The mini and midi excavator sector continues to squeeze more out of less, with some innovative engineering solutions being applied to zero- and short-tailswing models - Geoff Ashcroft investigates. It is a vicious circle - customers seek smaller, tighter, ever more compact excavators, leaving manufacturers with the challenges of squeezing greater levels of technology into what is all too often an even smaller machine.
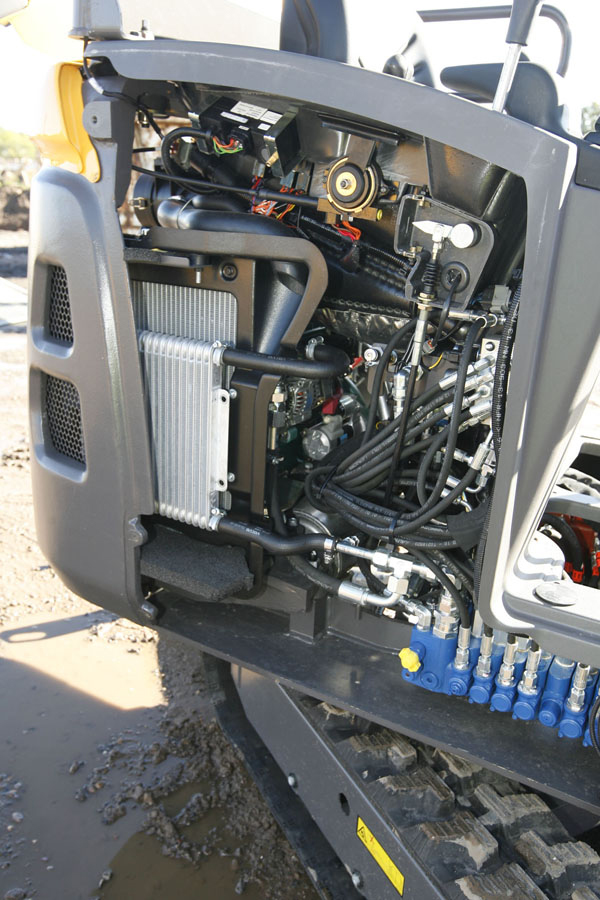
Good access for maintenance is a key feature of the latest Volvo mini excavator
The mini and midi excavator sector continues to squeeze more out of less, with some innovative engineering solutions being applied to zero- and short-tailswing models - Geoff Ashcroft investigates
It is a vicious circle - customers seek smaller, tighter, ever more compact excavators, leaving manufacturers with the challenges of squeezing greater levels of technology into what is all too often an even smaller machine.While keeping overall dimensions neat and compact, the engine, its cooling pack and all ancillaries along with a hydraulic system, pump, valve block and slew motor, all need to be installed in way that avoids the need for a major strip-down just to change a filter.
And with smaller swing radii, lower noise levels and easier maintenance at the top of the agenda, just how are manufacturers achieving these goals?
New Holland says that on its larger models, external noise levels have dropped by up to 10dB(A) as a consequence of introducing INDR, delivering an ultra quiet machine.
The system uses an additional pre-screen filter, which removes large dust particles from air flowing into the engine compartment, and it also goes some way to containing noise within the engine bay. Noise emissions are directed upwards as air exits the body on the offside of the machine, away from making a direct 'hit' on those standing near the machine.
It is a design that makes it difficult for noise to simply filter out of the machine in any direction. The result is an excavator that can be comfortably worked in urban environments, says the firm, without excessive noise intrusion to nearby residents.
New Holland Construction suggests that further developments in the mini excavator sector are being driven by customer demand for Object Handling Kits. These will include boom and arm safety check valves, a lifting hook and the installation of a safe load indicator.
"The ZTS configuration of the Bobcat E26 resulted in several packaging issues that required innovative engineering solutions," said Tom Raes, business unit director, mini excavators for Doosan Infracore Construction Equipment.
"The E26's cooling system was optimised to allow for machine operation in ambient temperatures up to 38°C and the cover and cooling system layout has been designed to allow tool-less radiator clean out," he added.
Mr Raes pointed out that the Bobcat E26 also benefits from a cab shared with larger Bobcat models while still maintaining the ZTS configuration. "This machine's final design allowed for adequate engine airflow while reducing external and in-cab noise levels."
The KX015-4, KX016-4 and KX018-4 replace the KX36-3, KX41-3s and KX41-3v, though the new models still use many proven components from the Dash 3 range.
Model numbers now closely mirror operating weights too.
To gain access to the cooling pack, Kubota has designed an opening door on the lefthand rear corner. The battery is in there too, relocated from beneath the seat on previous versions.
Cleverly, Kubota has introduced a fuel filler neck extender - this is not essential, but is indicative of the attention to detail the Japanese firm has put into giving customers the right kit for the job. With the fuel tank lid removed, the extender simply twists onto the tank neck and makes the task of refueling from a 25litre drum a much simpler task. There is less risk of spilling diesel down the side of the machine, too, and it creates a neat solution to an age-old problem - finding enough space to successfully package all the components in the upper structure.
There is also a push button by the fuel filler, and for those instances where you simply cannot see the fuel gauge, pushing the button activates an audible beep that indicates how the tank is filling. Beeps get closer together as the tank nears full, eventually becoming one long continuous tone to warn that the tank is full enough.
The 300.9D and 301.4C with operating weights of 935kg and 1,390kg respectively, give Cat a micro machine for those who demand ultra-compact dimensions and a true 1.5tonner for the rental sector.
While the 300.9D remains largely unchanged from its Wacker Neuson specification, the 301.4C has been given new joystick pods which both fold upwards to allow entry and exit from both sides of the machine.
There is a new floor mat and the introduction of interlocks to prevent accidental operation of the pedals when the control pods are raised.
Hydraulically, the 301.4C is a departure from Cat's usual format - where its own mini excavators have previously favoured variable displacement hydraulic pumps, the new 1.5 tonner uses a Rexroth flow sharing valve with a gear pump hydraulic system.
For Swedish maker
All four models are identical, save for aspects of the EC20C which gets a longer, four-roller undercarriage and 250mm wide tracks compared to the three lighter machines' 230mm, three-roller track frame. All models share a diesel tank design that uses a large removable bung in the base of the tank to simplify cleaning out.
Effort applied at the design stages has ensured the C-series minis are something of a revelation when it comes to service access and component location.
Lifting the engine cover at the rear provides easy and wide-open access to the engine compartment. Here, the moulded plastic diesel tank wraps snugly inside the cast counterweight, with a large filler to simplify refuelling. Above it sits the hydraulic oil tank, with a clear glass debris trap for the hydraulic system that is also within easy reach.
On the left-hand side, a removable panel - secured by three bolts - gives access to electrical relays, fuses and the battery.
Removing five bolts from the right-hand side panel allows the C-series to be opened up like Pandora's box, as the entire covering is effortlessly removed to give access to the cooling pack, valve block and hydraulic hoses.
Furthermore, it is easier to reach the starter motor and alternator.
Even the exhaust system is accessible, should the traits of three-cylinder engine vibration cause premature cracking of the silencer and its pipe, leading to early repair or replacement.
Hanix has recently gone from B to D series for its 1.5tonners marking the introduction of Kubota engines, while
Yanmar has recently launched its ViO33U model, weighing 3,270kgs. Replacing the ViO30, this fourth generation of ViO machine offers a larger cab than its predecessor and a straighter boom profile - the latter is said to improve truck loading characteristics and material retention when using the boom and arm for maximum lift height.