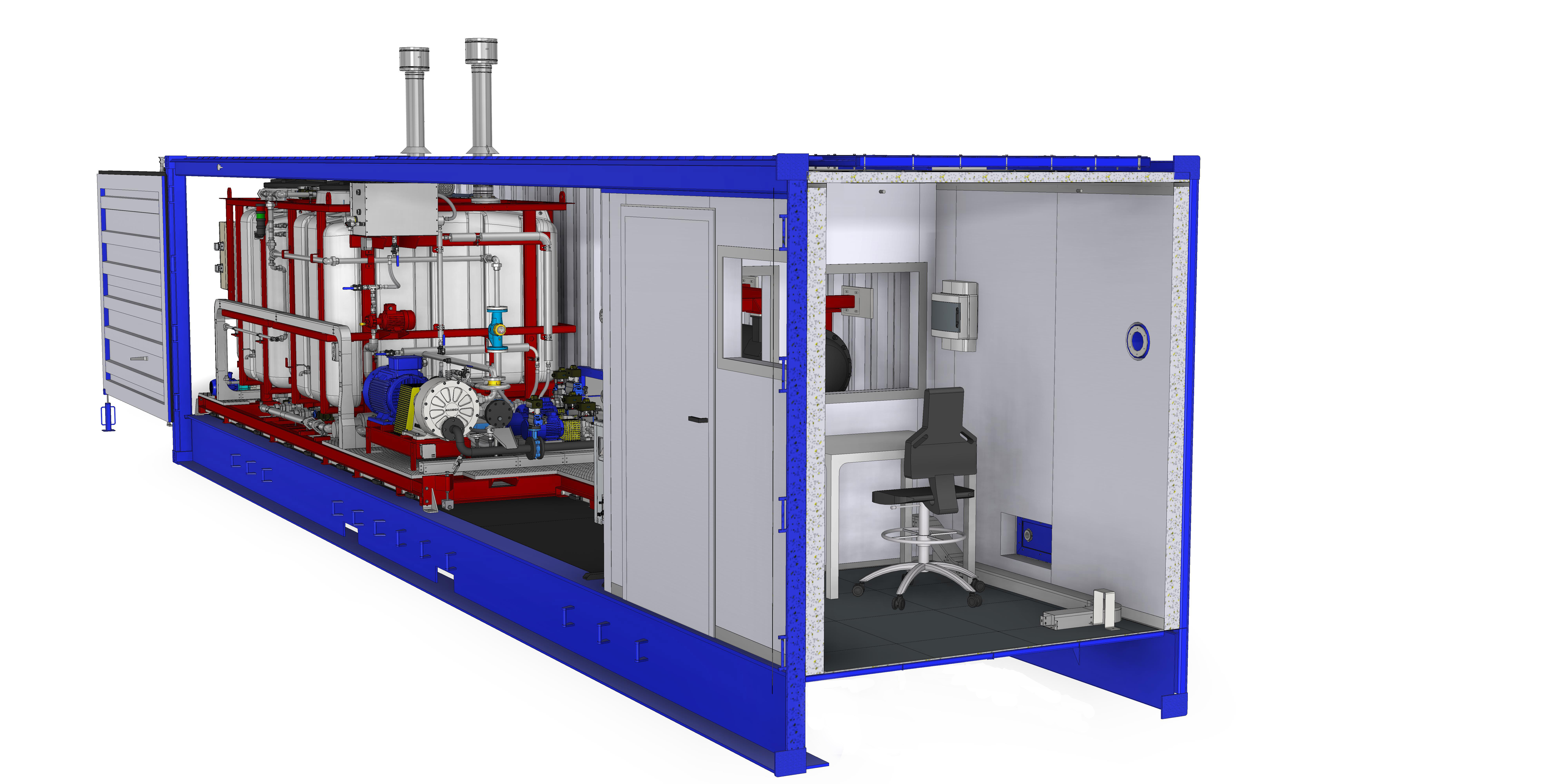
In developing a specialist bitumen emulsion plant for one of its major multi-national customers, Italian manufacturer Massenza has created a raft of additional features aimed to deliver maximum flexibility and production capacity.
Adaptations to its biggest and most advanced emulsion plant, MATIC 3500 AA TS, allow fast and efficient switches between different emulsion types. “We started from the basis of our MATIC 3500 plant and then worked in close cooperation with our customer’s engineering department to add several features so that it met their requirements,” said Andrea Menetti, Massenza’s commercial director.
The MATIC 3500 is already designed for high production, up to 20tonnes/hour. It has two water tanks which means that tank number two can be heating up ready for action while tank one is being used for emulsion production.
To allow quick and clean switching between cationic and anionic grades of emulsion, the bespoke plant was equipped with two fully separated lines for additives dosage, ensuring that the different chemicals used in the two different productions never come in contact with each other.
Additionally, an automatic cleaning procedure which sprays pure water round both water phase tanks has been incorporated. This must take place before the plant allows a different emulsion grade to be manufactured.
Polymer modified bitumen emulsion can be created via two different processes in this plant: conventionally with polymer modified bitumen or with the polymer added in latex form.
Since the plant will be used to produce polymer modified bitumen emulsions, which require higher production temperatures, Massenza developed a more efficient cooling system. The cooler can lower the heat of the emulsion by 40°C - rather than the standard 20°C - in one pass so that the emulsion exits at the right temperature. Additionally, a heating system in the lower part of the tank ensures that no residues of cold, hard bitumen build up.
Massenza’s customer, which has been buying emulsion plants, PMB plants and other equipment from the manufacturer for more than 20 years, required other modifications too. To ensure clean and green operation, the plant uses electrical power rather than fossil fuel to heat the oil – a system which Massenza developed within a month.
Because the plant will be located in a desert in the Middle East, it had to fit within a container to protect it from both sandstorms and the possibility of thieves. “Some of the challenges related to that were ensuring that there was enough space for maintenance and also creating openings so that the fumes, especially the steam, could escape,” said Menetti. “We also had to ensure that the container would still receive accreditation for shipping, with someone coming to inspect it before and after the modifications.”
A further modification saw the control plant board – usually located close to the plant itself – moved to its own room within the container and which could not be accessed via the plant area.
Although Massenza often creates bespoke plants for its customers, Menetti said he believes this is the most complex set of modifications it has made for an emulsion plant – and all in less than six months. However, all the hard work on design and fabrication means that future customers could also benefit from a wider choice of modifications, should they need them.