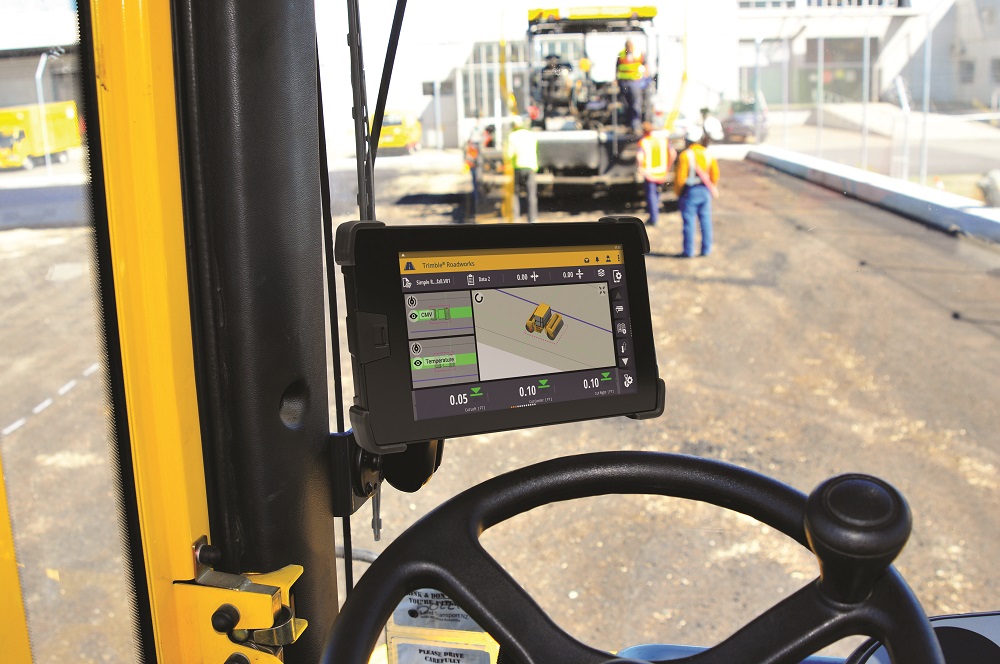
The latest compaction package from Trimble helps to deliver a quality surface more quickly and efficiently. According to the firm, the system allows operators to accurately control the compaction process, while reducing unnecessary passes that can result in over-compaction.
The Trimble Roadworks Paving Control Platform for Asphalt Compactors is an accurate, 3D paving control system designed to improve the speed, accuracy and ease of asphalt compaction. The system can use single GNSS dual GNSS and also Total-station technology.
The system can be used to monitor pass counts only or pass counts plus temperature. Operators are able to transfer Intelligent Compaction data wirelessly from the machine to the office with the Trimble SNM941 Connected Site Gateway. The system can be used to collect compatible data files that are ready to import into a Veta intelligent construction project.
The Android-based software features the same user interface as existing Roadworks applications. Customers can use one workflow from the initial design model to the last pass of the compactor and can monitor and analyse compaction efficiency from the office.
The system displays real-time temperature mapping, compaction progress, pass counts and optional display and recording of the compacted asphalt stiffness. It ensures that the surface is compacted to the specified stiffness target and users can monitor site volumes simultaneously and in real time.
The system ensures optimal compaction for the target temperature range, reducing rework and material waste with real-time temperature map monitoring. This allows the user to achieve optimum durability, stability and load-bearing capacity. Supervisors and quality managers can monitor compaction activities to track and report progress, while the real-time compaction data helps to improve layer management.
A colour display allows the operator to view compaction progress, pass counts and mat temperature information so that users can roll a more uniform surface and increase efficiency. The system also tracks compaction measurement values (CMV) over the entire area, while reducing reworking, operator hours and cutting machine maintenance costs.
Efficient communications and data transfer can be achieved using the Trimble WorksManager Software and Trimble WorksOS Software packages.
Users can transfer 3D designs wirelessly from the office to the machine, while productivity and compaction data collected from the machine can automatically sync back to the office for analysis. The wireless data share also allows each operator to see the work being done by others in real-time to achieve better surface quality over the jobsite, while saving time and fuel for each contract.