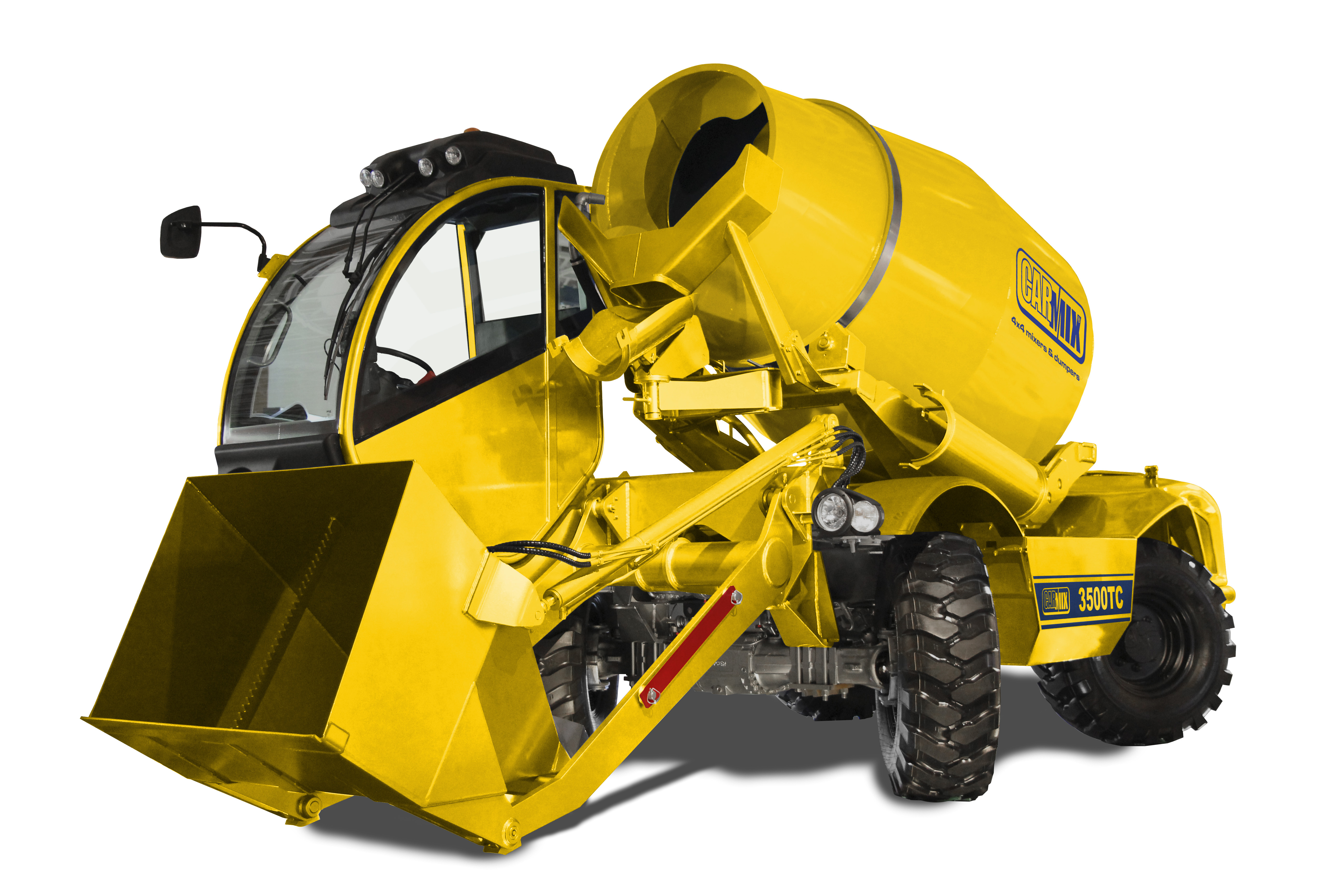
A batching unit has a material yield of 3.5m³ with double mixing screws. Mixing and discharge speed is independent from the speed of the diesel engine, and discharge is by reversing drum.
A joymix-controlled 600litre loader with a hydraulic door discharges sand or gravel directly into the drum. The unit can travel on slopes greater than 30%, even under full load, said Carmix.
Concrete-Mate, the mix design manager, includes an RMC Plant standard level management software. It uses four sensors in the mixing unit to ensure mix complies with international concrete production standards.
Up to 15 mixes and 99 types of material can be selected with Concrete-Mate, allowing the production of multiple combinations of materials. When the software stores a mix design, it suggests to the operator the dosage of each element, the sequence of operations and the working time for each process step. This eliminates the chance of error, according to the company.
Concrete-Mate can prepare concrete on site whose quality is confirmed by the Legal for Trade certificate, an accreditation certifying the superior accuracy of Concrete-Mate in all areas where these strict procedures are in force, such as Europe, Australia, Canada and Russia.
At the heart of Promix lies a stainless steel probe inside the mixing unit that is powered by a solar panel. Promix sends information in real time to a cabin display. The sensor provides data on slump, temperature, humidity, mixer rotation speed and notification of when the mix is ready.
All data is updated every 10 seconds and sent to the receiver. A display informs the operator on the parameters of the concrete being prepared. This information can be stored in an external computer or sent to other mobile devices via the GPS network.