Soft engineering techniques, used to prevent soil erosion and stabilise steep cuts and embankments, have allowed engineers to successfully widen the M1 motorway in the UK. Over the 50km length of the work (25km northbound, 25km southbound) on a busy section of the motorway near the city of Nottingham, a total of 48km of slopes had to be modified, split roughly between cutting and embankment. The UK Highways Agency requirements for the work meant that wholesale widening of the corridor was not possible: the
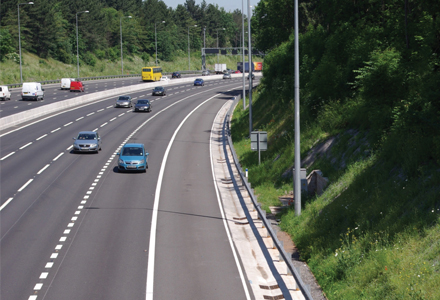
Soft engineering techniques, used to prevent soil erosion and stabilise steep cuts and embankments, have allowed engineers to successfully widen the M1 motorway in the UK.
Over the 50km length of the work (25km northbound, 25km southbound) on a busy section of the motorway near the city of Nottingham, a total of 48km of slopes had to be modified, split roughly between cutting and embankment.
The1441 UK Highways Agency requirements for the work meant that wholesale widening of the corridor was not possible: the road's overall footprint could not be extended. Land clearance within it had to be minimised and balanced relative to the needs of the agreed environmental impact statement [EIS].
This included building within the constraints of a no-contraflow construction and limited width of widening; providing a solution that would maximise replanting; ensuring topsoil retention and a vegetated finish on steep slopes; and minimising waste and offsite disposal/importation of materials.
Consulting engineers Gifford WSP was designer for MVM, a joint venture partnership between Morgan Est, Vinci and Sir Robert McAlpine. The team developed a hierarchy of solutions to allow maximum utilisation of the existing motorway corridor, including the re-profiling of cuts and embankments to accommodate the required, eight-lane plus hard-shoulder motorway.
Construction solutions were applied based on the geometry at each location: some locations were identified as being of higher environmental sensitivity, and consequently land clearance had to be kept to an absolute minimum.
At each location, solutions were cost assessed and an appropriate treatment adopted. Target cost solutions were tested against EIS criteria, with a degree of flexibility allowed to achieve an overall balance.
In cuttings, the sequence was general earthworks: low-height gabion retaining structures and then soil nailing/geotextile erosion protection matting.
On embankments, the sequence involved general earthworks, steep earthworks using selected, high-strength granular fill and topsoil with erosion protection materials. Finally, there were hard retaining structures.
Andy Rose, technical director geotechnics at Gifford, explained: "Close interaction between highways/structures/environmental specialists and geotechnical designers was essential to provide the optimum solutions and, at an early stage, specialist geotechnical suppliers were engaged.
"When extending a cut, removal of the toe of the slope generally means that the overall slope becomes less stable. The steepened slope may be stable in the short-term but it will require strengthening to ensure long-term stability." Rapid establishment of vegetative cover to the newly formed slopes was also a priority for the construction team." Geotechnical and erosion control advice on a significant proportion of the works was provided by specialists1589 Maccaferri.
Initially, its gabion retaining structures and rock-fall containment netting were supplied but, as work progressed, a wider range of systems from the company were introduced including soil retention, erosion protection and other 'soft' slope stabilisation systems.
A steepened slope solution using soft measures is approximately one-sixth the cost of a traditional, 'hard' retaining wall solution such as masonry or in situ concrete walls, and offers far greater flexibility to adapt to site conditions, so the designers were keen to exploit the benefits of these measures.
The Maccaferri erosion protection systems, Enkamat and Biomac, were used to overlay exposed cut faces of typically of 2-3m height and in places up to 6m high. Some 38,000m² was installed in combination with over 7,000 soil nails, bored into the retained slope to strengthen it and anchor the material in place.
Enkamat is a non-woven geotextile matting of thick polyamide filaments which is designed to be secured over the vulnerable slope face to prevent surface erosion by run-off. Over 90% of the volume of the mat is voids and is therefore available for soil filling, maximising the potential for establishing vegetation on the slope.
Biomac is a biodegradable erosion protection blanket made from natural fibres such as coir or a coir-straw mix. When secured to the soil slope, it offers immediate erosion protection to the soil during the establishment phase of seeding and planting.
The further problem of how to retain topsoil on the steepened slopes was addressed with the application of an expanding cellular soil containment system, also from Maccaferri, called Armater, which creates a continuous grid of 100mm deep pockets that holds topsoil. When seeded, root growth binds the soil layer together and to the underlying materials, preventing it from slumping down the steeply sloping site.
On the steepened embankment slopes, at certain locations up to 8m in height with the steepened and widened sections representing between 30-50% of this height, some 35,000m² of topsoil required such assisted retention: over the project the volume of total excavation exceeded 320,000m².
Over the 50km length of the work (25km northbound, 25km southbound) on a busy section of the motorway near the city of Nottingham, a total of 48km of slopes had to be modified, split roughly between cutting and embankment.
The
This included building within the constraints of a no-contraflow construction and limited width of widening; providing a solution that would maximise replanting; ensuring topsoil retention and a vegetated finish on steep slopes; and minimising waste and offsite disposal/importation of materials.
Consulting engineers Gifford WSP was designer for MVM, a joint venture partnership between Morgan Est, Vinci and Sir Robert McAlpine. The team developed a hierarchy of solutions to allow maximum utilisation of the existing motorway corridor, including the re-profiling of cuts and embankments to accommodate the required, eight-lane plus hard-shoulder motorway.
Construction solutions were applied based on the geometry at each location: some locations were identified as being of higher environmental sensitivity, and consequently land clearance had to be kept to an absolute minimum.
At each location, solutions were cost assessed and an appropriate treatment adopted. Target cost solutions were tested against EIS criteria, with a degree of flexibility allowed to achieve an overall balance.
In cuttings, the sequence was general earthworks: low-height gabion retaining structures and then soil nailing/geotextile erosion protection matting.
On embankments, the sequence involved general earthworks, steep earthworks using selected, high-strength granular fill and topsoil with erosion protection materials. Finally, there were hard retaining structures.
Andy Rose, technical director geotechnics at Gifford, explained: "Close interaction between highways/structures/environmental specialists and geotechnical designers was essential to provide the optimum solutions and, at an early stage, specialist geotechnical suppliers were engaged.
"When extending a cut, removal of the toe of the slope generally means that the overall slope becomes less stable. The steepened slope may be stable in the short-term but it will require strengthening to ensure long-term stability." Rapid establishment of vegetative cover to the newly formed slopes was also a priority for the construction team." Geotechnical and erosion control advice on a significant proportion of the works was provided by specialists
Initially, its gabion retaining structures and rock-fall containment netting were supplied but, as work progressed, a wider range of systems from the company were introduced including soil retention, erosion protection and other 'soft' slope stabilisation systems.
A steepened slope solution using soft measures is approximately one-sixth the cost of a traditional, 'hard' retaining wall solution such as masonry or in situ concrete walls, and offers far greater flexibility to adapt to site conditions, so the designers were keen to exploit the benefits of these measures.
The Maccaferri erosion protection systems, Enkamat and Biomac, were used to overlay exposed cut faces of typically of 2-3m height and in places up to 6m high. Some 38,000m² was installed in combination with over 7,000 soil nails, bored into the retained slope to strengthen it and anchor the material in place.
Enkamat is a non-woven geotextile matting of thick polyamide filaments which is designed to be secured over the vulnerable slope face to prevent surface erosion by run-off. Over 90% of the volume of the mat is voids and is therefore available for soil filling, maximising the potential for establishing vegetation on the slope.
Biomac is a biodegradable erosion protection blanket made from natural fibres such as coir or a coir-straw mix. When secured to the soil slope, it offers immediate erosion protection to the soil during the establishment phase of seeding and planting.
The further problem of how to retain topsoil on the steepened slopes was addressed with the application of an expanding cellular soil containment system, also from Maccaferri, called Armater, which creates a continuous grid of 100mm deep pockets that holds topsoil. When seeded, root growth binds the soil layer together and to the underlying materials, preventing it from slumping down the steeply sloping site.
On the steepened embankment slopes, at certain locations up to 8m in height with the steepened and widened sections representing between 30-50% of this height, some 35,000m² of topsoil required such assisted retention: over the project the volume of total excavation exceeded 320,000m².