Broomfield commented that US bridges constructed in the 1960s were designed to have a 50-year life. The widespread use of reinforced concrete bridges is a problem and Dr Broomfield said that many older structures were built to lower standards. Meanwhile maintenance has also proved an issue and he commented, “It took a while for the message on de-icing salts to sink in.”
When steel reinforced concrete bridges started being constructed there was not a great Deal of knowledge as to corrosion reactions that can take place. Corrosion can occur at a distance from contact with oxygen, while patching type maintenance can cause its own issues and Dr Broomfield said, “Simple repairs can accelerate the problem.”
Corrosion protection techniques vary and Broomfield said, “In the US they don’t tend to use waterproof membranes,” adding that epoxy coated rebar tends to be used instead. In other markets cathodic protection is preferred, although not in the Middle East as conditions can be aggressive chemically.
The presence of chloride is a challenge for bridge maintenance teams although Dr Broomfield said that corrosion thresholds can vary. “It can take five years before corrosion starts occurring after chlorides attack.”
Providing access for maintenance is important and Dr Broomfield commented, “When we train civil engineers we don’t teach them enough about materials degradation or access. New bridges need to be more durable and engineers need to be trained to understand the problems.”
John Munslow works for South Gloucestershire County Council and he explained that climate change is having a noticeable effect on transport infrastructure. The county’s records show that extreme weather conditions are now having a noticeable effect on road condition and much more so than just 15-20 years ago. Small changes in weather conditions over time will have big cost implications for transport infrastructure in the long term according to Munslow. To determine how the county would Plan its budgets more effectively, Munslow approached the UK’s Meteorological Office for help in using climate models. There are numerous factors to be considered including temperatures, precipitation, wind, humidity and the rising sea level and he said, “By using a risk matrix we could see which assets were going to be affected first and we identified what our biggest priorities were.”
Munslow said that temperature increases are playing a notable role in wear and tear on roads. With temperatures topping 30°C on several consecutive days and night-time temperatures not falling below 15°C, this does not allow sufficient time for surfaces to cool and asphalt roads can be vulnerable to deformation as a result. Minor roads could end up having the biggest repair costs as maintenance often tends to be minimal, unlike busier routes.
Looking ahead to the 2020s, the 2050s and the 2080s, Munslow asked some key questions, “Is our drainage going to cope? Do we need more gritters?”
Smart CCTV for road maintenance
High-speed video cameras from2546 Sony Image Sensing Solutions are now being used by system integrator Horus as part of a pothole identification system. The package is said to be capable of detecting potholes at speeds of up to 130km/h. By attaching the cameras system to vehicles, the system cuts the time, cost and danger of finding potholes. This speeds detection, allowing councils to make earlier, less costly repairs and cut damage to vehicles using the roads.
The cost of repairing potholes and the resultant damage to vehicles is estimated to be many billions of euros each year for European governments and drivers. In several European countries, courts are forcing local authorities to compensate drivers for this damage. A 2013 survey by UK roadside recovery organisation, the AA, suggests a third of vehicles in Britain had suffered pot hole related damage in the last two years.
The vision based pothole detection system integrates six high-speed Sony ITS camera modules, each taking 15 high-resolution frames/second. The resulting 360° imaging system accurately records data from up to 3 lanes simultaneously, even when travelling at high speed. Images are combined with GPS data and processed by an on-board CPU.
Video from the system can then be transferred to council computers and analysed in the office using a bespoke media player with integrated mapping functionality. Previously, detecting damage was labour intensive, requiring information from the public and certified specialists slowly travelling the length of the network. This also often required lane or road closures.
Government authorities in Holland as well as contractors such as BAM, BallastNedam, and Heijmans have already implemented the system. By adopting such a system the councils are able to more easily prioritise repairs to ensure potholes that would cause accidents or damage to cars are filled first. It also removes subjectivity from the prioritisation process, ensuring the most urgent repairs move to the top of the list.
Pothole patching system
Road repair specialist Nuphalt says that its pothole patching system can offer a long term solution. The system uses a portable thermal heater that is positioned over the affected area, with an 8-minute pulsed heat cycle allowing energy from the highly efficient NIT heater to penetrate the wearing course. This provides a workable material but without carbonising or damaging it in the process.
Road repair teams can then scarify an area 50mm in from the repair edge. This ensures integrity of the heated thermal joint between the new and existing material according to Nuphalt. This delivers a strong and seamless joint. No material is taken from the repair area however and everything is recycled in-situ, resulting in no waste or landfill.
To check temperatures, an infrared thermometer is used. The firm says that the material temperature should be between 70°-100°C to provide the best compaction conditions. High grade enriched emulsion is added to the repair area. This is evenly mixed through the recycled material to deliver a consistent and even exposure. The material is said to recoat the recycled aggregate, increasing bitumen content to near new levels.
The compaction equipment is then specified in line with the requirements of the area to be repaired. All edges are rolled first to create a mechanical interlock with the surrounding surface. The finished surface is said to provide a long lasting result and that also complies with safety requirements such as skid resistance.
Transport infrastructure is taken for granted in many, if not most, developed countries. This has resulted in a shortage of investment in maintenance, posing potential long term cost issues. In many developing nations transport networks are expanding fast, but insufficient thought is also being given to how these will be maintained.
Pascal Laumet is director of product development, infrastructure asset management,
But some asset owners are still proving sluggish in this regard and Laumet said, “Data mobility is a big question as well. These systems are in silos and they’re not talking to each other.”
He said that asset owners need to use the right tools for the job. “If you try to optimise your bridge programme, you can save more if you choose the right project. The higher you go, the more the potential for saving is significant.”
AgileAssets has several contracts with state departments of transport and one of its customers, Newark, optimised its limited budget using advice from the firm. He said, “They saved $9 million over a four-year period. They changed the way they did business.”
He added that the firm’s other clients have also revised their operations. “The whole idea was to fight the silo effects and do asset management as a whole. There is a big advantage to thinking strategically. “Better analytics matter and executives need to see the bigger picture. We can achieve further savings by coordinating projects.”
Alex Wright is group manager at the Transport Research Laboratory (
Wright explained that while traditionally, LIDAR has been an airborne technique using helicopters flying at low level at altitudes of 100-400m for scanning purposes, there are new technologies coming to market. The cost of using a helicopter has been a barrier to more widespread use of LIDAR systems in the past and Wright said, “The main thing is, they’re quite expensive and it isn’t commonly used due to the cost. But mounted on a vehicle, it’s cheaper and more versatile.”
He explained the new generation vehicle-mounted systems offer several benefits over aerial surveys and said, “You can survey under bridges and in tunnels, which you can’t do from the air.” He continued, “You can take LIDAR over the whole width of the road to get a 3D model and you need an inertial system to provide pitch and roll also. There are lots of applications such as the identification of signs and signals and overhead gantries and you can identify unsafe features.”
Accuracy can be an issue but he added, “You can get increases in accuracy if you use post-processing, base stations or use reference points.” Wright explained that when work had to be carried out on the UK’s busy M25 motorway, it was necessary to measure the distance from the white lines to the barrier so as to determine how much space was available for traffic management purposes. Wright noted that that LIDAR technology proved valuable in this application and said, “We reckoned it was accurate to a few centimetres.”
Jørgen Krarup is senior engineer at
According to Krarup, this system is more efficient and also more versatile than rival technologies that can only measure at lower speeds as it can record data at speeds of up to 80km/h. The system has been well-proven and recorded data on 18,000km of roads in Australia over a 5-month period for example. The units have been supplied to the UK, Denmark, Italy, Poland, South Africa, China and the US.
As the TSD measures the vertical pavement velocity at each Doppler laser position, it is the dynamic response to the authentic design axle load that is recorded according to Krarup. And he explained that instead of trying to simulate the load pulse from a truck, it is the axle load of rolling wheel that generates the deflection velocities. He explained that as most pavement works are focused on pavement preservation, the benefit from the data this equipment recovers will be enormous as it can provide the exact location of sections where damage will develop fastest.
Rod Eddies is regional service line manager geophysics at Fugro and he explained that managing ground risks is of key importance, particularly in the UK due to decades, and in some instances centuries, of industrial activity. He said, “This little island is peppered with former mines and quarries, which means it is not conducive to a good road surface structure.”
Eddies said that this cultural legacy leaves a great Deal of uncertainty as there is a lack of sub-surface information, “We need to reduce uncertainty in geophysics as a rule. By understanding how the ground varies we can understand the physics. Geology can be particularly unkind to our road surfaces.”
To address maintenance issues, the company has developed surface wave seismic technology, which Eddies says offers high accuracy. He said, “Geotechnics has come a long way. Now in 3D we can map ground stiffness.” And Eddies said that the systems are improving also, “There will be a continuation in the development of GPR technologies.”
Bridge condition poses major concern for transport infrastructure in many countries and there are many older structures that are not performing well or which may be reaching the end of their design life. Dr John Broomfield is international corrosion specialist at Broomfield Consultants and he said, “We have ageing bridges and we have to live with them.”
Broomfield used the condition of reinforced concrete bridges as a Case study for the built highway environment. He explained that in the UK, road bridges are traditionally designed for a 100-year working life and that many (if not most) of the 3,200 or so structures the Highways Agency is responsible for are well into their middle age, meaning that maintenance is a key issue. He said, “One of the problems is that bridges won’t be replaced so we’ve got to repair them so they’ll last indefinitely.”
If anything, the situation may be even worse in the US as Dr Broomfield commented that US bridges constructed in the 1960s were designed to have a 50-year life. The widespread use of reinforced concrete bridges is a problem and Dr Broomfield said that many older structures were built to lower standards. Meanwhile maintenance has also proved an issue and he commented, “It took a while for the message on de-icing salts to sink in.”
When steel reinforced concrete bridges started being constructed there was not a great Deal of knowledge as to corrosion reactions that can take place. Corrosion can occur at a distance from contact with oxygen, while patching type maintenance can cause its own issues and Dr Broomfield said, “Simple repairs can accelerate the problem.”
Corrosion protection techniques vary and Broomfield said, “In the US they don’t tend to use waterproof membranes,” adding that epoxy coated rebar tends to be used instead. In other markets cathodic protection is preferred, although not in the Middle East as conditions can be aggressive chemically.
The presence of chloride is a challenge for bridge maintenance teams although Dr Broomfield said that corrosion thresholds can vary. “It can take five years before corrosion starts occurring after chlorides attack.”
Providing access for maintenance is important and Dr Broomfield commented, “When we train civil engineers we don’t teach them enough about materials degradation or access. New bridges need to be more durable and engineers need to be trained to understand the problems.”
John Munslow works for South Gloucestershire County Council and he explained that climate change is having a noticeable effect on transport infrastructure. The county’s records show that extreme weather conditions are now having a noticeable effect on road condition and much more so than just 15-20 years ago. Small changes in weather conditions over time will have big cost implications for transport infrastructure in the long term according to Munslow. To determine how the county would Plan its budgets more effectively, Munslow approached the UK’s Meteorological Office for help in using climate models. There are numerous factors to be considered including temperatures, precipitation, wind, humidity and the rising sea level and he said, “By using a risk matrix we could see which assets were going to be affected first and we identified what our biggest priorities were.”
Munslow said that temperature increases are playing a notable role in wear and tear on roads. With temperatures topping 30°C on several consecutive days and night-time temperatures not falling below 15°C, this does not allow sufficient time for surfaces to cool and asphalt roads can be vulnerable to deformation as a result. Minor roads could end up having the biggest repair costs as maintenance often tends to be minimal, unlike busier routes.
Looking ahead to the 2020s, the 2050s and the 2080s, Munslow asked some key questions, “Is our drainage going to cope? Do we need more gritters?”
Smart CCTV for road maintenance
High-speed video cameras from
The cost of repairing potholes and the resultant damage to vehicles is estimated to be many billions of euros each year for European governments and drivers. In several European countries, courts are forcing local authorities to compensate drivers for this damage. A 2013 survey by UK roadside recovery organisation, the AA, suggests a third of vehicles in Britain had suffered pot hole related damage in the last two years.
The vision based pothole detection system integrates six high-speed Sony ITS camera modules, each taking 15 high-resolution frames/second. The resulting 360° imaging system accurately records data from up to 3 lanes simultaneously, even when travelling at high speed. Images are combined with GPS data and processed by an on-board CPU.
Video from the system can then be transferred to council computers and analysed in the office using a bespoke media player with integrated mapping functionality. Previously, detecting damage was labour intensive, requiring information from the public and certified specialists slowly travelling the length of the network. This also often required lane or road closures.
Government authorities in Holland as well as contractors such as BAM, BallastNedam, and Heijmans have already implemented the system. By adopting such a system the councils are able to more easily prioritise repairs to ensure potholes that would cause accidents or damage to cars are filled first. It also removes subjectivity from the prioritisation process, ensuring the most urgent repairs move to the top of the list.
Pothole patching system
Road repair specialist Nuphalt says that its pothole patching system can offer a long term solution. The system uses a portable thermal heater that is positioned over the affected area, with an 8-minute pulsed heat cycle allowing energy from the highly efficient NIT heater to penetrate the wearing course. This provides a workable material but without carbonising or damaging it in the process.
Road repair teams can then scarify an area 50mm in from the repair edge. This ensures integrity of the heated thermal joint between the new and existing material according to Nuphalt. This delivers a strong and seamless joint. No material is taken from the repair area however and everything is recycled in-situ, resulting in no waste or landfill.
To check temperatures, an infrared thermometer is used. The firm says that the material temperature should be between 70°-100°C to provide the best compaction conditions. High grade enriched emulsion is added to the repair area. This is evenly mixed through the recycled material to deliver a consistent and even exposure. The material is said to recoat the recycled aggregate, increasing bitumen content to near new levels.
The compaction equipment is then specified in line with the requirements of the area to be repaired. All edges are rolled first to create a mechanical interlock with the surrounding surface. The finished surface is said to provide a long lasting result and that also complies with safety requirements such as skid resistance.