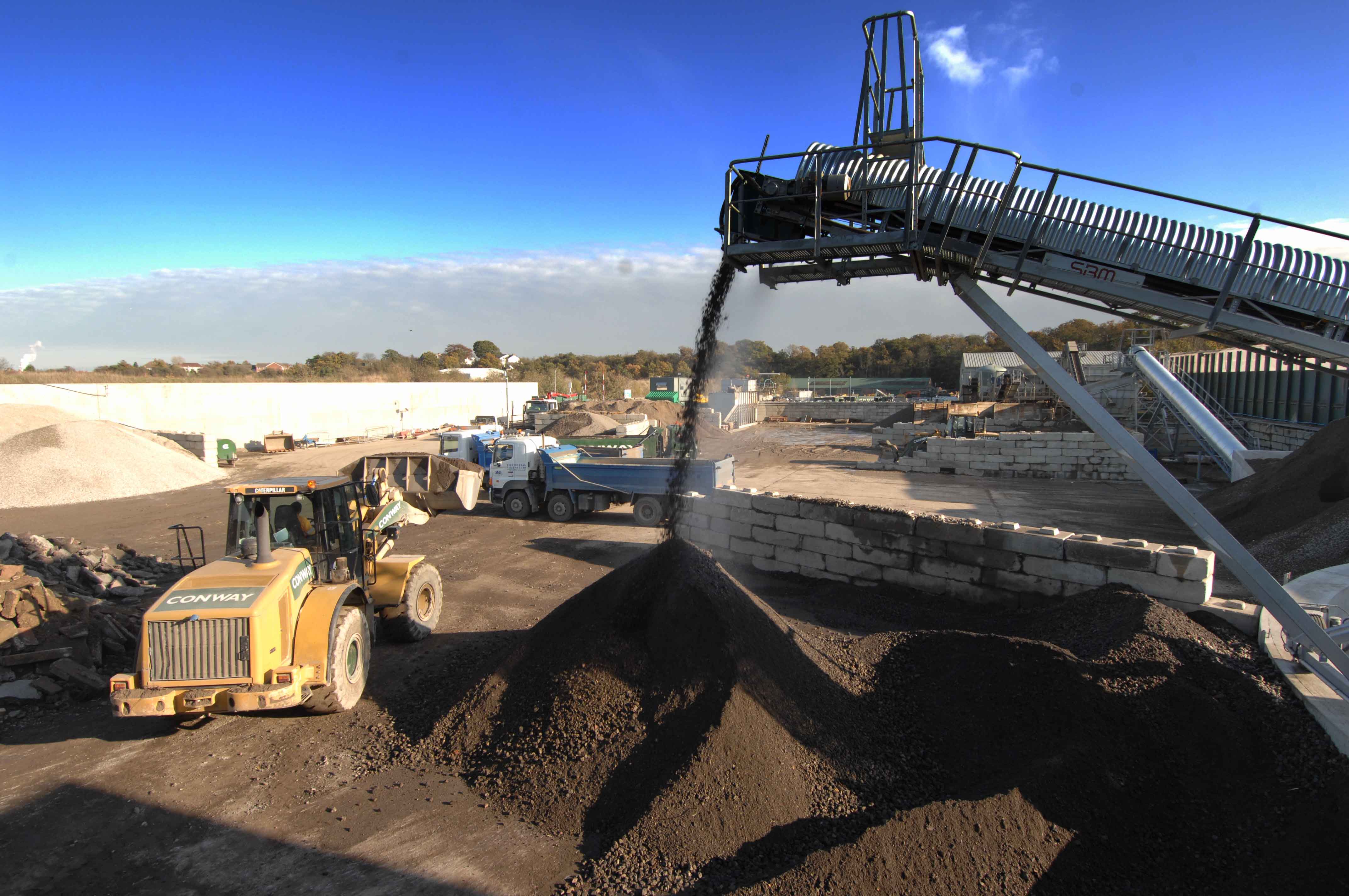
Britain’s infrastructure remains high on the public and political agenda, not least the state of our extensive road network. Estimated to be worth around £344 billion, much of our road network’s inherent value resides in the billions of tonnes of asphalt within the asset.
With Highways England’s £15.7 billion Road Investment Strategy, significant investment will be made to improve England’s strategic network over the next five years. The large-scale renewal of the road network comes not just at high financial cost but at a significant environmental cost too.
In the south-east of England in particular, there is a need to be more resource efficient. High Polished Stone Value aggregates are geologically scarce and must be imported to the region, adding to the logistical costs and carbon miles of road maintenance projects.
One obvious solution is, of course, recycling. Asphalt recycling is not new to the highways industry, but its use for the surface courses of strategic routes remains underexploited.
In the base and binder layers of Britain’s roads it is routine to incorporate asphalt with more than 50% recycled content and even up to 75% on lightly busy routes. However, when it comes to the surface course, many still remain wary of adding material with a recycled content of more than 10%.
This reluctance is not from any limitations within the relevant guideline specifications. It is more a case of ingrained custom – habitual practice which few wish to challenge. Highways teams are often concerned that high recycled content asphalt will not provide satisfactory skid resistance, especially on strategic routes.
FM
The firm has recently launched a trial with Transport for London (TfL) to test the use of a 50% recycled content asphaltic mix for the surface course of a three-lane highway in the capital – the first time that this has been attempted on a strategic route in the UK.
The mix – which is fully compliant with clause 942 of the Specification for Highway Work – contains a polymer modified bitumen to increase the carriageway’s durability. This route will be monitored to ensure that it retains the required surface texture and skid resistance.
The trial is still ongoing, but the firm is confident it will show that the use of high recycled content material for both surface courses and the lower layers of roads not only meets the specified safety requirements, but can significantly lower both the environmental impact and the costs of highways maintenance. In the south-east of England, where geologically scarce high PSV aggregates must be imported, the potential financial and logistical benefits could be greater still.
To make the use of high recycled content asphalt an integral part of road construction in the UK, it is necessary to rethink the way we source and process recycled materials.
Traditionally, RA is recovered from existing roads up to a depth of 100mm in a single operation. This means the material contains both high skid resistant surface asphalt and low skid resistant product from the lower layers – rendering it unsuitable for the surface courses of high-speed strategic routes.
By being more selective in the choice of recovery sites – taking RA only up to a depth of 35mm from multiple locations – it is much easier to control the properties of the resultant material.
The main barrier to this approach is a lack of data about what roads are actually made of. It is crucial to know the accurate materials composition of the highways to be able to make an informed choice as to which sites are the most suitable for asphalt recovery.
One solution is to integrate the processes of coring and testing into ongoing road maintenance programmes. Coring is often undertaken by highways contractors as part of routine maintenance, but the information about aggregate type and bitumen quality gleaned from petrographic analysis of these samples is rarely logged in a central database. Storing this data would allow highways authorities to quickly build up a databank cataloguing the quality and quantity of recoverable RA on a street by street basis.
Establishing these recycling databases may seem like a complex task but by working together, asset management teams and contractors can achieve considerable time and cost efficiencies.
If a road is being closed to replace highways signage, for example, there is no reason that coring couldn’t be undertaken at the same time, minimising both the cost of data collection and disruption to the public. At FM Conway, whenever the firm is carrying out maintenance works it now requests that the local authority in question informs other relevant teams about the project so they can make best use of the road closure.
Councils must also draw on their contractors’ technical knowledge and infrastructure to store recycled materials and ensure that the sourcing of RA from multiple sites meets the same quality control standards as those applied to the procurement of virgin material.
Any samples of asphalt recovered by FM Conway are transported to the central processing depot where they can be analysed and processed to optimise the quality of the recovered material. For example, a simple aerosol colour test is used to determine whether a batch contains tar. If positive, the material is deemed hazardous and removed to a specialist waste site.
Establishing the credentials for asphalt’s unlimited reuse must be part of a bigger shift in the way we approach construction materials – not just in the highways sector but across the wider construction industry too.
As a naturally resource intensive and waste heavy industry, construction is under increasing pressure from policymakers to embrace a more circular economic approach to resources. Materials have to be kept in use for as long as possible and then recovered and regenerated at the end of their service life to be used again.
Both the EU’s Circular Economy Package, released in late 2015, and the London Circular Economy Route Map, currently being developed by the Greater London Authority (GLA) and the London Waste & Recycling Board (LWARB), highlight the built environment and construction as critical to making the transition to a circular economy a reality.
It is the duty of those operating in the highways sector to act responsibly and ethically, but answering this call also offers clear commercial advantages for our industry. The EU estimates that a more circular approach to materials could support significant job creation and bring net savings of €600 billion for European businesses.
The large-scale maintenance of England’s strategic road network provides the highways industry with a unique opportunity to embrace best practice when it comes to the use and reuse of materials. Change will not be made overnight, but hopefully, trials such as that currently underway with Transport for London will encourage others to reassess the role that RA can play not just on local roads, but across the entire strategic network.
Making unlimited asphalt recycling a central element of asset management and renewal plans will require the time and collaboration of contractors and highways authorities. However, the difficulties are far outweighed by the potential environmental savings.