Wirtgen cold milling machines recently demonstrated their ability on runway rehabilitation work at Alghero-Fertilia Airport in Sardinia. Alghero-Fertilia Airport, about 8km northwest of Alghero, is one of three commercial airports on the Italian island. Built as a military airport in the late 1930s, Alghero-Fertilia still occasionally serves this purpose today.
It is also a major hub for low-cost carriers that ferry many of the annual 1.7 million passengers who pass through the airport. Summer tourist mo
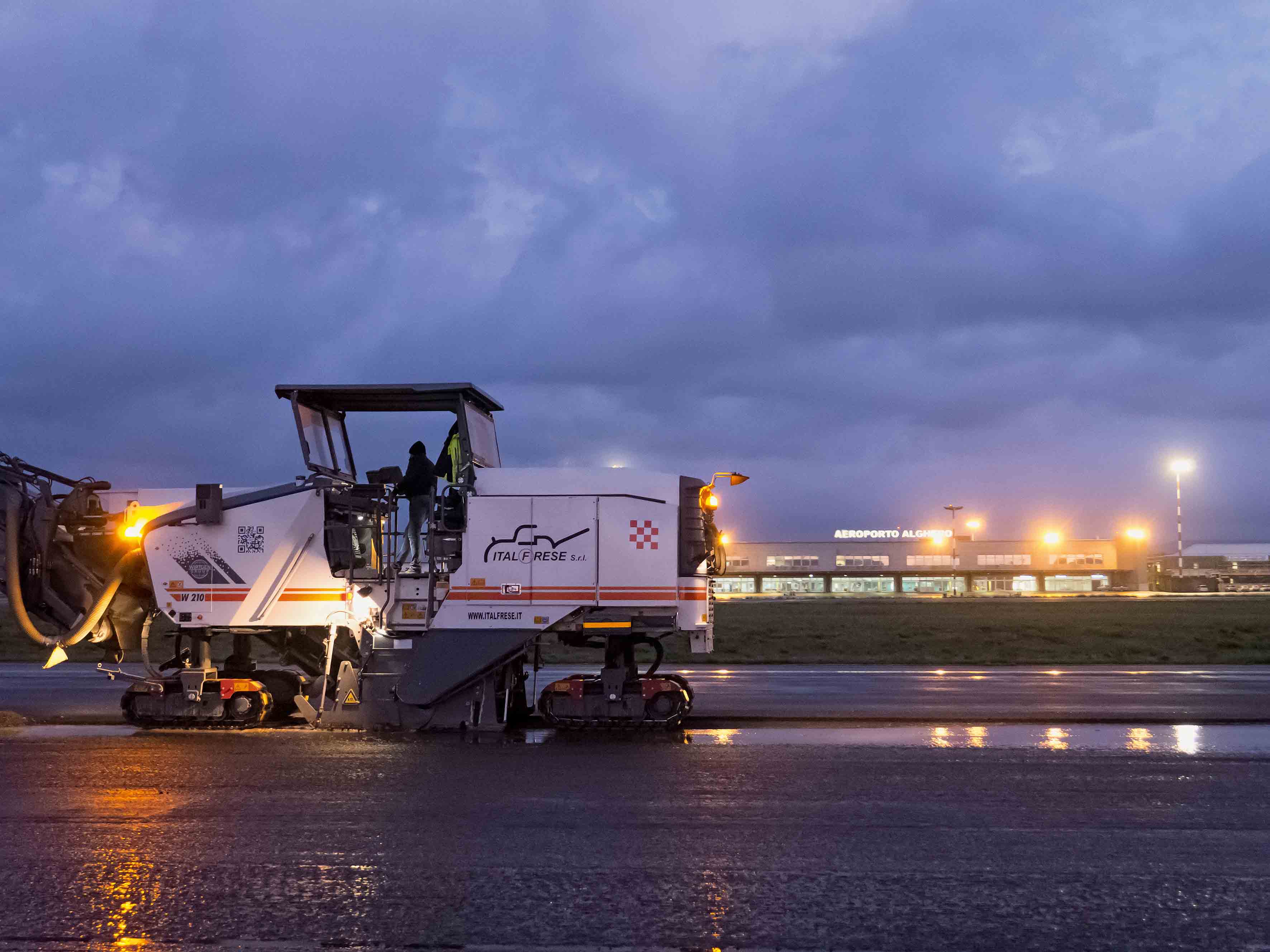
Two W210 cold milling machines removed the 5cm asphalt pavement over a 2.1km section.
Wirtgen cold milling machines recently demonstrated their ability on runway rehabilitation work at Alghero-Fertilia Airport in Sardinia.
Alghero-Fertilia Airport, about 8km northwest of Alghero, is one of three commercial airports on the Italian island. Built as a military airport in the late 1930s, Alghero-Fertilia still occasionally serves this purpose today.
It is also a major hub for low-cost carriers that ferry many of the annual 1.7 million passengers who pass through the airport. Summer tourist months are busiest so operating company Società di Gestione Aeroporto di Alghero used the off-season in early November to carry out necessary maintenance.
Work included rehabilitation of the runway surface over 2.1km and a width of up to 19m. In addition, underlying courses had to be stabilised over a further 600m and a width of 19m at the end of runway 20. The ground there is subject to heavier loads due to aircraft landings. This has led to a reduction in load-bearing capacity resulting from both material fatigue and soil composition.
The size of the area to be milled, the standards which applied to the stabilisation work and the short time allowed for the project called for a service provider with the necessary experience and equipment. The contract was awarded to the company Italfrese from San Damiano d’Asti, south of Turin in northern Italy. Stabilisation work was carried out by another Turin company, subcontractor Consolida.
Italfrese is a renowned Italian provider of milling services with a large fleet of machines comprising 102395 Wirtgen cold milling machines, a Wirtgen soil stabiliser of type WR2000 and a binding agent spreader of type SW 10TC from Streumaster.
Logistics was indisputably the biggest challenge for both companies. All the required machinery had to be shipped from the mainland – two Wirtgen cold milling machines W210 and a W200i, two soil stabilisers of type WR2000, two Streumaster binder spreaders of type SW 10 TC, two road sweepers and three service vans.
Semi-trailers brought the construction machines to the port of Genoa from where they were loaded onto a ferry for the 12-hour crossing to Porto Torres in the northwest of the island, roughly 25km from Alghero-Fertilia Airport.
The airport was closed for the work. Only two days and nights were allowed for milling so that the asphalt could be paved without delay. To remain on schedule, Italfrese set up an efficient system for supplying water and refueling the cold milling machines and other equipment before milling work started. Contracts were signed with local haulage companies to ensure that a sufficient number of trucks available when needed to transport reclaimed asphalt.
Work started at the end of runway 20. But before the soil was stabilised by the two WR2000 machines, Wirtgen’s cold milling machines removed all the 30cm-thick pavement over an area of 11,400m². This was done in several passes and in staggered formation at high feed rates.
Attilio Demuro, a cold milling machine operator for Italfrese, praised the machine’s easy-to-understand display. “It enables us to concentrate and have everything under control at all times, despite the complexity of the mechanical, hydraulic and electronic systems. This is where the LEVEL PRO leveling system and the hydraulic sensors for measuring the milling depth offer genuine added value." In addition, he found that abundant lighting ensured excellent visibility, even in the dark.
Ernesto Franco, chief executive of Italfrese, monitored the complete milling project on site. "This is not our first airport project, but every such job site is a different ball game. Just because we have the experience, highly qualified machine operators and a good logistics and organisational structure, that does not mean that we can afford to lose sight of the imponderables associated with such a job."
With their 2m-wide milling drum, the W210 and W200 can reclaim asphalt to a maximum depth of 33cm. Drum speed can be set directly from the operator's platform to 1,600rpm, 1,800rpm or 2,000rpm by a selector switch. The low speed of 1,600 rpm – as used for removal of complete road pavements in Alghero – is ideal for a maximum milling output and lower fuel consumption per cubic meter of reclaimed material with low wear on the cutting tools.
The middle rate of 1,800rpm is perfect for standard milling jobs, such as removal of surface courses. It also delivers RAP in appropriate particle sizes. The top speed of 2,000rpm is used to remove thin pavements at maximum feed rates while producing a good milled result.
Once the cold milling machines had removed the pavement at the end of the runway - in less time than was scheduled - excavators removed the base to a depth of 80cm in just one night shift plus the following morning. They were followed by two WR2000 soil stabilisers. Over the next few days, these mobile machines stabilised the first 30cm with 2.5% lime and 2.5% cement, as required on account of the clay soil. The remaining 50cm of soil were also homogenised by the two WR 2000 machines, this time adding 3% cement.
At the same time, the two W210 cold milling machines tackled the 2.1km runway from which the surface course had to be removed to a depth of 5cm. But the challenge was the size of the area to be milled, rather than the milling depth. A total area of 37,800m² had to be milled, yielding a RAP volume of roughly 1,900m³. The two W210 machines performed outstandingly, with their enormous feed rate and medium milling drum speed, says Demuro. "Despite the large area, the W6-G/20X cutting tools showed little sign of wear when the work was complete," he says.
Low wear was attributable to the carefully coordinated interaction between cold milling machine and point-attack tools as well as the use of low milling drum speeds. The dual-engine concept of the W210 also proved to be economical. Depending on the power required, this concept allows the milling machine to operate with one or two engines.
The two diesel engines are linked by a power belt. Only the first engine was in operation whenever the performance level required to achieve results was low. It served as the power unit for all functional groups. The second engine was activated for milling at full power. The advantages were obvious: noise levels, vibrations and exhaust emissions are lower when the second engine is deactivated. At the same time, diesel consumption was also significantly lower.
Since the dual-engine concept and the three milling drum speeds were optimally adapted to meet the job’s requirements, milling on the airfield could proceed quickly and cost-efficiently. Soil stabilisation by the two WR2000 machines also proceeded within the agreed time frame.
In this way, the fleet of Wirtgen machines successfully laid the ground for asphalt paving and subsequent work. Consequently, Alghero-Fertilia Airport could open on schedule.
Alghero-Fertilia Airport, about 8km northwest of Alghero, is one of three commercial airports on the Italian island. Built as a military airport in the late 1930s, Alghero-Fertilia still occasionally serves this purpose today.
It is also a major hub for low-cost carriers that ferry many of the annual 1.7 million passengers who pass through the airport. Summer tourist months are busiest so operating company Società di Gestione Aeroporto di Alghero used the off-season in early November to carry out necessary maintenance.
Work included rehabilitation of the runway surface over 2.1km and a width of up to 19m. In addition, underlying courses had to be stabilised over a further 600m and a width of 19m at the end of runway 20. The ground there is subject to heavier loads due to aircraft landings. This has led to a reduction in load-bearing capacity resulting from both material fatigue and soil composition.
The size of the area to be milled, the standards which applied to the stabilisation work and the short time allowed for the project called for a service provider with the necessary experience and equipment. The contract was awarded to the company Italfrese from San Damiano d’Asti, south of Turin in northern Italy. Stabilisation work was carried out by another Turin company, subcontractor Consolida.
Italfrese is a renowned Italian provider of milling services with a large fleet of machines comprising 10
Logistics was indisputably the biggest challenge for both companies. All the required machinery had to be shipped from the mainland – two Wirtgen cold milling machines W210 and a W200i, two soil stabilisers of type WR2000, two Streumaster binder spreaders of type SW 10 TC, two road sweepers and three service vans.
Semi-trailers brought the construction machines to the port of Genoa from where they were loaded onto a ferry for the 12-hour crossing to Porto Torres in the northwest of the island, roughly 25km from Alghero-Fertilia Airport.
The airport was closed for the work. Only two days and nights were allowed for milling so that the asphalt could be paved without delay. To remain on schedule, Italfrese set up an efficient system for supplying water and refueling the cold milling machines and other equipment before milling work started. Contracts were signed with local haulage companies to ensure that a sufficient number of trucks available when needed to transport reclaimed asphalt.
Work started at the end of runway 20. But before the soil was stabilised by the two WR2000 machines, Wirtgen’s cold milling machines removed all the 30cm-thick pavement over an area of 11,400m². This was done in several passes and in staggered formation at high feed rates.
Attilio Demuro, a cold milling machine operator for Italfrese, praised the machine’s easy-to-understand display. “It enables us to concentrate and have everything under control at all times, despite the complexity of the mechanical, hydraulic and electronic systems. This is where the LEVEL PRO leveling system and the hydraulic sensors for measuring the milling depth offer genuine added value." In addition, he found that abundant lighting ensured excellent visibility, even in the dark.
Ernesto Franco, chief executive of Italfrese, monitored the complete milling project on site. "This is not our first airport project, but every such job site is a different ball game. Just because we have the experience, highly qualified machine operators and a good logistics and organisational structure, that does not mean that we can afford to lose sight of the imponderables associated with such a job."
With their 2m-wide milling drum, the W210 and W200 can reclaim asphalt to a maximum depth of 33cm. Drum speed can be set directly from the operator's platform to 1,600rpm, 1,800rpm or 2,000rpm by a selector switch. The low speed of 1,600 rpm – as used for removal of complete road pavements in Alghero – is ideal for a maximum milling output and lower fuel consumption per cubic meter of reclaimed material with low wear on the cutting tools.
The middle rate of 1,800rpm is perfect for standard milling jobs, such as removal of surface courses. It also delivers RAP in appropriate particle sizes. The top speed of 2,000rpm is used to remove thin pavements at maximum feed rates while producing a good milled result.
Once the cold milling machines had removed the pavement at the end of the runway - in less time than was scheduled - excavators removed the base to a depth of 80cm in just one night shift plus the following morning. They were followed by two WR2000 soil stabilisers. Over the next few days, these mobile machines stabilised the first 30cm with 2.5% lime and 2.5% cement, as required on account of the clay soil. The remaining 50cm of soil were also homogenised by the two WR 2000 machines, this time adding 3% cement.
At the same time, the two W210 cold milling machines tackled the 2.1km runway from which the surface course had to be removed to a depth of 5cm. But the challenge was the size of the area to be milled, rather than the milling depth. A total area of 37,800m² had to be milled, yielding a RAP volume of roughly 1,900m³. The two W210 machines performed outstandingly, with their enormous feed rate and medium milling drum speed, says Demuro. "Despite the large area, the W6-G/20X cutting tools showed little sign of wear when the work was complete," he says.
Low wear was attributable to the carefully coordinated interaction between cold milling machine and point-attack tools as well as the use of low milling drum speeds. The dual-engine concept of the W210 also proved to be economical. Depending on the power required, this concept allows the milling machine to operate with one or two engines.
The two diesel engines are linked by a power belt. Only the first engine was in operation whenever the performance level required to achieve results was low. It served as the power unit for all functional groups. The second engine was activated for milling at full power. The advantages were obvious: noise levels, vibrations and exhaust emissions are lower when the second engine is deactivated. At the same time, diesel consumption was also significantly lower.
Since the dual-engine concept and the three milling drum speeds were optimally adapted to meet the job’s requirements, milling on the airfield could proceed quickly and cost-efficiently. Soil stabilisation by the two WR2000 machines also proceeded within the agreed time frame.
In this way, the fleet of Wirtgen machines successfully laid the ground for asphalt paving and subsequent work. Consequently, Alghero-Fertilia Airport could open on schedule.