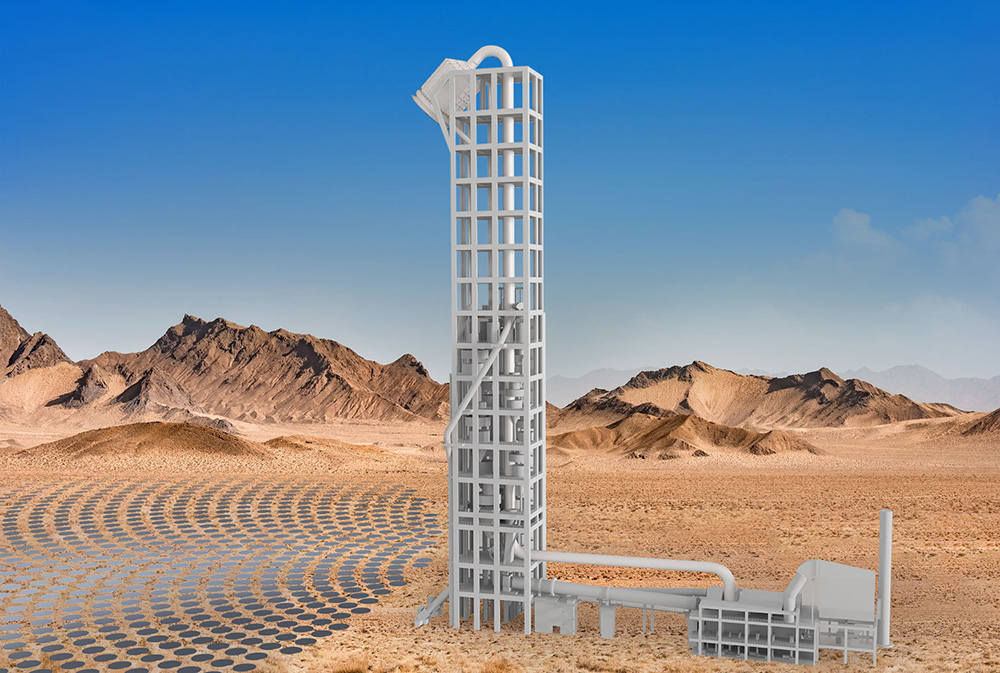
Key moves are being made in the battle to reduce the effects of climate change. The cement and concrete production sector, which is highly energy intensive, is seeing significant steps being made by some of the biggest players in the market.
CEMEX, Heidelberg Cement and LafargeHolcim have all announced developments that will help to lower CO2 emissions from this industry, which will assist in the battle to limit, and even halt, climate change. CEMEX and LafargeHolcim have pledged to become carbon neutral by 2050.
For its part, CEMEX says that it has invested over US$280 million since 2013 in technology to measure, control, and mitigate the gas and particle emissions in its operations. Through this continuous investment, the company has introduced international standards consistent with the world's strictest emissions regulations throughout its operations.
As a result, by the end of 2019, CEMEX achieved significant emissions reductions when measured against its 2005 baseline, the year when the company initiated its investments to improve its air quality. As of December 31st, 2019, CEMEX has reduced dust emissions by approximately 90%, sulphur emissions (SOx) by almost 60%, and nitrogen oxides (NOx) by close to 50%.
The company has signed an agreement with Carbon Clean to develop an efficient carbon capture solution by 2021. UK-headquartered Carbon Clean provides low-cost modular carbon dioxide capture and separation technology, aimed at developing a carbon capture solution for the cement industry that lies below the line of US$30/tonne cost of CO2 captured.
The partners say the aim is to develop technology that allows for the economically viable capture of CO2 emissions in the cement industry at industrial scale.
As part of the agreement, both companies will further develop and adapt Carbon Clean’s third generation modularised carbon capture technology for the cement industry. Carbon Clean uses an integrated modular system that works using rotating packed beds (RPBs) to intensify the carbon capture process. This technology could provide a significant reduction in both capital cost and equipment size compared to conventional capture technologies. The technology will be tested for the first time in the cement industry at a CEMEX facility by deploying an industrial-scale pilot during the first quarter of 2021. The partners say the technology has the capacity to capture up to 100,000tonnes of CO2/year at a cost lower than US$30/tonne of CO2 captured.
Furthermore, CEMEX says that it expects its European operations to reach the target of a 35% reduction in carbon emissions from cementitious materials by the end of 2020, a decade ahead of CEMEX´s 2030 global commitment outlined in its Climate Action strategy announced earlier in 2020. The company has launched its Vertua carbon-neutral concrete in the UK and France, which will be gradually available in other countries where CEMEX operates.
CEMEX and Synhelion meanwhile have announced that they developed a technology to decarbonise the cement manufacturing process based on solar energy. Synhelion, based in Switzerland, is a pioneer in sustainable solar fuels and process heat.
The radical approach is based on replacing the use of fossil fuels in cement plants with solar heat, and capturing 100% of the carbon emissions, to be used as feedstock for fuel production, enabling cement manufacturing to achieve net-zero level. This is made possible by the unprecedented temperature levels of solar heat provided by Synhelion’s technology and its pioneering process to turn CO2 into synthetic drop-in fuels, such as kerosene, diesel, and gasoline.
This solution offers a comprehensive approach to decarbonise the cement industry. Following the research collaboration completed in spring 2020, CEMEX and Synhelion will phase in implementation of the technology. A pilot installation will be incorporated into an existing CEMEX cement plant by the end of 2022 and extended to a fully solar-driven plant.
Meanwhile, HeidelbergCement has plans for the Brevik cement production facility in Norway through its Norecem subsidiary. Brevik is to implement an industrial-scale carbon capture and storage (CCS) project.
Giv Brantenberg, general manager HeidelbergCement Northern Europe and chairman of the board of Norcem, said: "We have been developing this project since the first desktop studies in 2005 and have interacted well over many years with the Norwegian authorities and our supportive partners."
The Norwegian Government shortlisted Brevik for an industrial-scale CO2 capture trial at the beginning of 2018. On 5th September 2019, a memorandum of understanding on the capture and storage of CO2 was signed by HeidelbergCement and the state-owned Norwegian energy Group Equinor. The Norwegian Government is expected to provide the bulk of the project funding.
The company has joined the SBTi “Business Ambition for 1.5°C,” and says it is signing the pledge with intermediate targets for 2030, validated by SBTi. It adds that this commitment builds on its green construction solutions including ECOPact concrete and Susteno circular cement.
For its 2030 goals, LafargeHolcim is further lowering its target for CO2 intensity in cement to 475kg net CO2/tonne of cementitious material. Europe is on track to become the first region to reach this net zero ambition, building on its €148.51 million investment roadmap launched in 2019. LafargeHolcim is also partnering with SBTi to develop a roadmap for aligning climate targets to a 1.5°C future in the cement sector.
By 2030, LafargeHolcim says it will: accelerate the use of low-carbon and carbon-neutral products such as ECOPact and Susteno; Recycle 100 million tons of waste and by products for energy and raw materials; Scale up the use of calcined clay and develop novel cements with new binders; Double waste-derived fuels in production to reach 37%; Reach 475kg net CO2/tonne of cementitious material; Operate its first net zero CO2 cement production facility.
In addition to its pledge to reduce scope 1 and scope 2 emissions, LafargeHolcim will expand its actions to include scope 3 emissions. The company says this will cut transportation and fuel-related emissions by 20%.
LafargeHolcim adds that it will increase the use of recycled materials in its products and processes while recovering materials at the end of their life cycle. In 2019, the company recycled 48 million tonnes of waste.
The company says it will develop and deploy advanced technologies, preparing the next step of its net zero journey. This includes piloting over 20 Carbon Capture Usage and Storage (CCUS) projects across Europe and North America.
In addition, Canadian clean technology company CarbonCure has announced an investment co-led by Amazon and Breakthrough Energy Ventures (BEV) will be used to tackle the carbon footprint of concrete.
CarbonCure is to use the investment to accelerate its product roadmap and geographical expansion in a bid to remove 500 million tonnes of CO2/year from the concrete industry by 2030. The investment is expected to help Amazon and other companies meet The Climate Pledge, a commitment to net zero carbon by 2040.
Other companies involved in the investment include Microsoft, BDC Capital, 2150, Thistledown Capital, Taronga Ventures and GreenSoil Investments.
Blue Planet has developed a carbon capture and utilisation system to permanently remove carbon dioxide that it says is economically viable and can be deployed at Gigaton (GT) scale.
In strength, performance and cost, Blue Planet claims that its CO2-sequestered aggregate is equivalent to that of standard quarried aggregates.
The startup says it will capture carbon dioxide emissions from bioenergy, natural gas and coal-fired power plants, steel mills, cement plants and refineries, as well as directly from the atmosphere. The process converts captured CO2 to carbonate for mineralisation as a synthetic limestone (CaCO3).
The synthetic limestone is claimed to be able to replace extracted limestone in concrete, permanently sequestering the captured CO2.
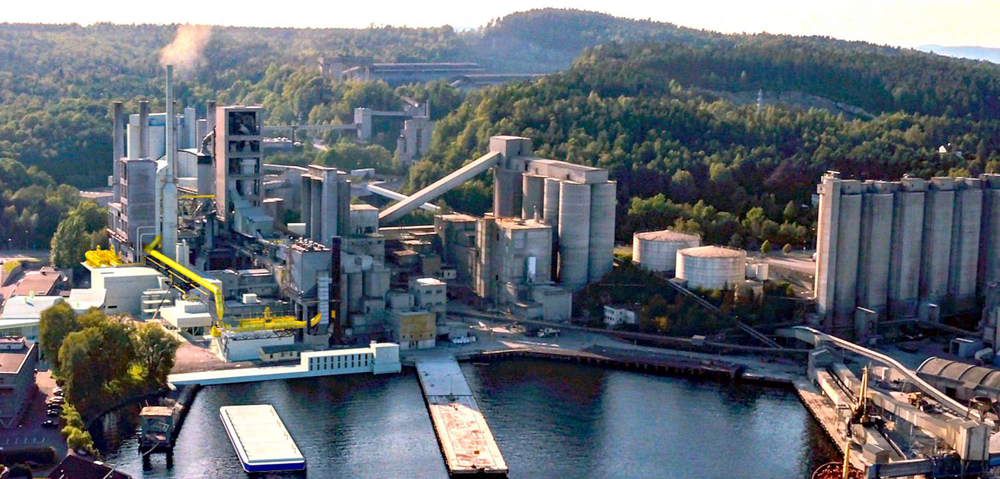
Blue Planet says the rock market represents one of the largest potential sinks for CO2 at over 50 GT every year, making Blue Planet's solution to reducing global carbon levels scalable and economically viable.
The company's proprietary process creates synthetic limestone sand and gravel that can be used to make carbon-neutral and carbon- negative concrete, with the same structural integrity of conventional concrete.
By offsetting the carbon footprint of the cement in concrete, Blue Planet says its aggregate compensates for the cement component's carbon footprint, making the concrete a net carbon storage sink. The process also creates upcycled concrete aggregate as a by-product, reducing the need for further extraction processes.
Blue Planet says that most carbon reduction schemes are not permanent and instead allow the captured carbon dioxide to re-enter the atmosphere at some point. The production and distribution of synthetic aggregate for concrete is said to make the operations profitable, and the plants can be financed, owned and operated without subsidies.
Blue Planet's first plant is being constructed in Pittsburgh, California, adjacent to a natural gas-fired power plant and the Sacramento Delta, for barged material transport of raw materials and finished goods. Blue Planet concrete has already been incorporated at Terminal 1 at San Francisco International Airport (SFO), which the company says establishes a model for cost-neutral public procurement of low carbon building materials for carbon mitigation.