
Progress has been rapid in the aggregates production market, with key manufacturers introducing more efficient technology. High output and high efficiency can be achieved with the latest developments available to customers.
An array of options and systems are now available that can help quarrying firms optimise productivity. More efficient crushing and screening can make major savings in costs, reducing wastage and ensuring firms benefit from better quality product.
Optimising plant design is key for throughput and Metso is introducing important technology aimed at boosting crushing efficiency, including a new system for designing plant layout, plus a new cone crusher. The My Plant Planner system is available on the firm’s website and is an online tool for designing efficient crushing and screening plants. This system features a novel drag and drop 3D crushing and screening plant tool that allows aggregate sector customers to design productive and efficient plants through real-time insights.
The tool means that customers can design and simulate different crushing and screening circuit configurations and operating conditions to see how they affect process performance. A user can either design and simulate a new crushing and screening plant in 3D or test how upgrading current equipment can improve performance.
The tool is based on proprietary Metso software and can be used to download a detailed report of the designed plant. The system allows the user to predict power consumption of the system and to see the footprint of the circuit. A designer can select different types of crushers, screens and conveyors to optimise the circuit and identify bottlenecks to understand where extra capacity is needed. Factors such as capacity, load, and power draw are updated in real time as the circuit is designed and the parameters updated.
Cone crushing
The Nordberg HP900 Series cone crusher suits customers in the aggregate production market and is designed to offer increased performance and reduced capital expenditure. The model is an upgrade of the proven HP800 cone crusher and there is around 80% parts commonality between the two.
Features of the HP900 include improved kinematics, raised pivot point and a power increase, boosting capacity by 15%, as well as a new lubrication system.
The HP900 is delivered pre-assembled, prewired and factory tested. The equipment is packaged with a rubber-pad mounted subframe and guards allowing quick and safe setup with a compact footprint, reducing installation time by 50%.
The crusher has the firm’s proven and reliable tramp iron release system, minimising production stoppages and protecting components, while good service access to the head, shaft, eccentric and other major components make disassembly safe and easy. The crusher features Metso's IC70C automation system to ensure optimum operating parameters. Information can be tracked using a single screen and features help and trouble-shooting options.
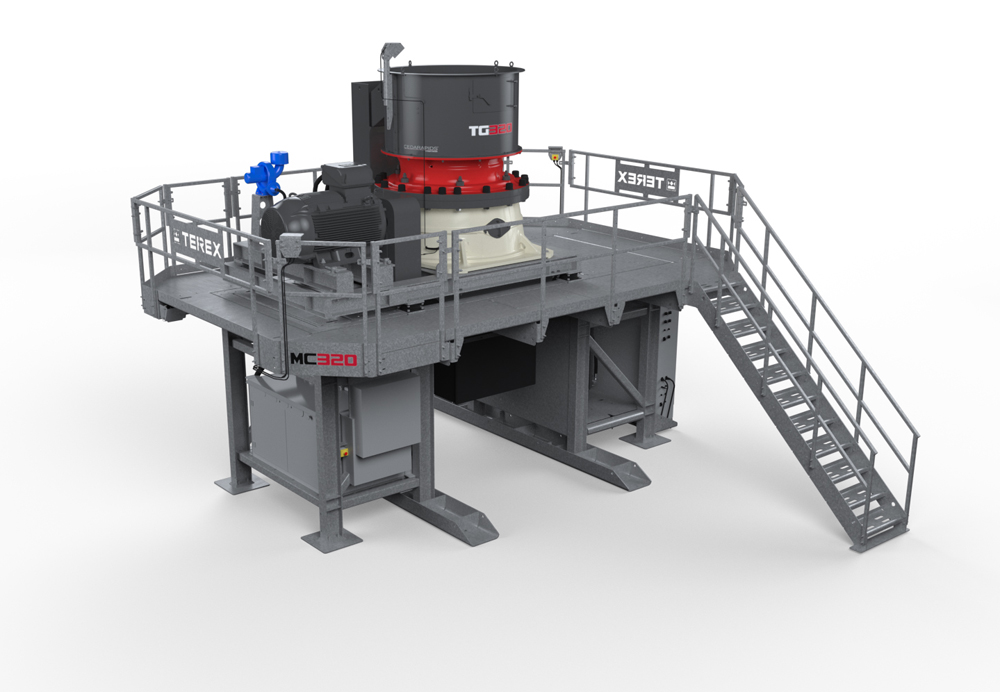
Meanwhile, Terex says that its MC320 cone module benefits from having the TG320 or optional TGS320 cone on the same universal base structure as the MC and MV Series modular lines. The all-electric, pre-engineered solution can be easily transported in standard containers and can be bolted together onsite quickly with basic tools and minimal wiring, and installed with or without full concrete foundations. The TG320 is a 225kW bushing cone with large feed opening, adjustable eccentric throw and multiple liners, which is designed to optimise production in all applications.
The 1800/1500 rpm motor and crusher are mounted on a rubber isolated frame, common between modular, portable and static platforms. The MC320 comes with standard AIC crusher controls. Additional options include an overflow chute and off plant conveyor starter kit.