New machines from Dynapac have played an important role in tackling a stretch of Canadian highway with safety issues. The machines have been used to meet experimental compaction standards specified by highway engineers, so as to withstand Canada's harsh winter conditions. Canadian contractors InterCite Construction and Pavex of St Felicien have used the new Dynapac machines for work on upgrading Route 175, one of Canada's most dangerous highways, located in the Province of Quebec. Route 175 is a 174km long
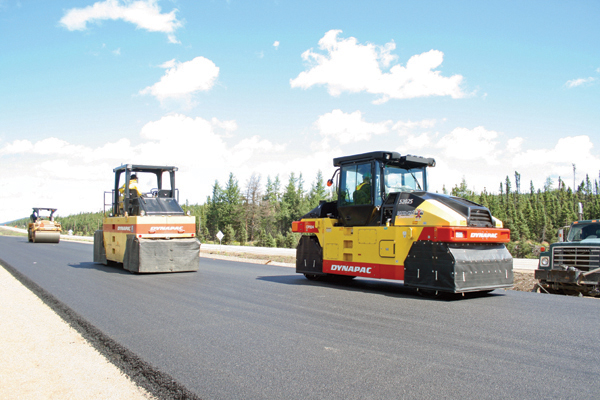
Dynapac compactors have played a part in upgrading a key Canadian route that suffers safety issues
New machines from 206 Dynapac have played an important role in tackling a stretch of Canadian highway with safety issues. The machines have been used to meet experimental compaction standards specified by highway engineers, so as to withstand Canada's harsh winter conditions. Canadian contractors 2830 InterCite Construction and Pavex of St Felicien have used the new Dynapac machines for work on upgrading Route 175, one of Canada's most dangerous highways, located in the Province of Quebec. Route 175 is a 174km long highway through Canada's Parc des Laurentides National Park and links Quebec City and the northern city of Saguenay (Chicoutimi). The highway is used by a wide variety of vehicles including heavy logging trucks and large commercial vehciles as well as local and tourist traffic. However, the route is one of Canada's most dangerous due to often tough weather conditions as well as frequent collisions between vehicles and wildlife (moose in particular). Built originally with a single lane in each direction, the road had progressively been partially built to highway standards but with many sections still single lane or with an overtaking third lane. Following lengthy negotiations between the Quebec and Federal Governments funding of almost US$637 million to upgrade the highway was budgeted in 2002. In 2005 work started on upgrading to a four lane, dual carriageway along the full length of the highway with a completion date of 2012. With the first four-lane section completed in 2007, some 67km had been completed by 2008 with a further 16km in 2009.
However highway engineers are looking for solutions to extend the asphalt lifespan and cope with Canada's harsh winters. Snowfall can be up to 3m deep and a frost penetration of more than 1m can be experienced, while additional asphalt damage is also caused by the country's unregulated lorry load axle weights. As a result the engineers are experimenting with different thicknesses of asphalt, layers and compaction densities. The highway is being generally built with at least a metre high embankment to reduce frost penetration. Highway engineers have also specified low mix asphalt and low compaction density to absorb any soil/asphalt movement together with a bottom, third anti-cracking asphalt layer. It is anticipated that these will offer flexibility in the pavement to prevent possible cracking during the harsh winter months.
Contracts are generally broken down into 5-10km segments with the two contractors, Pavex of St Felecien and Intercite Construction working at km143 and km154 respectively, using purpose-ordered Dynapac compaction equipment for the brief summer month's construction period. Intercite Construction is currently working on a 10km segment from km154 and has, since 2005, completed almost 70km of highway along Route 175 close to Chicoutimi using its large fleet of Dynapac rollers. For its latest contract, Inter Cite is laying a specified 55-66mm thick ESG5 asphalt mix, featuring a 0.5mm aggregate mixed with sand and bitumen, as an anti-cracking (fissure) layer. This is topped by an ESG14 mix to depths of between 6 -80mm as specified with a 50mm top ESG10 wearing course. All the asphalt layers are compacted to meet a minimum of 93% compaction density and a maximum of 98% depending on the section of road. The firm added a new CP224 pneumatic tyred compactor to work alongside its existing CP221 roller and the new machine's improved cab and performance was apparent over the earlier mode.
Meanwwhile Pavex of St Felicien took delivery of a Dynapac CC524HF from dealer JA Larue, for its segment at km143. This new machine was put to work alongside a Dynapac CC522HF compaction roller and a rubber tyred CP221. Using the CC522HF with four passes behind the paver, the CP221 roller follows with one or two passes to seal the asphalt. The new CC524HF roller then completes the cycle with a single vibratory pass over the 500m length for the first asphalt layer. For the top layer the roller provides a static mode pass.
However highway engineers are looking for solutions to extend the asphalt lifespan and cope with Canada's harsh winters. Snowfall can be up to 3m deep and a frost penetration of more than 1m can be experienced, while additional asphalt damage is also caused by the country's unregulated lorry load axle weights. As a result the engineers are experimenting with different thicknesses of asphalt, layers and compaction densities. The highway is being generally built with at least a metre high embankment to reduce frost penetration. Highway engineers have also specified low mix asphalt and low compaction density to absorb any soil/asphalt movement together with a bottom, third anti-cracking asphalt layer. It is anticipated that these will offer flexibility in the pavement to prevent possible cracking during the harsh winter months.
Contracts are generally broken down into 5-10km segments with the two contractors, Pavex of St Felecien and Intercite Construction working at km143 and km154 respectively, using purpose-ordered Dynapac compaction equipment for the brief summer month's construction period. Intercite Construction is currently working on a 10km segment from km154 and has, since 2005, completed almost 70km of highway along Route 175 close to Chicoutimi using its large fleet of Dynapac rollers. For its latest contract, Inter Cite is laying a specified 55-66mm thick ESG5 asphalt mix, featuring a 0.5mm aggregate mixed with sand and bitumen, as an anti-cracking (fissure) layer. This is topped by an ESG14 mix to depths of between 6 -80mm as specified with a 50mm top ESG10 wearing course. All the asphalt layers are compacted to meet a minimum of 93% compaction density and a maximum of 98% depending on the section of road. The firm added a new CP224 pneumatic tyred compactor to work alongside its existing CP221 roller and the new machine's improved cab and performance was apparent over the earlier mode.
Meanwwhile Pavex of St Felicien took delivery of a Dynapac CC524HF from dealer JA Larue, for its segment at km143. This new machine was put to work alongside a Dynapac CC522HF compaction roller and a rubber tyred CP221. Using the CC522HF with four passes behind the paver, the CP221 roller follows with one or two passes to seal the asphalt. The new CC524HF roller then completes the cycle with a single vibratory pass over the 500m length for the first asphalt layer. For the top layer the roller provides a static mode pass.