Compact compaction units are delivering increased performance – Mike Woof reports. Competition is tough in the market for non-ride-on compaction units, with two manufacturers now introducing revamped models. Both JCB and Wacker Neuson aim to claim a larger section of the market with their latest designs, compaction plates and remote-controlled trench rollers respectively.
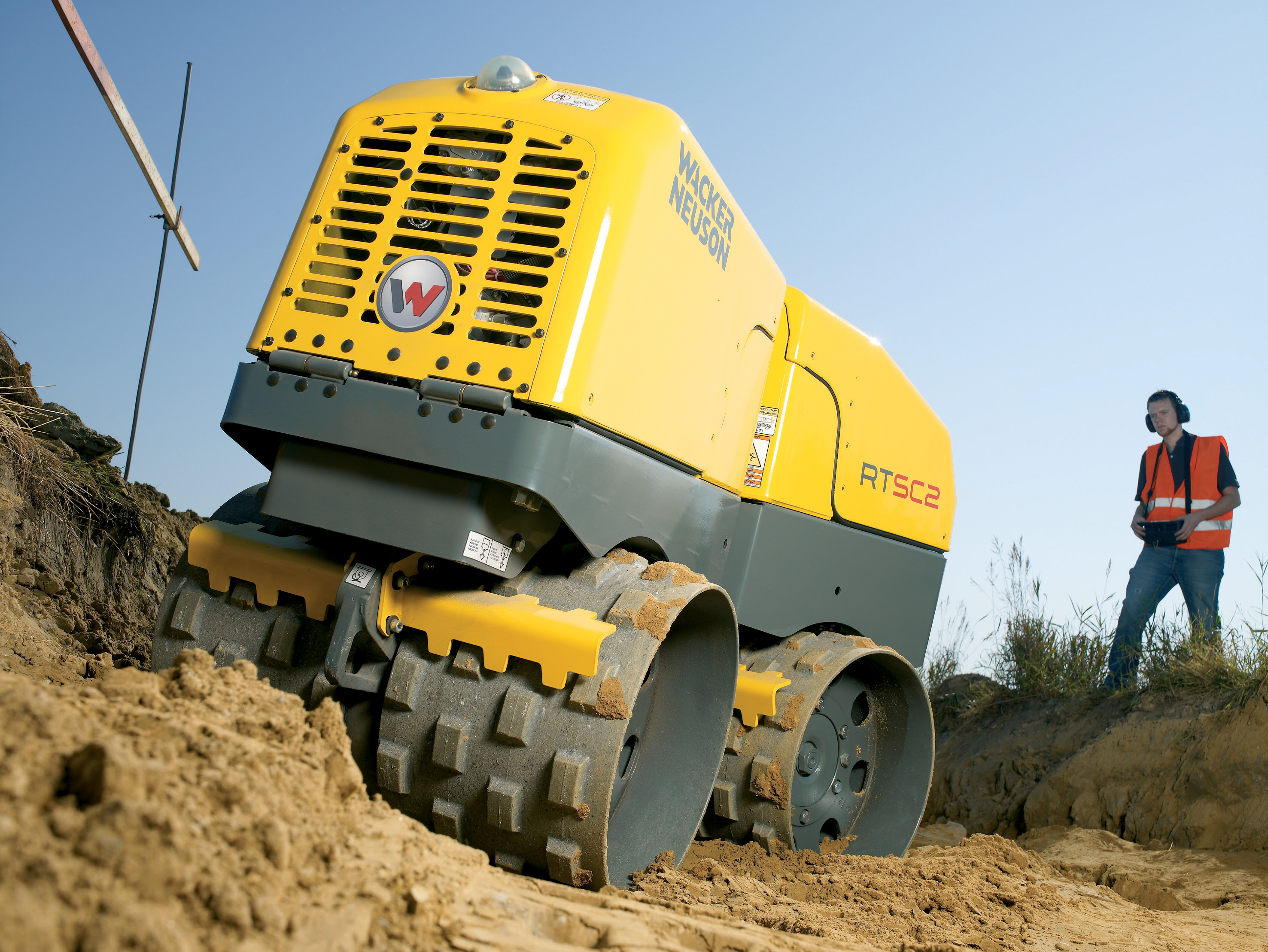
The new remote-controlled compactors from Wacker Neuson are said to offer low running costs, high performance and long working life
Compact compaction units are delivering increased performance – Mike Woof reports
Competition is tough in the market for non-ride-on compaction units, with two manufacturers now introducing revamped models. BothJCB says that its new compaction plates are designed to reduce hand arm vibration levels while delivering high performance. There are three new models, the FP1030, FP1540 and FP1550, and these feature plate widths of 300mm, 400mm and 500mm respectively. The FP1030 delivers a compaction force of 10kN while the FP1540 and FP1550 both deliver 15kN. These units can be used to compact materials such as hard-core and soil, as well as for asphalt work when fitted with the optional water kit. The water kit comes with a sprinkler bar located close to the base plate to optimise coverage. Meanwhile a specialist paving kit allows the compaction plates to be used on non-cohesive materials such as stone paving.
According to JCB, key features include the patent-pending handle design, which is said to ensure that hand/arm vibration levels are amongst the lowest in the industry. This is important as it allows for up to 15 hours operation on the largest model. In addition to the handle features, the folding design means that the plates can be fitted into small vans for easy transport from site to site.
The plates are powered by
From Wacker Neuson come improved rollers with maintenance-free lower body designs. The new RT56SC-2 and RT82SC-2 models are equipped with permanent lubrication, which is said to boost operating times and reduce running costs. The lower maintenance needs have been achieved as the drive gear is located in the lower body while the gearbox and ball bearings in the vibration-generating exciter now have high-quality permanent lubrication. This eliminates two maintenance steps that used to be necessary over the lifetime of the roller. Servicing of the RT56SC-2 and RT82SC-2 rollers is limited to one annual hydraulic oil change and replacement of the hydraulic return filter.
Oliver Kolmar, product manager for soil and asphalt compaction, said, "If they schedule their annual maintenance during the winter months, operators are able to count on this roller throughout the entire construction season."
An additional improvement is provided by the more robust housing fitted to the exciter motor, which further increases durability and reliability, even in continuous operation on tough sites. The remote control system boosts safety and for compaction in trenches, it allows an operator to be positioned off the trench, allowing the roller to work right close to the edge even in tight spots. Further protection for the operator and construction site workers is provided by the infrared data transmission. Should the line of sight between the roller and the remote control be obstructed, the roller stops. The unit also switches itself off if the machine is too far away or if the proximity recognition sensor detects that the distance between the roller and the operator is insufficient.
The units are designed for use in an array of applications, including compacting the lower sub-base of foundations, roads and parking lots, as well as excavations for utility connection for example. The sheeps-foot drums and high vibration speed allow the units to compact cohesive soils, while low centres of gravity and twist-proof articulated joints prevent them from tipping over on steep inclines. Good manoeuvrability is claimed, allowing the machines to work around manhole covers.