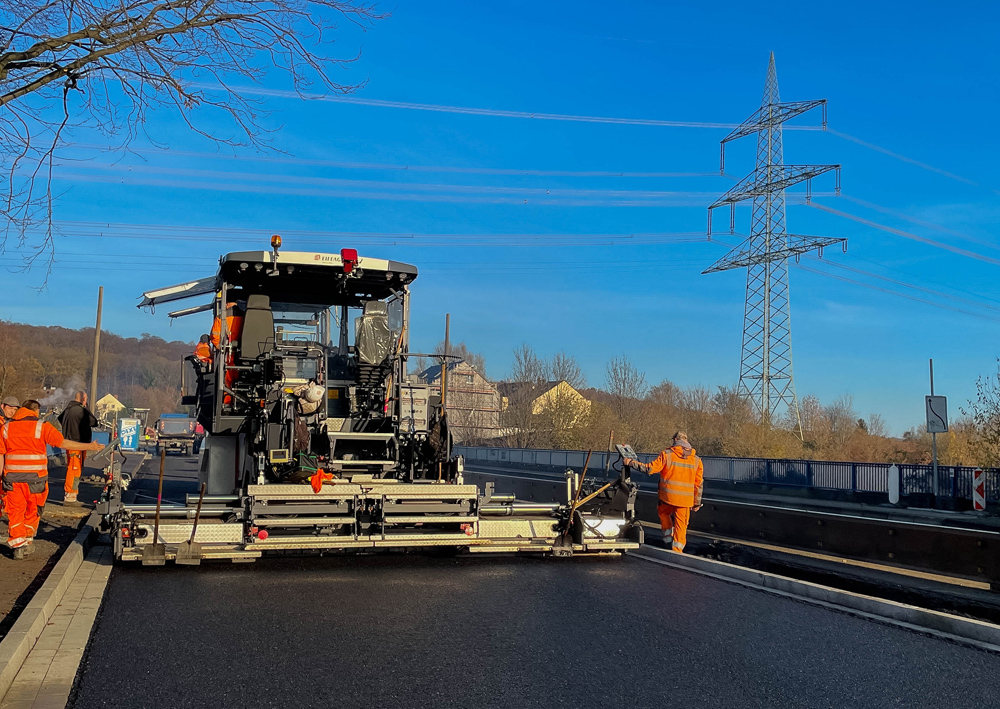
The new system operates on the firm’s proven four-tube design and allows the delivery of material for very thin layers, while ensuring quality. To achieve this, the firm has replaced the standard vibration unit with redesigned high compaction units, one for each screed section
Operated through the screed mounted control panel, team members have direct access to compaction controls, which include tamper, vibration and the setting of the additional available compaction pressures. All functions are displayed on the control panel.
The new high compaction unit is capable of delivering 3000rpm with a maximum high compaction pressure of 70bar across all four sections simultaneously. This is due to an integrated lift system that allows for adjustment of the forces coming from the high compaction unit (HCU), with the hydraulic pressure fully independent from the vibration speed.
In practical terms, this means the screed operator can control and adjust pressure and vibration from the two screed remote control panels, positioned either side of the screed, or the main operator panel. These controls come with common pre-settings for the different course types and adapt to the individual needs of the jobsite, using the expertise of the operator.
By controlling pressure and vibration speed, operators can provide the compaction level needed for the jobsite conditions. This applies to a whole range of jobs as the system still delivers the maximum compression possible by combining higher vibration frequencies and the additional pressure to push the unit and material forward. The ability to optimise performance by adjusting speed and pressure individually helps to boost productivity and deliver a high-quality final finish. The Dynapac machines are also said to produce lower working noise levels than other equipment, while having reduced wear rates to help boost reliability and uptime.
To provide better consistency, the new screed benefits from two Dynapac Assistant Systems. The MatTracker sensor system is designed to keep the operator safe from oncoming traffic. To do this MatTracker uses sensors to automatically monitor the position of the screed against existing mats or edging stones. The system then moves the screed horizontally to ensure correct material placement. With MatTracker ensuring the right horizontal positioning of the screed, the system keeps the operator inside the machine’s safety area and away from live traffic.
The integrated levelling system meanwhile uses factory-fitted technology from Dynapac’s machine control technology partner, MOBA. The MOBA package uses sonic sensors that can link with the MOBA BigSki software or other third-party systems. Dynapac’s screed can also support 3D screed levelling independent from the existing base solution through partnerships with the machine control specialists: Trimble; Topcon; Leica Geosystems. These systems can be retrofitted into the machine’s Canbus architecture to use GPS location, and jobsite data measured as the screed operates. Using the high compaction screed delivers better high-pressure layering and can also save up to 50% of the roller passes needed to reach the optimised compaction, reducing both fuel consumption and equipment movements onsite.
A range of screed options is also available, such as side shields to limit the material flow to the sides for more defined edges. A number of different options are offered including standard manually adjusted units, hydraulic variants and also fully foldable types. The fully foldable option removes the need for manual lifting or coupling, as well as eliminating disassembly. It allows operators to set up machines for work and transportation in a matter of minutes. This option is popular with countries where transport widths have to meet tight regulations anywhere between 2.55-3m. All side shield options can couple with an edge former offering 30-70° angle options to form the edge of the mat.
Other key options include lighting for night working, modular electric and gas heating versions, and a heating rod to prevent material from sticking to the screed.