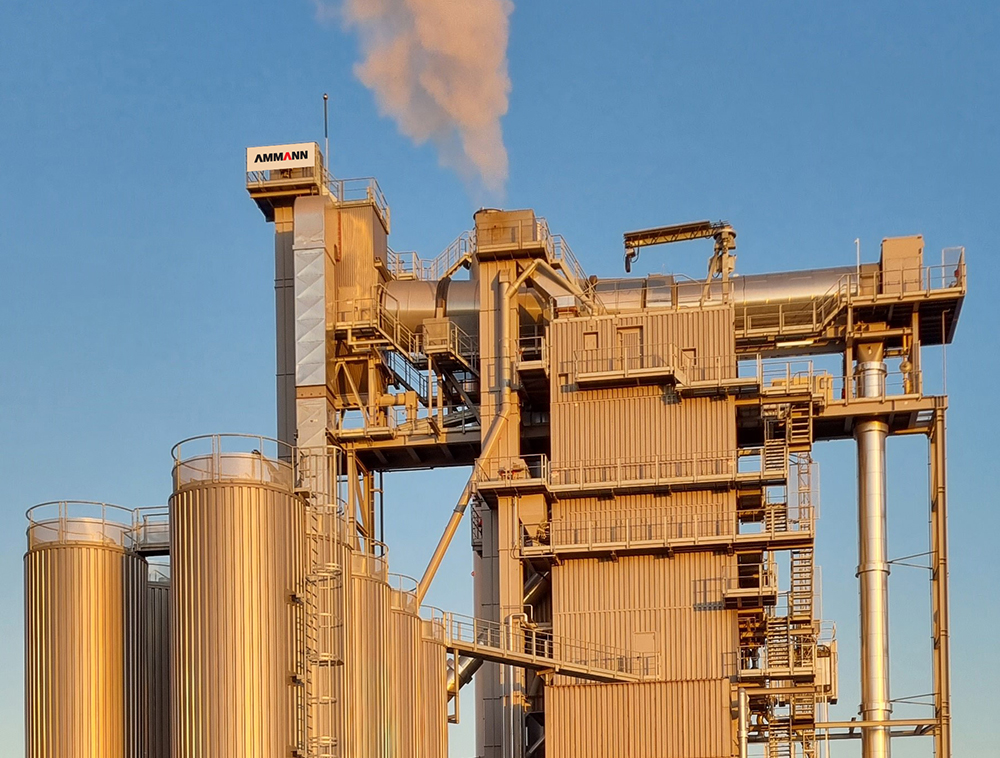
“As the time comes to reduce the industry’s carbon footprint, this plant, and its related infrastructure, will help our customers achieve their environmental objectives,” said Dante Cremasco, head of Road Services at Downer.
The Ammann ABP 320 HRT (High Recycling Technology) Asphalt-Mixing Plant features the firm’s RAH100 drying drum and can make mix entirely from recycled materials. It has the capability to use up to 100% RAP and incorporate other waste materials – such as glass, recycled print cartridges, soft plastics, and packaging.
The market is changing to better address environmental impacts and higher levels of recycling are being accepted by end users. The Ammann plant has the flexibility to produce conventional asphalt but is also equipped to future challenges.
“It’s significantly advanced,” Cremasco said of the plant, which began full operation in Sydney in June 2022. According to Cremasco a key benefit of the plant is, “…its ability to incorporate numerous recycling components, while still being capable of producing standard virgin mixes.”
Able to supply 320tonnes/hour, the plant can satisfy high-volume customers. “It’s also flexible to service the smaller ex-bin customers at any time,” he said.
Downer opted for the plant to service the Sydney community as it can quickly change recipes. “With the batch plant, we can minimise waste and improve cycle times and most importantly, service more of our customers’ demands,” Cremasco said.
Downer commenced planning for a new plant about two years ago. The firm opted for an Ammann plant based on the success of the other Ammann plants it owns. This new plant allows Downer to leverage its years of experience in innovative asphalt products and enable it to efficiently meet the needs of its customers. “Previously, we had six hot asphalt silos, at 200tonnes each,” Cremasco said. “We now have a similar volume in 10 silos. That gives us more flexibility.”
The plant has five RAP feeders that provide the flexibility to supply the top drum or go directly to the mixer. Downer can include up to three different granular additive types in a mix and up to three liquid additives. The facility can vertically store 6,000tonnes of aggregate and 720m3 of bitumen.
The plant is also equipped with oversized silos for reclaimed and imported fillers. “We have about 500m3 of fillers available across three separate silos, so we’re sure to have the ability to bring the materials in,” Cremasco said. “The hot asphalt silos give us the flexibility to store the mix, so we can keep the plant flexible and efficiently change the mixes on the run.”
Six aggregate cold feed bins complement the bunker storage system to assist with any specialty mix production or serve as backup. The firm is well set up for the use of RAP. “Downer has constructed a highly advanced RAP processing plant immediately adjacent to the asphalt plant that can shred, fractionate and store the RAP so it’s ready for immediate introduction into the plant,” Cremasco said.
Australia has a goal of carbon neutrality by 2050, with incremental steps along the way. While some targets are voluntary, certain standards must be met in order to do business with the government. The Downer facility helps to reduce that footprint for customers. Currently, about 25% of mix produced in Australia has recycled content. “This plant allows us to significantly increase those percentages,” Cremasco said. “We’re hoping to progressively increase the recycle content to at least 60% in coming years.”
The plant emissions also easily meet Australia’s tough standards according to Cremasco. Downer continues to work on producing high-quality mixes at increasingly lower production temperatures. “More and more foaming will be the result. We’re reducing the temperature of products by a few degrees/year.”
The long-term goal is producing asphalt at ambient temperatures. “We’re doing lab trials on that and making progress,” he said. A team of scientists has been working on the ambient temperature project for some time.
“The team is really committed. We see the importance of removing heat, and hence energy, from what we do,” he added.