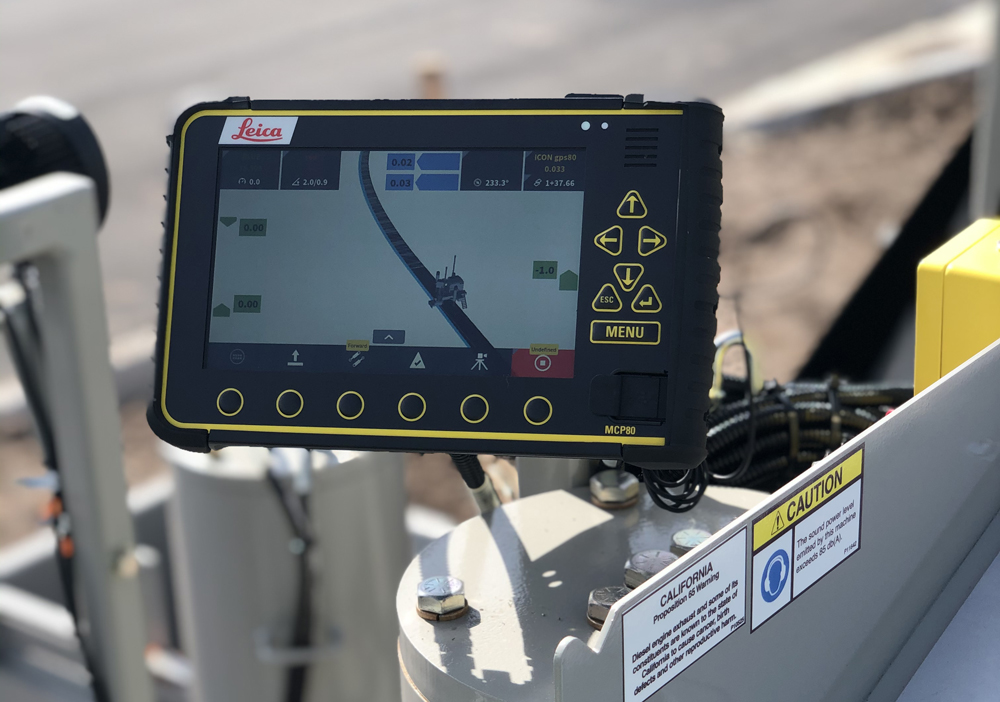
These systems for concrete slipforming are becoming more popular and help deal with business challenges such as labour shortages, competitive bidding, and future sustainability.
Elliot Jones, managing partner of 3D Concrete Solutions, has a different perspective, “I looked at it as training wheels. It kind of keeps us in the rails. I feel a lot better with having this control.”
The firm was already well established in the construction market in the earthmoving sector. And as the company had experienced difficulties with local companies carrying out concrete work, the firm saw this as an opportunity to establish its own specialist business. Diverging from the earthmoving business was a big move, however, as the company had no prior hand forming or slipforming experience.
From the beginning, Jones said that he wanted the concrete company to be the first in the region running a stringless slipform machine. As the company has worked with machine control on earthmoving equipment for 10 years Jones had seen green operators successfully trained on dozers or motor graders using 3D systems. He was confident that a slipform operator could be trained similarly and felt good about using 3D tools for stringless slipforming.
Jones and Rusty Grimes, president, visited the Power Curbers manufacturing facility and opted for a new 5700-D slipformer. The decision was made also to purchase a control system to go with the slipformer.
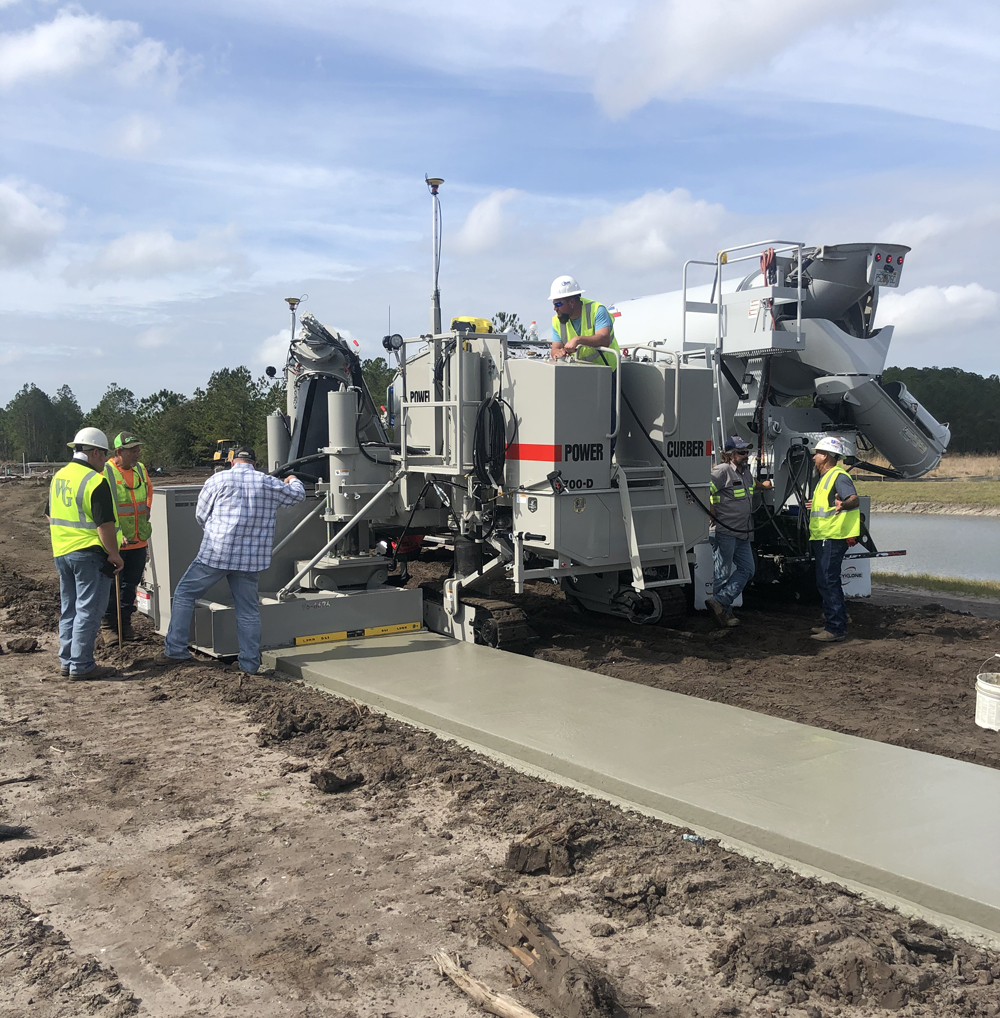
One of the primary reasons Jones insisted upon starting with 3D controls was avoiding stringline limitations. He stated, “you are saving at least a day on a small job, a half-day to set up and a half-day to break down or anywhere from two days or more for a larger job. You only have so many linear feet of pins, and you have to leapfrog them. That is your bottleneck.” However, with stringless controls, Jones pointed out, “your bottleneck isn’t how many pins; it becomes: control is here, total stations are here, we can keep leapfrogging those bad boys until the concrete plant shuts us down. There are no limits now.” Grimes continued, “it saves costs with the survey and guys putting out stringline and pins. We can roll in there, localise everything in an hour or two, and we are off and running. We’ve done as much as 4,000 linear feet or more, and that’s only because we ran out of mud.”
Not only is 3D Concrete Solutions seeing time and money savings, but the quality is superior. “They’ve verified vertical tolerances as small as 0.02”. Jones reported that “it’s better than stringline. The stringline gets manipulated by people on the jobsite. There is room for human error. If you follow the model, it is perfectly to the engineer’s plan.” After a number of completed jobs, Jones expressed that the 5700-D with Leica controls has been highly successful for quality and productivity, as well as proving popular with the paving crew.