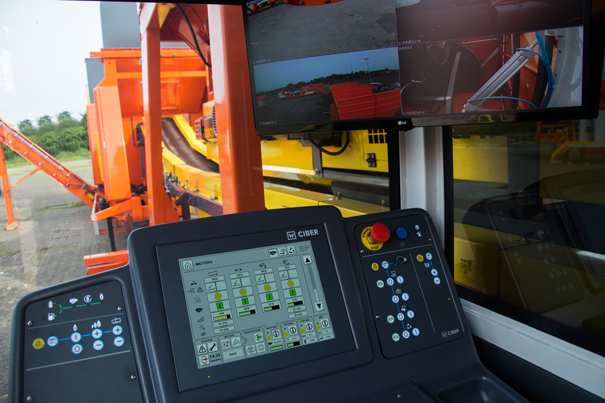
Preventive maintenance is a widely used method for maximising equipment uptime. Scheduled stoppages of machines are made according to the expected amount of wear, based on average statistics for generic equipment applications. Predictive maintenance is much more complex because it considers the condition and use of components, according to a specific application. This is used in order to schedule maintenance at the correct time. According to Marcelo Zubaran, application engineer and product specialist at
A predictive maintenance plan can be used for components featuring an abrasive wear rate, which develops over the lifetime of a tool. A plant’s mixer vanes exhibit wear proportional to the time they have been used. Examining the wear on the vanes, it is possible to predict when to replace the component. The condition of the plant’s bag filters are monitored indirectly during production by pressure meters installed in the filter box. This system indicates if the filters are likely to saturate. The meters help to prevent damage to the filter elements as well as wear to the plant hood.
State-of-the-art technologies can also be employed, such as constant monitoring of the power consumption of motors during production. When a motor starts drawing more power than usual, it can be a sign that a fault is developing. This type of fault diagnosis system also provides real-time information on the operating conditions of the motors to the plant operator. “If any of the plant motors are not operating at their optimum performance, an alarm is triggered immediately. The operator can select to stop production of an asphalt mix and then check the condition of the motor and even stop the plant if necessary. In this way, predictive maintenance technology allows the user to perform preventive maintenance," according to Zubaran.
For this technology to work, it is necessary for the motors to be connected to an electrical current measuring device. This system then has to be connected to a data transmission network. Frequency inverters are used to vary the speed of motors and are also capable of measuring the current running through a motor. In addition, soft start technologies used for big motors can also measure the electric current. Integral starter systems can be utilised to measure the current passing through motors also. These devices require a network interface to allow data to pass over to the plant’s computer, which will then analyses the information using software.