New developments for the milling machine sector should help optimise performance, as well as increase health and safety standards for site personnel
Advances in the milling machine market generally focus on new models being available or developments to drums and cutters. However some rather different developments are taking place that could well deliver long-term improvements for health and safety as well as the quality of work carried out, optimising milling operations.
Earlier this year, new guideli
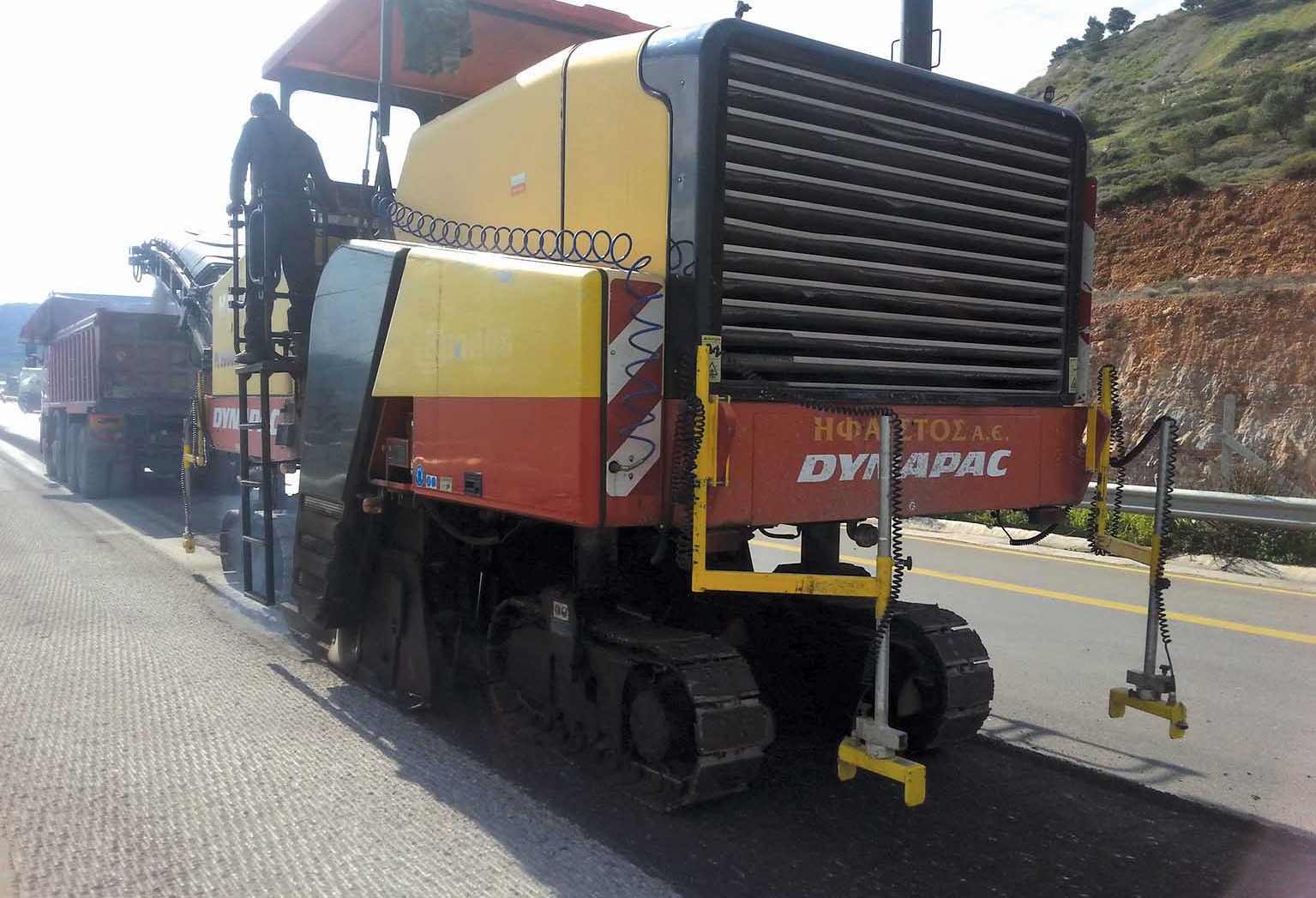
The new MOBA system has proven its worth in optimising milling operations
New developments for the milling machine sector should help optimise performance, as well as increase health and safety standards for site personnel
Advances in the milling machine market generally focus on new models being available or developments to drums and cutters. However some rather different developments are taking place that could well deliver long-term improvements for health and safety as well as the quality of work carried out, optimising milling operations.
Earlier this year, new guidelines on cold milling were introduced, designed to reduce airborne silica particles on work sites. Called Best Practice Engineering Control Guidelines to Control Worker Exposure to Respirable Crystaline Silica during Asphalt Pavement Milling, the guidelines represent a significant development.
These are the culmination of 10 years of collaborative research in the industry and the guidelines are available from the5159 National Institute for Occupational Safety and Health (NIOSH)—Publication No 2015-105.
The research is intended to address concerns over the health implications of airborne silica dust, known to be a problem in other sectors.
The collaboration began in 2003, when the3464 National Asphalt Pavement Association (NAPA) helped form a Silica/Milling Machine Partnership. This was tasked with evaluating milling machines and silica exposure hazards to protect site personnel. This partnership includes the International Union of Operating Engineers, the Laborers’ International Union of North America, equipment manufacturers 1252 Roadtec, 7659 Volvo Construction Equipment, 2395 Wirtgen America, 3956 Terex Roadbuilding and 178 Caterpillar, the 1100 Association of Equipment Manufacturers (AEM) and NIOSH. And it is of note that rival manufacturers have come together to pool knowledge in a bid to improve health and safety onsite.
The first stages, from 2003 through to 2006, were aimed at understanding exposure levels and where dust is generated internally by the machines. This technical exercise led the team to look at optimising and improving water systems in the machines. Some research was carried out on how best to optimise the nozzle systems to get at the source of the dust. Field trials were held where manufacturers shared their research regarding spray, ventilation, and vacuum systems.
The work has now resulted in standard industry cold milling guidelines for reducing airborne silica particles on asphalt milling sites. There are two key elements to the guidelines for restricting worker exposure to respirable crystaline silica during asphalt pavement milling. These are for the use of ventilation controls and water sprays to cool the cutting teeth. When combined, these two elements can consistently reduce exposures below the NIOSH-recommended limit of 0.05 mg/m3.
In addition, best practice recommendations for water sprays have been developed for contractors that are not using ventilation controls on their asphalt milling machines. The two best methods for achieving this are to spray water on the pavement being milled to suppress any dust and to reduce airborne dust by spraying the dust cloud.
As a key component of any milling machine is its water spray system for cooling cutter bits on the cutter drum, this can offer a dual purpose of controlling respirable dust. But to maximise the effectiveness of water spray systems, several alterations may need to be made to optimise the flow, pressure and nozzle locations.
Meanwhile German firm1228 MOBA is now offering a system that can help optimise milling quality. The company is introducing its Big Sonic-Ski system, which suits use with road milling machines (as well as pavers).
The Big Sonic-Ski works with the MOBA-matic levelling system and be used to deliver a more uniform surface. Using the system means that a milled surface will be more even so that when it comes to paving a road with new asphalt there will be less waste of materials that would otherwise be required to fill in uneven areas on the milled surface. According to MOBA, the system can quickly pay for itself due to the savings in materials costs.
The system was proven on a site in Greece during the renovation of the road connecting Schimatari and Chalcis, around 50km from the capital Athens. The job involved the renovation of a 10km stretch of road that had originally been built in 2009.
A major issue in Greece is that the specifications for paving jobs are very old, so levelling systems are not required from the authorities. Worse still, the authority that had supervised the project had been rushed to accept the work due to time delays. As a result, the surface layer of the road was already completely unusable after little more than five years in service. The problem was that it had a lot of uneven areas, but at the same time was absolutely flat in other places. This situation also led to a high rate of crashes on this stretch of road and as a result, a new surface had to be laid.
The surface layer was milled away to a depth of 50mm. The contractor that carried out the milling work, Ifaistos, deployed a Big Sonic-Ski using two ultrasound sensors and a wire rope sensor on its milling machine. The firm was well aware that achieving high quality at the milling stage was key to providing a good surface on which to pave and avoiding problems of unevenness that eventually lead to premature damage to the road surface or uneven spots that have to be levelled out using additional material, increasing overall costs.
And Ifaistos also used the MOBA Big Sonic-Ski on its asphalt paver, laying new asphalt on the freshly milled surface. The system sends out five ultrasound beams to detect the road level. From the values returned by these soundings, the two values with the largest deviations are set aside. This ensures that measurement inaccuracies caused by stones for example are eliminated from the calculations. A mean value is obtained from the three mid-range measurements. The measured values for all three Sonic-Skis are then used by the computer to calculate their mean value and provide a virtual reference level for the levelling job. This has the effect that the uneven areas on the substrate are levelled out instead of simply being reproduced, delivering the necessary evenness.
As a result, the wave effect on the surface has now been eliminated and the stretch of road has been resurfaced with a quality mat that should last considerably longer and help improve safety also.
According to MOBA, its system is also very easy to operate, as all its main functions can be controlled using four buttons, and important values are shown on the display. The MOBA-matic II control panel can be used for both milling and paving as it is possible to use a variety of different sensors.
Advances in the milling machine market generally focus on new models being available or developments to drums and cutters. However some rather different developments are taking place that could well deliver long-term improvements for health and safety as well as the quality of work carried out, optimising milling operations.
Earlier this year, new guidelines on cold milling were introduced, designed to reduce airborne silica particles on work sites. Called Best Practice Engineering Control Guidelines to Control Worker Exposure to Respirable Crystaline Silica during Asphalt Pavement Milling, the guidelines represent a significant development.
These are the culmination of 10 years of collaborative research in the industry and the guidelines are available from the
The research is intended to address concerns over the health implications of airborne silica dust, known to be a problem in other sectors.
The collaboration began in 2003, when the
The first stages, from 2003 through to 2006, were aimed at understanding exposure levels and where dust is generated internally by the machines. This technical exercise led the team to look at optimising and improving water systems in the machines. Some research was carried out on how best to optimise the nozzle systems to get at the source of the dust. Field trials were held where manufacturers shared their research regarding spray, ventilation, and vacuum systems.
The work has now resulted in standard industry cold milling guidelines for reducing airborne silica particles on asphalt milling sites. There are two key elements to the guidelines for restricting worker exposure to respirable crystaline silica during asphalt pavement milling. These are for the use of ventilation controls and water sprays to cool the cutting teeth. When combined, these two elements can consistently reduce exposures below the NIOSH-recommended limit of 0.05 mg/m3.
In addition, best practice recommendations for water sprays have been developed for contractors that are not using ventilation controls on their asphalt milling machines. The two best methods for achieving this are to spray water on the pavement being milled to suppress any dust and to reduce airborne dust by spraying the dust cloud.
As a key component of any milling machine is its water spray system for cooling cutter bits on the cutter drum, this can offer a dual purpose of controlling respirable dust. But to maximise the effectiveness of water spray systems, several alterations may need to be made to optimise the flow, pressure and nozzle locations.
Meanwhile German firm
The Big Sonic-Ski works with the MOBA-matic levelling system and be used to deliver a more uniform surface. Using the system means that a milled surface will be more even so that when it comes to paving a road with new asphalt there will be less waste of materials that would otherwise be required to fill in uneven areas on the milled surface. According to MOBA, the system can quickly pay for itself due to the savings in materials costs.
The system was proven on a site in Greece during the renovation of the road connecting Schimatari and Chalcis, around 50km from the capital Athens. The job involved the renovation of a 10km stretch of road that had originally been built in 2009.
A major issue in Greece is that the specifications for paving jobs are very old, so levelling systems are not required from the authorities. Worse still, the authority that had supervised the project had been rushed to accept the work due to time delays. As a result, the surface layer of the road was already completely unusable after little more than five years in service. The problem was that it had a lot of uneven areas, but at the same time was absolutely flat in other places. This situation also led to a high rate of crashes on this stretch of road and as a result, a new surface had to be laid.
The surface layer was milled away to a depth of 50mm. The contractor that carried out the milling work, Ifaistos, deployed a Big Sonic-Ski using two ultrasound sensors and a wire rope sensor on its milling machine. The firm was well aware that achieving high quality at the milling stage was key to providing a good surface on which to pave and avoiding problems of unevenness that eventually lead to premature damage to the road surface or uneven spots that have to be levelled out using additional material, increasing overall costs.
And Ifaistos also used the MOBA Big Sonic-Ski on its asphalt paver, laying new asphalt on the freshly milled surface. The system sends out five ultrasound beams to detect the road level. From the values returned by these soundings, the two values with the largest deviations are set aside. This ensures that measurement inaccuracies caused by stones for example are eliminated from the calculations. A mean value is obtained from the three mid-range measurements. The measured values for all three Sonic-Skis are then used by the computer to calculate their mean value and provide a virtual reference level for the levelling job. This has the effect that the uneven areas on the substrate are levelled out instead of simply being reproduced, delivering the necessary evenness.
As a result, the wave effect on the surface has now been eliminated and the stretch of road has been resurfaced with a quality mat that should last considerably longer and help improve safety also.
According to MOBA, its system is also very easy to operate, as all its main functions can be controlled using four buttons, and important values are shown on the display. The MOBA-matic II control panel can be used for both milling and paving as it is possible to use a variety of different sensors.