Berco, the Italian heavy equipment machinery undercarriage parts manufacturer, is targeting strong growth after hitting back at what the firm describes as market competitor rumours of its decline and the relocation of much of its manufacturing capability to China.
Speaking during a construction equipment trade media and customer tour of Berco headquarters in Copparo, near Ferrara, in northern Italy, Matteo Seghieri, the company’s Global Aftermarket Sales Manager, said, “Berco went through a very importan
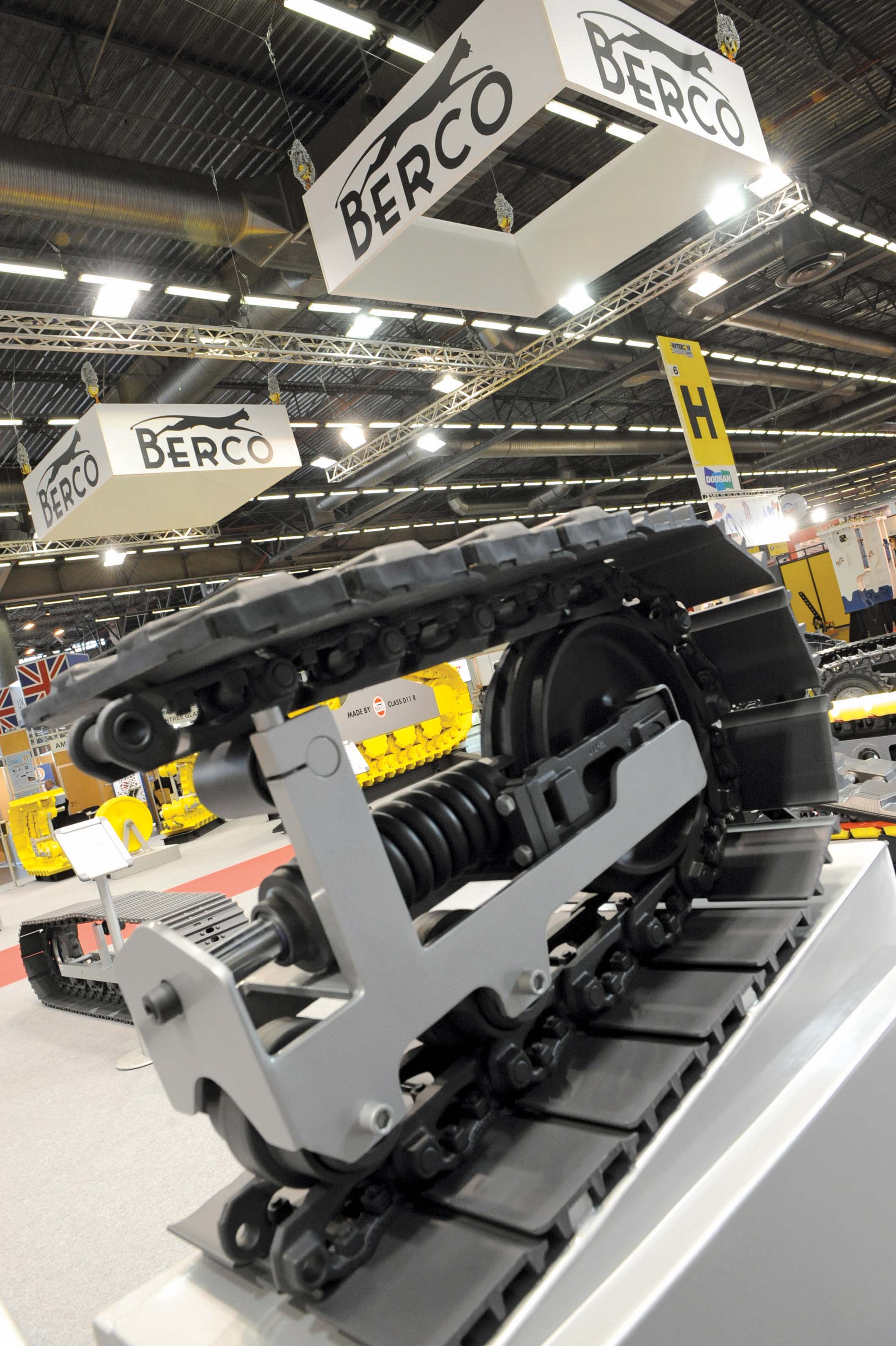
Berco is a world leading supplier of components such as track parts and undercarriages
Berco, the Italian heavy equipment machinery undercarriage parts manufacturer, is targeting strong growth after hitting back at what the firm describes as market competitor rumours of its decline and the relocation of much of its manufacturing capability to China.
Speaking during a construction equipment trade media and customer tour of2653 Berco headquarters in Copparo, near Ferrara, in northern Italy, Matteo Seghieri, the company’s Global Aftermarket Sales Manager, said, “Berco went through a very important restructuring last year. Now we want again to become a very important player in the market. With this visit, we also want to answer the rumours that our competitors are spreading, ranging from ‘Berco is disappearing from the market’, to ‘Berco is producing everything in China’. I believe today you have seen a factory that is producing in Italy and is our main plant. Our second Italian plant is in Castelfranco, Veneto - not in China.”
With market volatility linked to different currencies and import duties and the presence of strict import regulations, Berco is investing to localise certain products in low cost countries. This investment is in the company’s own manufacturing lines and what the firm says is its “well known quality standard”. While this move is aimed at local markets, the Copparo and Castelfranco facilities in northern Italy are said by the company to remain the heart of its production.
Stressing Berco’s near century long history of undercarriage production, Seghieri told Copparo HQ trade media and customer tour attendees how the firm was committed to delivering a traceable and consistent quality.
Berco’s Copparo factory tour revealed how the redesigned site now has dedicated lines for high volume components, and Flexible Manufacturing Cells (FMC) for lower volume products. This model production mix is said by the firm to be improving its flexibility and productivity.
“The changes we have made are already giving us a more agile and flexible supply chain, which is helping us to quickly adjust our production volumes to market demand, to serve our customers in the best way.”
Berco’s two largest (32,000tonnes and 16,000tonnes) presses, forging large components in a single stroke, are providing high quality products to the mining industry. Meanwhile, the company’s fully automated roller assembly lines are producing 100% quality inspected rollers for the majority of small and medium application, including rollers used in severe road construction equipment applications.
Of Berco’s complete frame production division, Seghieri said it is dedicated to the production of crawlers systems for utility track vehicles such as drilling machines, asphalt pavers, milling machines, and surface miners. “We have the capacity to design and produce frames in-house,” he added.
Seghieri also highlighted Berco’s use of 3D modelling. “We independently produce 3D models of all our products and processes, and we internally produce forging dies and other production tools used in our production lines. This is all value-added activity when it comes to engineering solutions for our customers.”
This capacity to internally design and produce components and systems is also said to be resulting in a very effective protection of not only Berco’s “know-how”, but also of customers, who ,the firm says, are more and more partners in the development of their new products.
Speaking during a construction equipment trade media and customer tour of
With market volatility linked to different currencies and import duties and the presence of strict import regulations, Berco is investing to localise certain products in low cost countries. This investment is in the company’s own manufacturing lines and what the firm says is its “well known quality standard”. While this move is aimed at local markets, the Copparo and Castelfranco facilities in northern Italy are said by the company to remain the heart of its production.
Stressing Berco’s near century long history of undercarriage production, Seghieri told Copparo HQ trade media and customer tour attendees how the firm was committed to delivering a traceable and consistent quality.
Berco’s Copparo factory tour revealed how the redesigned site now has dedicated lines for high volume components, and Flexible Manufacturing Cells (FMC) for lower volume products. This model production mix is said by the firm to be improving its flexibility and productivity.
“The changes we have made are already giving us a more agile and flexible supply chain, which is helping us to quickly adjust our production volumes to market demand, to serve our customers in the best way.”
Berco’s two largest (32,000tonnes and 16,000tonnes) presses, forging large components in a single stroke, are providing high quality products to the mining industry. Meanwhile, the company’s fully automated roller assembly lines are producing 100% quality inspected rollers for the majority of small and medium application, including rollers used in severe road construction equipment applications.
Of Berco’s complete frame production division, Seghieri said it is dedicated to the production of crawlers systems for utility track vehicles such as drilling machines, asphalt pavers, milling machines, and surface miners. “We have the capacity to design and produce frames in-house,” he added.
Seghieri also highlighted Berco’s use of 3D modelling. “We independently produce 3D models of all our products and processes, and we internally produce forging dies and other production tools used in our production lines. This is all value-added activity when it comes to engineering solutions for our customers.”
This capacity to internally design and produce components and systems is also said to be resulting in a very effective protection of not only Berco’s “know-how”, but also of customers, who ,the firm says, are more and more partners in the development of their new products.