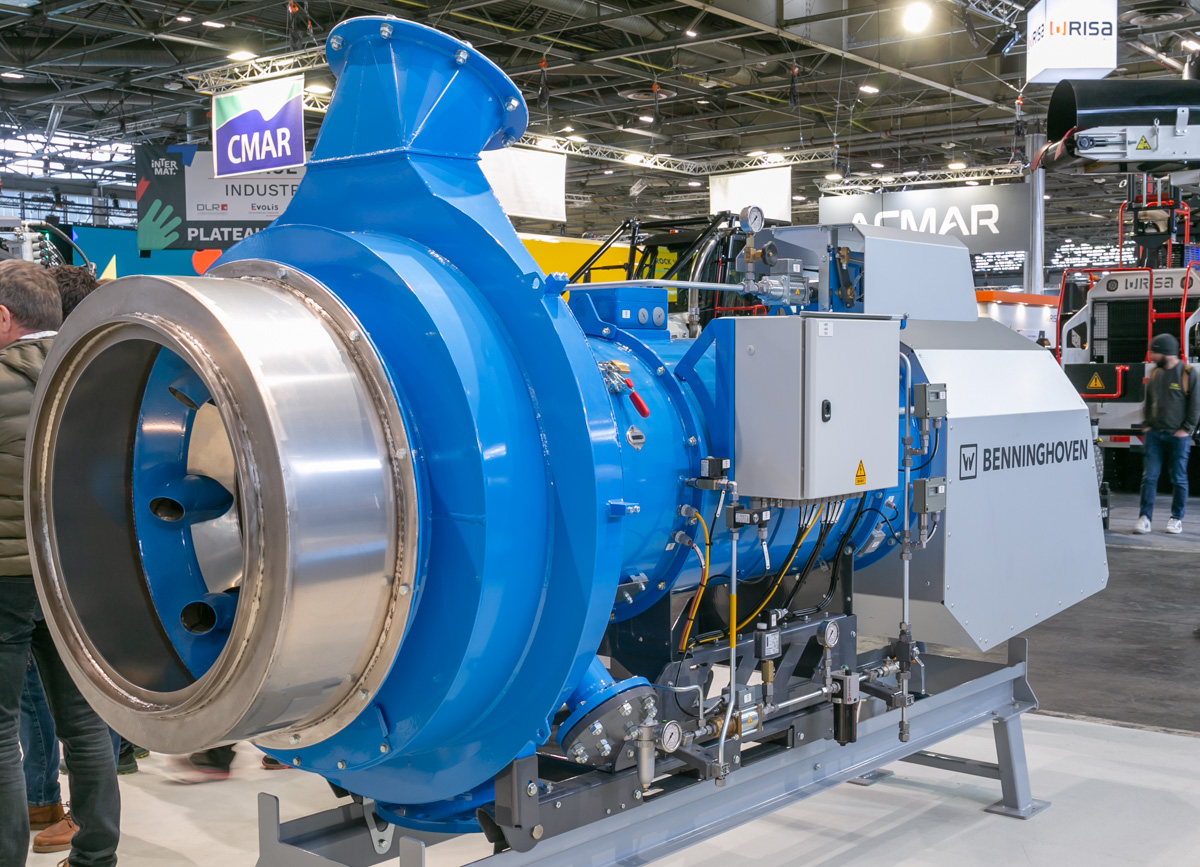
One of Benninghoven’s customers in Norway is now using the firm’s innovative hydrogen burner to produce several thousand tonnes of asphalt.
The hydrogen burner from Benninghoven is supplied with an intelligent control system to maximise the efficiency during asphalt production. This includes control of the feed systems, including the pressure control section, drying section with burner and burner control. It is a multi-fuel unit and can use natural gas and light oil in addition to hydrogen. A novel feature is that it can be set to use any combination of the three fuels, with any percentage of either also, depending on fuel availability.
To make the asphalt production process more efficient, Benninghoven says it has developed a new generation of burners that includes the control and drying system alongside the burner itself. With this system, up to four separate burners can be operated at the same time.
This versatile approach increases the cost-effectiveness of the plant as an owner can use the best-available energy sources. Switching between fuels or combinations of multiple fuels is done on the fly, meaning that no shutdown or downtime is required and with only minimal temperature fluctuations in the process. Emissions are kept low when using hydrogen as a fuel are kept very low, with minimal NOx being produced.
The company also says that the power draw has been reduced by 20% while keeping the feed capacity constant. Heat transfer efficiency has been significantly improved by maximising the use of the burner space and providing a burner control and geometry that ensures optimum flame production for each fuel. Another significant benefit for plant operators is the 5dB reduction in noise emissions.
Green hydrogen is a sustainable fuel, producing no greenhouse gases and is suitable for the heating process thanks to its high energy density. In many cases, facility operators wanting to start using hydrogen as a fuel experience difficulties due to current limitations in their infrastructure. Burner technologies from Benninghoven can be used to equip both new facilities and existing asphalt mixing plants, while retrofit solutions can be deployed in plants from other manufacturers. This gives a plant operator the chance to upgrade to the latest technologies, an important aspect for ensuring economic, sustainable asphalt production and long-term plant operations.
With one unit already in use, the firm is currently in discussions with customers in Europe and the Middle East for a further four units.