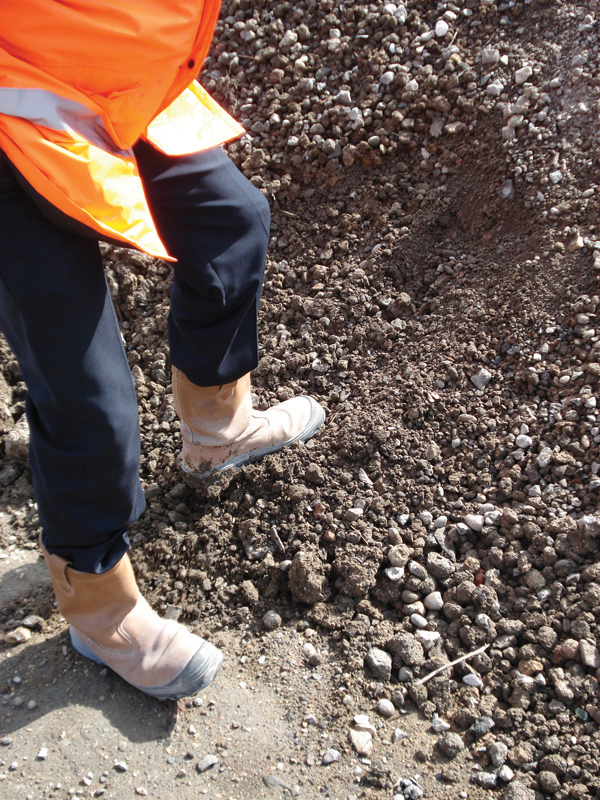
Day Aggregates offers a novel materials recycling approach - Kristina Smith reports
Here's a neat idea: take the muck from utilities trenches, treat it and reuse it, saving between 30-40% on the cost of landfill and backfill.This, in essence, is the theory behind
"There is great demand for a solution to waste streams which have previously gone to inert landfill and which have a high clay content," said Day Group director Adam Day.
"How do we take that muck and make it reusable? The solution is to produce an HBM." An HBM or hydraulically bound material, such as EcoFILL 40, is a mixture which hardens and sets by hydraulic action due to the inclusion of cementitious materials. Using graded clay-rich arisings from the utilities trenches dug around London, Day adds pulverised fuel ash (PFA), lime and cement to produce a cheaper and greener alternative to virgin type 1 backfill and sub-base.
"For us, it's all about trying to be green and being seen to be green," said Dereck Adams, contracts manager for
"The principle of soil stabilisation is commonly used in situ. This is taking that principle by transporting the material to a recycling centre, treating it and then taking it back," said Day. This is Day Aggregates' first foray into bound aggregates. The family run business was started by Adam Day's grandfather as a coal merchant but in the 1970s the power stations stopped using coal, so Day's father began to use rail to bring in limestone for road construction. Aggregates logistics is still a major part of the group's business.
In the past decade, Day Aggregates has started manufacturing recycled aggregates with 1m tonnes of the 3m tonnes the company handles being recycled. Adam Day works alongside his three brothers who hold various roles in the company including chief executive, with his father overseeing the changes and developments as chairman.
HBMs are not a new concept; the Romans used crushed stone, flint and tile tamped down onto a bed of ashes in the upper layers of their roads. But until the European standard governing the production of HBMs was finally incorporated into the
The advantage of EcoFILL 40 for Morrison is that it is produced to the British Standard and highways Agency specifications which means that there is no need for trials, as is the case with other alternative reinstatement materials.
"That's really important for us," said Adams.
"We are doing lots and lots of work for councils all across London. We cannot keep doing twoyear trials in different locations." Day has been producing EcoFILL 40 on a trial basis for a year with Morrison, working for
Day's new continuous mixing plant, designed and manufactured by
As well as re-using a waste material, this process also reduces lorry movements for the contractor and hence fuel bills and carbon emissions. The idea is that lorries bringing arisings into Day's works come out again with a load of type 1 equivalent backfill to be used in reinstatement.
There are some differences in working with a type 1 equivalent HBM compared to virgin type 1 material, said Day: "People have to look at an HBM as a new product; there are going to be some variations over an unbound material compared to a bound material." one point to note is that an HBM cannot be used in extreme weather conditions, that is temperatures below 3°C or very wet conditions.
Operatives must also be made aware that it should be handled in a similar way to concrete due to its cementitious binders. however it is compacted in the same way as virgin backfill.
Weather conditions aside, the only situation where a product such as EcoFILL 40 could not replace its virgin equivalent would be if stockpiles of the material were to be required, said Day: it must be used within 14 days and should not be stored where water can get to it.
The biggest challenge in producing the HBM is controlling the feed stock, said Day, which the firm tackles with a proven quality assurance (QA) system. When the muck comes in, it is assessed as to whether it is suitable for the HBM process or not. If there is too much clay contamination with no granular material at all it will leave the Greenwich site by barge to go to landfill. Adam Day said that around 70% of utility arisings can be recycled and reused.
Acceptable material is crushed and screened, with the base aggregate tested through the laboratories. From here the aggregate goes into the mixing plant.
The plant records the quantities by weight of each constituent added, with the final product subject to routine tests. "This plant gives us extreme accuracy and recordability of our mixes," said Day. "We can measure very precisely the amount of binders added into the mix." Day considered three different manufacturers before deciding on Rapid. "We felt that Rapid gave us the build, design and quality that we look for in our suppliers and the application of the health and safety aspects of the plant. They also had an understanding of the process we wanted to achieve, which is relatively new, and which required changes to the design." A major advantage which the Rapid plant, adapted from a mobile version known as the Rapidmix 400, had over its competition was the design of its the mixing chamber, known as the pugmill. Rapid's pugmill has been designed to make it easy to clean.
Configured with versatility in mind, Day's plant could be used to produce a number of different products from various waste streams.
In addition to the range of HBMs, the plant could process road planings to make cold mix asphalt, which Day may consider in the future.
Built around the firm's conveyor belt which carries material from the bank of the River Thames, over a footpath to the main part of the site, the plant has been modified so that it can swing round to discharge onto the main conveyor, for example if it is using higher grade base material to produce HBM for new construction, rather than discharging into the waiting trucks of the utilities contractors.
Day sees the plant's bread and butter as the utilities market, with the plant batching EcoFILL 40 every day. In addition to that, he hopes to bring in new build contracts. Day Group isn't the only firm that has spotted the opportunity in HBMs. O'Keefe Utilities set up a similar plant in Silvertown, east London in late 2009 which can process up to 100tonnes/hour of arisings for Laing O'Rourke working for EDF Energy, now UK Power Networks.
O'Keefe now supplies other contractors from its Silvertown plant and opened a second plant in Chatham, Kent earlier this year to supply HBMs and a whole range of recycled products to utilites and road contractors.
Director Ricky hemmings says that the firm will soon hit the 100,000tonne mark for HBM produced since october 2009 with its two plants.
While the reinstatement market seems a guaranteed winner - lower cost, lower carbon, less lorry movements - the new build market can be a tougher nut to crack, said Day. "The complex business of pavement design is changing to take advantage of hBMs, but it takes a long time to get through to designers and for them to take on the implications into designs." Despite these hurdles, both Day Group and O'Keefe have plans to expand this line of business. The drivers of cost and sustainability go hand-in-hand. "We only develop new products which we believe give an advantage," he said. "There has to be a cost reason for doing it. Every business is looking for low carbon because fuel costs money. If you can take out the requirement of a layer of asphalt within road construction, you are immediately taking out the cost of heat, therefore reducing carbon dioxide demand. It's a win-win situation."
Mixer
Day Aggregate's new continuous mixer can produce a lot of product: 300tonnes/hour. The heart of the plant is its pugmill mixer. Two sets of paddles on two shafts turn in opposite directions to provide forced action mixing of the constituents.
The static plant has been adapted from Rapid International's mobile version, the RapidMix 400. This model has been widely supplied in North America to perform tasks from stabilising soils on road construction jobs to making roller compacted concrete for damn construction.
Day's static machine is more versatile than its mobile cousin, with the ability to mix up to three aggregate materials and various cementitious material. The RapidMix 400 works with just one base material and one cementitious one.
Day's new machine, now installed at its Greenwich site in south London, has three shovel-fed aggregate hoppers, each with automatically controlled variable outputs, monitored by belt scale to accurately blend the right proportions of materials.
Going into the three hoppers to produce its HBM for utilities trench, reinstatement will be crushed and screened aggregate from trench arisings; a more precisely graded aggregate to help control the grade; and pulverised fuel ash (PFA). These materials fall onto a conveyor which carries them into the pugmill mixer. At the entry end of the pugmill, water and other liquid additives are added, followed by OPC and lime from two silos.
Once processed, the product is carried by a radial conveyor which can be moved to discharge either directly to trucks, into a stockpile or onto Day's ship-to-shore conveyor which carries material to the main aggregate stockpiles.
Rapid's novel cleaning system was one of its main selling points, said Day Group director Adam Day. The mixing operation sees a layer of base material build up on the wall of the chamber, which protects the walls from wear but also must be removed if it gets too thick or if a different grade or type of product is to be produced. Rapid's plan uses hydraulic cylinders to drop open the sides of the pugmill with the bottom of the pugmill constructed from a static conveyor which is only operated for cleaning.
Measurement of constituents by weight is a key requirement in order to allow Day to meet European standards. Rapid only developed this function recently, as its main market, North America, requires measurement by volume. Now that measurement by weight is available, Victor Pickering of Concrete Technology who represents Rapid International in the UK, expects more orders for its RapidMix 400 plant from Europe.