The Kaliningrad motorway Primorsk Ring is one of the prestige projects under construction within the scope of infrastructure improvements in the Russian exclave. With a total length of around 180kms, of which 81kms are motorway, the ring road will encircle the 500,000 residents of Kaliningrad city in a broad arc around the Samland peninsula.
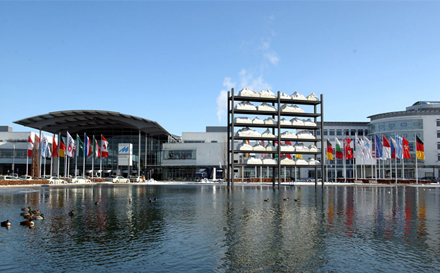
The Kaliningrad motorway Primorsk Ring is one of the prestige projects under construction within the scope of infrastructure improvements in the Russian exclave. With a total length of around 180kms, of which 81kms are motorway, the ring road will encircle the 500,000 residents of Kaliningrad city in a broad arc around the Samland peninsula.
Completion of the US$32.55 million (1bn RUB) project is scheduled for 2015 and should allow comfortable travel for residents, tourists and football fans travelling to the 20181556 World Cup football venue in Kaliningrad. Four sections have already been opened to traffic; a fifth section is currently under construction.
For ZAO VAD, the construction consortium which is performing the work, precise and error-free construction of the road has been a top priority.
To accomplish this, the right material composition, material temperature, smooth paving process and then a precise compaction of the asphalt are necessary.
"During road construction, it is very important that work be performed exactly and painstakingly from the first to the last work step. Compaction of the paved material is one aspect that plays a key part for a successful result", said Ronald Brinks of ZAO VAD. For this purpose, ZAO VAD, in cooperation with OOO SMD Balt Avtomatika, installed the1228 MOBA Compaction Assistant system (MCA-2000) on a roller.
"The requirement in this project was to make the compaction more controllable as, in the past, this was based solely on the experience of the worker and there was no continuous monitoring of the results. Moreover, it was to be possible to create a quality certificate for the performed compaction work. That is why we decided to use the MCA-2000", said Yuri Dolgilevitch from OOO SMD Balt Avtomatika.
With the MCA-2000, the material is now said to be able to be compacted in a more controlled manner and much more precisely. The system uses temperature sensors to measure the temperature of the paved asphalt. This information appears directly on the display and the roller operator can use it to compact in precisely those areas where the temperature is in the optimum temperature range from 100°C to 140°C. "During comparison measurements, the temperature displayed by the system was identical to the temperature that we measured and thereby facilitates a reliable temperature measurement", said Yuri Dolgilevitch. This prevents asphalt that is either too cold or too hot from being compacted, which can lead to material damages and, thus, to a reduced road quality.
The system also records the passes of the roller by means of GPS positioning and compares the target and actual passes. The current status is visualised in real time on the seven-inch, touch-screen display: using a colour scheme, the roller operator can identify where a sufficient amount of compaction has been performed and what sections still require passes.
"In addition to supporting the operator, it is important for us that this data still be available afterwards. Because only in this way can we document the quality", said Brinks. This is made possible by the ability of the MCA-2000 to record and store all data such as passes and temperature. The data is compiled for the report and read out using a USB stick and is then available for future use and documentation.
By exactly monitoring the compaction processes, unnecessary passes are avoided. This is said by MOBA to reduce MCA-2000 installed machine fuel use by around 20%, while also increasing machine efficiency.
Completion of the US$32.55 million (1bn RUB) project is scheduled for 2015 and should allow comfortable travel for residents, tourists and football fans travelling to the 2018
For ZAO VAD, the construction consortium which is performing the work, precise and error-free construction of the road has been a top priority.
To accomplish this, the right material composition, material temperature, smooth paving process and then a precise compaction of the asphalt are necessary.
"During road construction, it is very important that work be performed exactly and painstakingly from the first to the last work step. Compaction of the paved material is one aspect that plays a key part for a successful result", said Ronald Brinks of ZAO VAD. For this purpose, ZAO VAD, in cooperation with OOO SMD Balt Avtomatika, installed the
"The requirement in this project was to make the compaction more controllable as, in the past, this was based solely on the experience of the worker and there was no continuous monitoring of the results. Moreover, it was to be possible to create a quality certificate for the performed compaction work. That is why we decided to use the MCA-2000", said Yuri Dolgilevitch from OOO SMD Balt Avtomatika.
With the MCA-2000, the material is now said to be able to be compacted in a more controlled manner and much more precisely. The system uses temperature sensors to measure the temperature of the paved asphalt. This information appears directly on the display and the roller operator can use it to compact in precisely those areas where the temperature is in the optimum temperature range from 100°C to 140°C. "During comparison measurements, the temperature displayed by the system was identical to the temperature that we measured and thereby facilitates a reliable temperature measurement", said Yuri Dolgilevitch. This prevents asphalt that is either too cold or too hot from being compacted, which can lead to material damages and, thus, to a reduced road quality.
The system also records the passes of the roller by means of GPS positioning and compares the target and actual passes. The current status is visualised in real time on the seven-inch, touch-screen display: using a colour scheme, the roller operator can identify where a sufficient amount of compaction has been performed and what sections still require passes.
"In addition to supporting the operator, it is important for us that this data still be available afterwards. Because only in this way can we document the quality", said Brinks. This is made possible by the ability of the MCA-2000 to record and store all data such as passes and temperature. The data is compiled for the report and read out using a USB stick and is then available for future use and documentation.
By exactly monitoring the compaction processes, unnecessary passes are avoided. This is said by MOBA to reduce MCA-2000 installed machine fuel use by around 20%, while also increasing machine efficiency.