New developments in concrete paving will increase working efficiency for contractors - Mike Woof writes
The concrete paving market is a fiercely competitive segment of the off-highway construction machinery business. Although there are only a few key players in this niche market, the firms are constantly developing new systems, equipment and methods in a bid to help improve working efficiencies for contractors working in the sector. It is of note that the majority of the key players in the concrete pavin
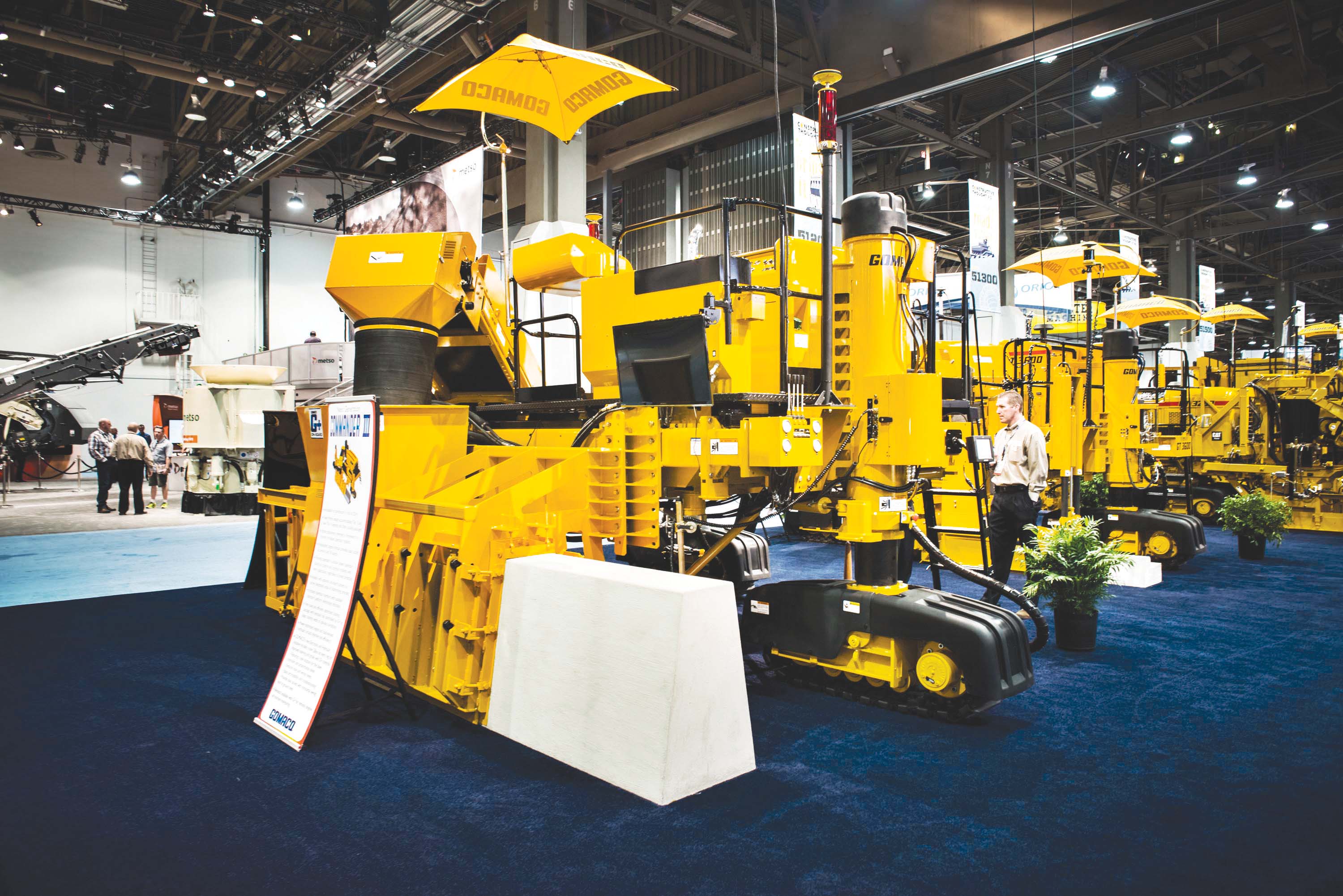
GOMACO continues to widen the range of capabilities for its highly successful and versatile Commander III paver
New developments in concrete paving will increase working efficiency for contractors - Mike Woof writes
The concrete paving market is a fiercely competitive segment of the off-highway construction machinery business. Although there are only a few key players in this niche market, the firms are constantly developing new systems, equipment and methods in a bid to help improve working efficiencies for contractors working in the sector. It is of note that the majority of the key players in the concrete paving equipment market are based in the US, with German firm2395 Wirtgen being the only exception. And while there have been various attempts by Chinese manufacturers to build concrete slipforming equipment, these have not been sold in numbers or used outside of the country.
218 Gomaco is one of the leaders in the concrete paving equipment market and its Commander III slipform paver is one of the firm’s most successful and versatile products. The latest developments to the Commander III further extend the range of capabilities for the machine, as well as allowing the unit to meet the latest emissions requirements. The machine is now being offered with power from a Tier 4 compliant engine, as well as the firm’s new G+ control system.
As part of its installation, the engine has been turned by 180° within the chassis in comparison to the earlier model, which improves airflow and reduces the cooling requirements of the diesel. As a result, the machine now features a smaller fan than before and this lowers the noise generated when the Commander III is in operation. Meanwhile having the latest generation diesel has also reduced the machine’s fuel consumption, aided by improvements to the hydraulics. With the engine turned around in the frame, service access has been improved along with operator visibility.
In addition, the operator station has been improved with the addition of vibration damping to a control console that pivots and can be moved as required to maximise visibility in a range of different types of job. An onboard camera can be mounted anywhere on the machine and will provide a live display on the G+ screen of functions that would otherwise be out of sight. Improved steering and grade control accuracy is achieved using the G+ system as GBox units are fitted to each leg.
The Commander III is being offered in three and four track versions with the former being a more versatile machine aimed at kerb and gutter slipforming duties and able to pave widths of up to 3.66m. The four track machine is for more standard slipforming duties and can pave widths up to 6.1m.
Another key development for Gomaco is the phased introduction of machine control technology from specialist firm2122 Trimble as a customer option. Companies can now select Trimble stringless 3D PCS900 Paving Control System, which uses field-proven Trimble total stations, on-machine positioning sensors and office software. This is a major development as Gomaco has long offered machine control technology from 265 Leica Geosystems on its equipment and more recently offered 342 Topcon systems as an option. The Trimble package means that contractors can pave accurately and consistently, while boosting productivity.
The Trimble PCS900 Paving Control System is fully integrated into the Gomaco paver and runs from a 3D model, allowing the operator to control grade and slope to the plan with a high degree of accuracy. The control system offers automatic steering and control of the pan, ensuring that the paver remains accurately on track as well as maintaining the design specifications for grade and slope. A key feature of the PCS900 Paving Control System and SPS930 Universal total Station is that it allows the machine to work continuously and transition from one total station to the next, without the operator having to reset the equipment.
Meanwhile225 Guntert & Zimmerman is addressing the needs of contractors looking to carry out paving within tight working environments in applications such as having live traffic running in lanes adjacent to the site. A development targeted at this need for paving at full width in restricted space applications is the firm’s optional Tight Trackline Paving Package, now being offered for models including the S600. The system allows the pavers to operate at full width, with just 300mm of companion lane trackline available next to a temporary median barrier or active lane of traffic.
The G&Z TightTrack system is also offered with or without a dowel bar inserter (DBI) attachment. When set up in the TightTrack configuration, the paver will not extend beyond the top of a temporary barrier. The firm says that this development now allows a mid-large size paver to be used for a narrow profile application. As a result, the firm says that contractors have more options when operating in minimal clearance trackline paving conditions. This means firms can maintain optimum concrete smoothness as well as full width paving, when pouring in narrow profile duties.
The firm offers an array of features for the TightTrack configuration including a tractor centre module, kit hangers and end bolsters. These maximise versatility and allow the paver to be configured for a much wider array of paving duties.
Another major development from Guntert & Zimmerman is the material placer, currently being developed in prototype form. The new model is more compact in design than Guntert & Zimmerman’s current placer spreader, which is designed for use in much bigger slipforming applications, such as airport paving. This new model is intended to help boost productivity in duties including highway paving, where working space may be very limited and contractors face challenges in delivering concrete shipments by truck.
Guntert & Zimmerman opted to start the development programme following a number of requests from its customers. The company said that several contractors had bought old CMI wheeled material placers and refurbished them. However Guntert & Zimmerman realised an entirely new machine based around a similar concept would offer various benefits. The four wheel drive MP550 is powered by a178 Caterpillar diesel delivering 206kW and which meets Tier 4 Final emissions requirements.
The model is being developed primarily for the North American market, where contractors have more of a focus on productivity rates, although Guntert & Zimmerman recognises that the MP550 could also appeal to an international market. The 7.06m3 capacity hopper of the machine is designed so that it can match the varying dump characteristics of different tipper trucks, featuring a rubber seal to minimise material spillage. The machine features four wheel steer and crab steer to maximise manoeuvrability while the firm has maximised access to the conveyors for cleaning and servicing.
Other new developments from the company included the fitting of its sophisticated EGON IntelliMatics system to the paver range, and updates to the TC1500 Texture Cure Machine. The EGON package uses telematics and allows performance and health monitoring of the engine, electrical system and hydraulics. This means that software patches or adjustments can be controlled remotely while a user can also address service issues and catch problems early on. Meanwhile the upgrades to the TC1500 include new relocatable jacking columns, and a redesigned cure spray hood with a quick-width change system.
Wirtgen continues to broaden the range of concrete pavers it offers in the North American market, with the company adding the SP84i to its line-up. The machine is said to be highly manoeuvrable as it has four steerable crawler tracks and this allows it to turn in tight space constraints despite its size. The machine has its mould fitted between the crawler tracks and like other models in the Wirtgen range, features a modular design that allows it to be tailored to the needs of a contractor or application. Power comes from a diesel delivering 180kW and the machine can be used with either electric or hydraulic vibration. A smooth slope system is offered, which helps maximise paving precision and lower response times while as with other Wirtgen pavers, the SP 84i features the firm’s WI-Control system. The sophisticated telematics package allows customers to link the machine to fleet management systems, improving servicing and utilisation and reducing the risk of costly downtime. Meanwhile the onboard machine management technology helps optimise performance, while reducing engine noise and fuel consumption. The load-sensing system adjusts the power output to the needs of the job in hand.
The concrete paving market is a fiercely competitive segment of the off-highway construction machinery business. Although there are only a few key players in this niche market, the firms are constantly developing new systems, equipment and methods in a bid to help improve working efficiencies for contractors working in the sector. It is of note that the majority of the key players in the concrete paving equipment market are based in the US, with German firm
As part of its installation, the engine has been turned by 180° within the chassis in comparison to the earlier model, which improves airflow and reduces the cooling requirements of the diesel. As a result, the machine now features a smaller fan than before and this lowers the noise generated when the Commander III is in operation. Meanwhile having the latest generation diesel has also reduced the machine’s fuel consumption, aided by improvements to the hydraulics. With the engine turned around in the frame, service access has been improved along with operator visibility.
In addition, the operator station has been improved with the addition of vibration damping to a control console that pivots and can be moved as required to maximise visibility in a range of different types of job. An onboard camera can be mounted anywhere on the machine and will provide a live display on the G+ screen of functions that would otherwise be out of sight. Improved steering and grade control accuracy is achieved using the G+ system as GBox units are fitted to each leg.
The Commander III is being offered in three and four track versions with the former being a more versatile machine aimed at kerb and gutter slipforming duties and able to pave widths of up to 3.66m. The four track machine is for more standard slipforming duties and can pave widths up to 6.1m.
Another key development for Gomaco is the phased introduction of machine control technology from specialist firm
The Trimble PCS900 Paving Control System is fully integrated into the Gomaco paver and runs from a 3D model, allowing the operator to control grade and slope to the plan with a high degree of accuracy. The control system offers automatic steering and control of the pan, ensuring that the paver remains accurately on track as well as maintaining the design specifications for grade and slope. A key feature of the PCS900 Paving Control System and SPS930 Universal total Station is that it allows the machine to work continuously and transition from one total station to the next, without the operator having to reset the equipment.
Meanwhile
The G&Z TightTrack system is also offered with or without a dowel bar inserter (DBI) attachment. When set up in the TightTrack configuration, the paver will not extend beyond the top of a temporary barrier. The firm says that this development now allows a mid-large size paver to be used for a narrow profile application. As a result, the firm says that contractors have more options when operating in minimal clearance trackline paving conditions. This means firms can maintain optimum concrete smoothness as well as full width paving, when pouring in narrow profile duties.
The firm offers an array of features for the TightTrack configuration including a tractor centre module, kit hangers and end bolsters. These maximise versatility and allow the paver to be configured for a much wider array of paving duties.
Another major development from Guntert & Zimmerman is the material placer, currently being developed in prototype form. The new model is more compact in design than Guntert & Zimmerman’s current placer spreader, which is designed for use in much bigger slipforming applications, such as airport paving. This new model is intended to help boost productivity in duties including highway paving, where working space may be very limited and contractors face challenges in delivering concrete shipments by truck.
Guntert & Zimmerman opted to start the development programme following a number of requests from its customers. The company said that several contractors had bought old CMI wheeled material placers and refurbished them. However Guntert & Zimmerman realised an entirely new machine based around a similar concept would offer various benefits. The four wheel drive MP550 is powered by a
The model is being developed primarily for the North American market, where contractors have more of a focus on productivity rates, although Guntert & Zimmerman recognises that the MP550 could also appeal to an international market. The 7.06m3 capacity hopper of the machine is designed so that it can match the varying dump characteristics of different tipper trucks, featuring a rubber seal to minimise material spillage. The machine features four wheel steer and crab steer to maximise manoeuvrability while the firm has maximised access to the conveyors for cleaning and servicing.
Other new developments from the company included the fitting of its sophisticated EGON IntelliMatics system to the paver range, and updates to the TC1500 Texture Cure Machine. The EGON package uses telematics and allows performance and health monitoring of the engine, electrical system and hydraulics. This means that software patches or adjustments can be controlled remotely while a user can also address service issues and catch problems early on. Meanwhile the upgrades to the TC1500 include new relocatable jacking columns, and a redesigned cure spray hood with a quick-width change system.
Wirtgen continues to broaden the range of concrete pavers it offers in the North American market, with the company adding the SP84i to its line-up. The machine is said to be highly manoeuvrable as it has four steerable crawler tracks and this allows it to turn in tight space constraints despite its size. The machine has its mould fitted between the crawler tracks and like other models in the Wirtgen range, features a modular design that allows it to be tailored to the needs of a contractor or application. Power comes from a diesel delivering 180kW and the machine can be used with either electric or hydraulic vibration. A smooth slope system is offered, which helps maximise paving precision and lower response times while as with other Wirtgen pavers, the SP 84i features the firm’s WI-Control system. The sophisticated telematics package allows customers to link the machine to fleet management systems, improving servicing and utilisation and reducing the risk of costly downtime. Meanwhile the onboard machine management technology helps optimise performance, while reducing engine noise and fuel consumption. The load-sensing system adjusts the power output to the needs of the job in hand.