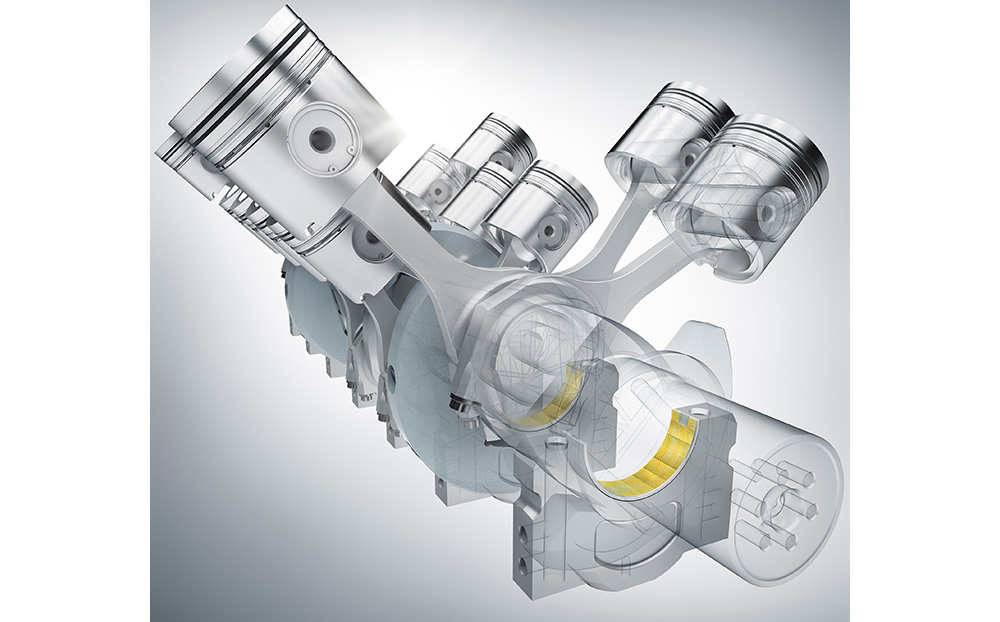
Rolls-Royce and cellcentric, a joint venture company set up by Daimler Truck and Volvo Group have a strategic cooperation for the deployment of cellcentric hydrogen fuel cell modules. Rolls-Royce, through its Power Systems business unit, is to develop complete mtu hydrogen fuel cell solutions based on cellcentric’s fuel cell modules. The hydrogen-based, CO2 free power generation fuel cell prototypes are already on the test stand, with pilot installations planned for 2023.
Both Rolls-Royce and cellcentric are convinced that the technology and time are right for launching commercial fuel cell applications for the mass market. Each fuel cell module will in the future deliver a net power output of around 150kW. These can be connected together into scalable fuel cell power plants with outputs in the megawatt range, capable of providing clean power.
Rolls-Royce commissioned a fuel cell demonstrator earlier this year and plans to bring a further demonstrator plant online in 2022, based on modules providing approximately 100kW each. The first pilot plants with customers will be installed in 2023, with Rolls-Royce launching standard production fuel cell systems in 2025.
Partnership with cellcentric offers Rolls-Royce the opportunity of using fuel cell modules produced by a leading supplier with long-standing experience. Its quick deployment of a large volume of fuel cells has in turn enabled cellcentric to ramp up its series production, while preparation for on-highway use is still in progress. Their installation into heavy-duty utility vehicles from Daimler Truck and Volvo is also planned.
Meanwhile, the novel bearing system for engines helps reduce friction and improves fuel economy by 1%. The new bearings reduce the amount of friction generated between bearing and crankshaft and also enable prediction of when maintenance will next be required.
The bearing surface, instead of being entirely smooth, features fine grooves, which, together with the lubricant, produce an aquaplaning-like effect which functions as an anti-friction layer.
This anti-friction layer reduces, for example, the friction-induced losses arising between crankshaft and bearing by 20-35%, depending on the operating mode. The innovative bearing is the result of a collaborative effort between a small project team in Friedrichshafen, bearing manufacturer Miba, and the MontanUniversität Leoben in Austria.
“We've succeeded in developing an optimised metal slide bearing that can be installed in our engines without the need for further modification. With just one easy production step extra, a 1% reduction in fuel consumption can be achieved that not only lowers costs, but avoids emissions,” pointed out Dr Otto Preiss, COO and CTO at Rolls-Royce Power Systems. mtu engines produced in higher volumes by the company are to be fitted with the new sliding bearing in the near future. mtu engines already in service will be retrofitted in the course of overhauls. The future plan is for the new bearing to be marketed as an individual component by Miba.
Use of the bearing in the engine reduces friction-induced losses, and while power output is maintained, fuel consumption drops by around 1%. Another benefit is that the novel bearing technology indicates when the next major maintenance work will be due by producing a change in the sound signature of the bearing. Premature maintenance is avoided and excessive wear identified in good time, saving material and operating costs.
The bearing, for which a patent is pending, is not only suitable for use in mtu engines from Rolls-Royce: “It is suitable for all equipment in which sliding bearings must withstand high loads," explained Dr Thomas Kottke, who is heading up the project.