Effective washing processes are crucial to providing quality materials. Materials washing specialist CDE is offering three updated machines, the Evowash, the M2500 and the Agg Max 83R. All three machines have benefitted from improvements compared to previous versions but the Evowash unit features the most changes, including two ideas with patents pending. “We have been evolving the Evowash ever since we invented it 20 years ago, hence its name,” said Iain Walker, technical sales manager for the Middle East.
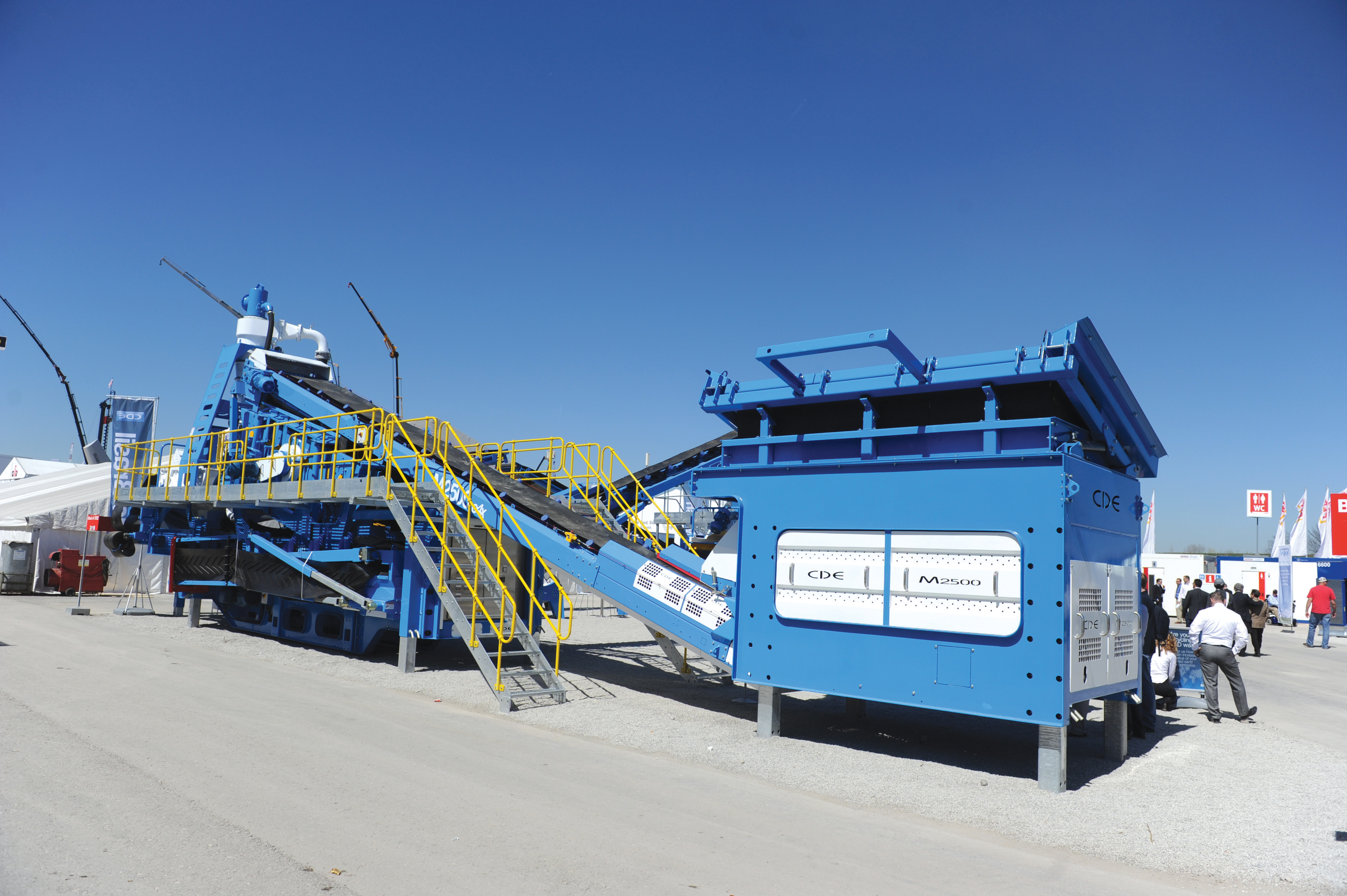
From CDE Global comes an innovative approach to materials washing technology
RSSEffective washing processes are crucial to providing quality materials. Materials washing specialist 3168 CDE Global is offering three updated machines, the Evowash, the M2500 and the Agg Max 83R. All three machines have benefitted from improvements compared to previous versions but the Evowash unit features the most changes, including two ideas with patents pending. “We have been evolving the Evowash ever since we invented it 20 years ago, hence its name,” said Iain Walker, technical sales manager for the Middle East. “But this is the first time we have made such a large number of changes at once.”
CDE has made radical changes to the dewatering screen. First, the whole structure is bolted rather than welded, since welds are a potential weak spot when the screen is vibrating. Second, rather than mounting the motors on a bridge structure which spans either side of the screen to brace the metal sides, the motors are an integral part of the structure. This reduces the weight of the screen by 30% and means that it requires 30% less power. Finally, the feed box is on rails, which means it can be moved forward to provide more space for maintenance. Other improvements include mounting the pump on a turntable so that it can be swivelled round to allow easy access for maintenance. A built-in boom means there is no additional lifting gear, and one person can work on the pump. The boom can be dismantled, unbolted and re-erected next to the screen to aid maintenance of the motors.
The M2500, first launched by CDE in 2010, combines a loading hopper, inclined feed conveyor, two-deck washing screen and integrated Evowash. “It was the first of its type,” said Walker. The latest version incorporates a number of modifications, most of them aimed to make maintenance easier, safer and faster. Some of the improvements made on the newest Evowash have already fed through into the M2500.
The AggMax 83R is a scrubbing machine, which has found most of its customers in the UK, but is now being bought by operators in other European countries and the Middle East. Here again, CDE has made a tranche of improvements, including changes to the design to increase its efficiency and durability. “Customers are finding that material from quarries which they would previously have considered as waste can now be turned into useful sand and aggregate,” said Walker. “It’s a way of conserving resources.”
3004 W.S. Tyler says that its Hydro-Clean washing system is now available on a chassis for extra mobility, allowing it to be moved from site to site. The working features have been retained and a spokesperson for the firm said, “It uses 75% less water than a traditional washing plant. It also uses about 15% less power as well.”
The wheel-mounted chassis was offered following a customer request and the spokesperson said, “People told us they wanted to move the equipment to different sites. It’s not quite plug and play though and you have to know how to set it up.”
The Hydro-Clean removes silt and clay particles faster than traditional methods, which require soaking the material for long periods to loosen unwanted debris. Of the total volume of wastewater, up to 90% can be recycled and reused in the Hydro-Clean, which only requires 10% fresh water to operate effectively. Hydro-Clean units require less energy than other washers, ranging from 26kW on the smallest of three models to 225kW on the largest, while the machines also weigh up to 60% less than conventional units. The machine features a four bearing, double eccentric screen and the spokesperson added, “There’s no vibration in the chassis.”
Unlike a traditional washing unit, which can require up to three screens along with a log washer or screw, the Hydro-Clean only requires a single rinse screen for discharged material. The only other requirements are a water source, a pump station and a feed conveyor.RSS
CDE has made radical changes to the dewatering screen. First, the whole structure is bolted rather than welded, since welds are a potential weak spot when the screen is vibrating. Second, rather than mounting the motors on a bridge structure which spans either side of the screen to brace the metal sides, the motors are an integral part of the structure. This reduces the weight of the screen by 30% and means that it requires 30% less power. Finally, the feed box is on rails, which means it can be moved forward to provide more space for maintenance. Other improvements include mounting the pump on a turntable so that it can be swivelled round to allow easy access for maintenance. A built-in boom means there is no additional lifting gear, and one person can work on the pump. The boom can be dismantled, unbolted and re-erected next to the screen to aid maintenance of the motors.
The M2500, first launched by CDE in 2010, combines a loading hopper, inclined feed conveyor, two-deck washing screen and integrated Evowash. “It was the first of its type,” said Walker. The latest version incorporates a number of modifications, most of them aimed to make maintenance easier, safer and faster. Some of the improvements made on the newest Evowash have already fed through into the M2500.
The AggMax 83R is a scrubbing machine, which has found most of its customers in the UK, but is now being bought by operators in other European countries and the Middle East. Here again, CDE has made a tranche of improvements, including changes to the design to increase its efficiency and durability. “Customers are finding that material from quarries which they would previously have considered as waste can now be turned into useful sand and aggregate,” said Walker. “It’s a way of conserving resources.”
The wheel-mounted chassis was offered following a customer request and the spokesperson said, “People told us they wanted to move the equipment to different sites. It’s not quite plug and play though and you have to know how to set it up.”
The Hydro-Clean removes silt and clay particles faster than traditional methods, which require soaking the material for long periods to loosen unwanted debris. Of the total volume of wastewater, up to 90% can be recycled and reused in the Hydro-Clean, which only requires 10% fresh water to operate effectively. Hydro-Clean units require less energy than other washers, ranging from 26kW on the smallest of three models to 225kW on the largest, while the machines also weigh up to 60% less than conventional units. The machine features a four bearing, double eccentric screen and the spokesperson added, “There’s no vibration in the chassis.”
Unlike a traditional washing unit, which can require up to three screens along with a log washer or screw, the Hydro-Clean only requires a single rinse screen for discharged material. The only other requirements are a water source, a pump station and a feed conveyor.RSS