The firm builds its plants in seven facilities around the world and is able to supply these to customers in all territories. Baldassari said, “We delivered to the market more than 140 plants/year.”
Mobility is one of the key features in many of the firm’s latest designs, which are containerised so as to speed transport, erection and commissioning. He explained, “This is the cheapest and easiest way to bring a plant to site.”
The company has different options for recycling and he said, “We are a leader and we reinforced this at
The firm’s TRX100 is a continuous plant capable of using up to 100% RAP in the feed for certain mixes. Meanwhile the Master Tower is a batching plant with an innovative end-to-end drum configuration that is also able to use up to 100% RAP in its feed.
Utilising RAP is an increasingly important factor for the road sector. Baldassari said, “You reduce the cost of ownership and you respect the environment through lower emissions and lower use of virgin materials.”
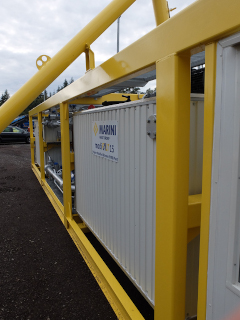
Emissions are further minimised with the firm’s latest systems by collecting dust, putting this back into the mix and also encapsulating the plant. The firm has also developed solutions for the production of warm mix, typically at temperatures 30°C lower than for hot mix, reducing emissions and fuel consumption.
Meanwhile other options include the firm’s dedicated cold mix plant and solutions for PMBs and its emulsion plants. Baldassari said, “PMB is becoming more popular in many countries because it makes roads stronger and more resistant to temperature changes.”
He added that retrofit solutions are also offered, “You can modernise your mix plant, whether it’s from us or not. We have a big portfolio of solutions.”