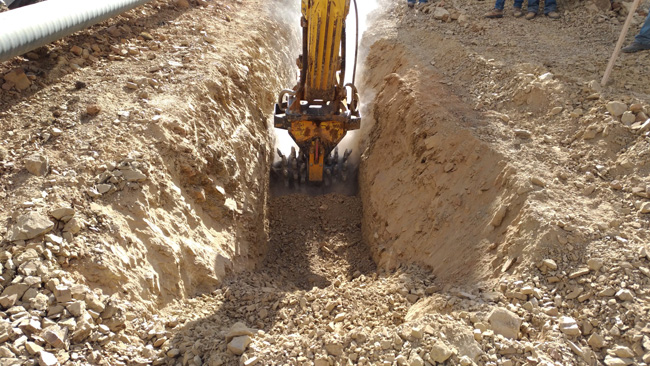
The city of Potosi in Bolivia is benefiting from improved infrastructure, following the use of equipment from
Cutter units from MB Crusher have been used to dig in difficult conditions so as to excavate a channel for a new gas pipeline.
Located at 4,090m above sea level, Potosi has suffered from major issues with regard to utilities. Gas supplies for example have been restricted, with users typically having to rely on bottled gas. Given that the city is central to Bolivia’s silver mining industry, this restriction has also held back Bolivia’s economy as a whole
However, the MB Crusher unit has been involved in an important project for the city, the construction of the Sucre-Potosì Gas pipeline.The work has been carried out in remote areas at more than 4,000m above sea level, in a terrain that is not completely served by roads.
The 57km gas pipeline between Mariaca and Karachipampa will meet Potosì's increasing demand for natural gas and will allow the expansion of commercial and industrial activities in the area. The MB Crusher Drum Cutter was used with a
In a rarefied zone with extreme conditions and hard rock, the work was arduous. However despite the difficult conditions, the MB-R800 unit selected for the work proved both reliable and productive. An important feature in this job was the unit’s integrated security system. This is designed to intervene if the excavator's parameters are not properly regulated. In cases where materials with different levels of hardness are being excavated, the MB units can adjust themselves. This reduces wear and tear while also optimising productivity. It also reduces stress on the excavator arm and increases stability during processing. To ease efficiency, the two drums can be dismantled directly on site and units have a patented direct, twin motor drive that is said to distribute forces generated by the two milling heads more efficiently. In addition, the contractor used other units from MB Crusher, including a BF80.3 crusher bucket. This unit had the task of crushing the material excavated by the cutter and reducing it in size so that it could be re-used as fill to cover the pipes.