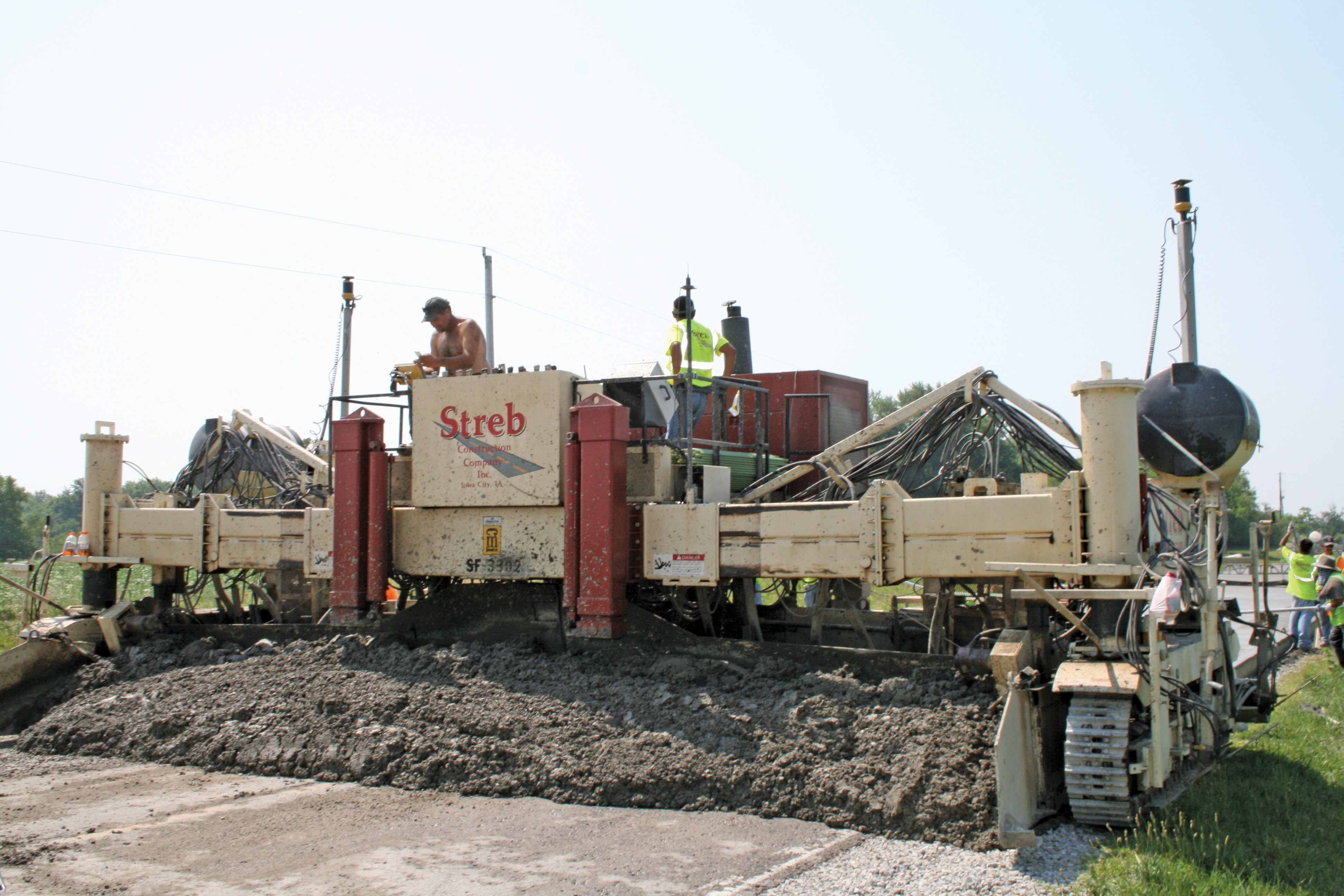
Upgrades to a slipform concrete paver built in 1999 allow it to use current technology
US firm Streb Construction has taken a novel approach to its paving fleet by upgrading a CMI paver built in 1999 to use modern machine control technology. The company bought the CMI SF3302 machine new and this piece of equipment had logged a high number of hours since its purchase. However the company realised that this proven piece of equipment could be made to operate more efficiently and productively, as well as more accurately, by dispensing with stringless controls and using new machine control systems instead. Steve Streb, vice president of Streb Construction, pointed out that stinglines can be vulnerable to on-site damage by vehicles and personnel and that the latest stringless systems avoid this problem and other potential errors.Streb Construction approached
Power Pavers was able to retrofit this machine because the SF3302 has a similar hydraulic circuit to the current SF1700 model. This allowed the firm to install the SF1700 control system and hydraulic components in parallel to the existing components on the SF3302. With the upgrade made, it was then capable of running the Topcon's GPS Paver System, which uses GPS and Topcon’s patented Lazer Zone designed to provide millimetre accurate control for concrete pavers. This package allows minute adjustments to be made to the thickness of the paving by the machine operator while the machine is running, a major benefit to county engineers who conduct depth checks. The system allows the machine operator to make fine incremental changes using the Topcon GX50 control box. Prior to GPS machine control on pavers, the operator or another worker would need to physically run a measure to the hub and adjust the string to measure the adjustment. The Topcon technology provides grade reference over the entire project and supplies vertical measurement. It is designed to pave transitions and even through horizontal and vertical curves, while the system can be simply switched off when not required.
Concrete utility drill
Ohio-based
The A-1 utility drill is available in two models - the A-1-24 UTL and the A-1-30 UTL. Both models are said to be powerful and compact, allowing them to be used productively for drilling in confined spaces. An array of special application and pattern kits are also available from Minnich depending on the specific job. The A-1-24 UTL has an operating weight of 34kg, and can reach a drill depth of 177mm, with a cut-out width of 609mm. The A-1-30 UTL features an operating weight of 36kg and can reach a drill depth of 254mm with a cut-out width of 762mm. Both units are available with an optional dust collection system.