New US-style pavers are coming to market, writes Mike Woof. Paving Techniques for the North American market focus on productivity, with manufacturers offering new machines specially for this sector. The US paving market is very different from Europe, with manufacturers having focussed on productivity so as to be able to surface the country’s long distance highway construction projects.
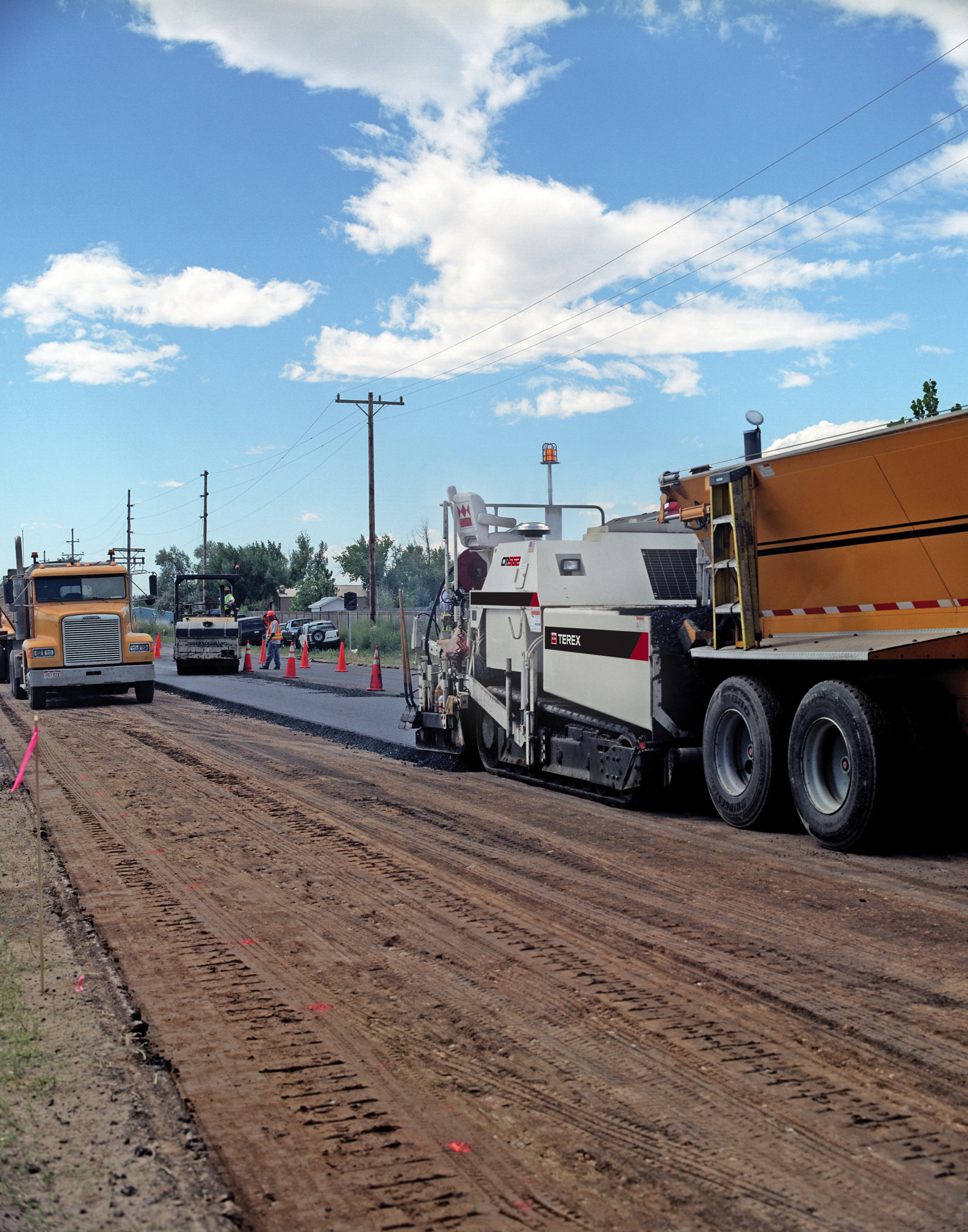
Terex Roadbuilding’s new CR562 paver is said to be one of the most productive machines on the North American market
New US-style pavers are coming to market, writes Mike Woof
Paving Techniques for the North American market focus on productivity, with manufacturers offering new machines specially for this sector. The US paving market is very different from Europe, with manufacturers having focussed on productivity so as to be able to surface the country’s long distance highway construction projects.Some manufacturers like
A number of firms are now offering new units for the North American market, including Dynapac, Terex and Volvo. Dynapac is introducing its new paver line for the North America market in the shape of its F1000T tracked and F1000W wheeled models. They can pave surfaces up to 3.05m wide and have been designed from the ground up, with input from US dealers and contractors. The F1000 series pavers are said to be easy to service and are rugged and reliable, with heavy-duty welded frames, dual swing-out operator stations and a low deck height. Benefits include high visibility of the work area, hopper and auger for the operator.
Features include a high-performance outboard auger drive and a novel design with no auger chain drive box to minimise centre line segregation. The machine can be fitted with
Simple controls and multi- function display are said to be operator friendly and grouped for convenience. A front-wheel assist steering system improves turning, with precise paving speed control.
Powered comes from a
asphalt fumes.
Meanwhile Terex is offering the new CR652 and CR662RM pavers. The CR562 runs on rubber tracks and offers paving widths of up to 9.1m. This is now the largest paver in the Terex Roadbuilding line and is claimed to be one of the most productive on the market. The machine has a standard 15tonne hopper capacity but its heavy-duty frame allows it to be fitted with an insert to boost capacity up to 25tonnes if necessary. This provides extra surge capacity for developing continuous, full-width paving applications such as airport and major highway construction. With its hopper insert, the CR562 paver can deliver over 20% greater capacity than competing machines according to Terex.
The feed system features an ironclad 78mm pitch offset-link roller slat chain with hardened eight tooth slat drive sprockets and a hard-wearing chain for slat and auger drive. The machine also has 9.5mm slat liners and heavy-duty slat bars with Terex guarantees of 5 years/5,000 hours and 10 years/10,000 hours respectively.
The CR662RM shares many features with the CR562. However the CR662RM also has a remix auger delivery configuration. This is a novel system designed to minimise material segregation and features two sets of two counter-rotating augers in the hopper to reblend material. The augers draw down material from all areas of the hopper to minimise material and thermal segregation, which allows for a homogeneous mat texture and more consistent temperatures across the width of the mat.
Other key features of the CR562 include the firm’s patented frame raise and three-point suspension systems. The novel frame raise system raises and lowers the rear of the paver, allowing an operator to adjust the head of material at the spreading augers, minimising segregation. Meanwhile the three-point suspension system isolates the frame from the drive and allows the paver to maintain a constant material feed height at the screed.
Power for the CR562 comes from a Tier 3 compliant diesel rated at 194kW and contractors have a choice of three different screed models, the diesel Fastach 10, electric VersaScreed 210, and the electric or diesel Stretch 20, while maximum paving depths of 305mm and widths of 9.1m can be achieved.
And from Volvo, the PF6160 and PF6170 wheel-mounted pavers form part of the firm’s PF6000-Series highway-class asphalt paver line. The PF6160 and PF6170 are powered by a 153kW Tier 3 compliant Cummins diesel and also have 30kW on-board generators. The machines feature
a patented level-load suspension design, which uses the two drive wheels and the centre of the bogie hydraulic system for consistent and even ground contact to increase stability. Both machines have the firm’s two-wheel front-wheel assist as standard while the PF6170 can be configured with an optional four-wheel frontwheel assist for all-wheel-drive capability.
The auger systems are independent of the conveyor with each of the twin auger and conveyor drives using sonic sensors for precise material handling. The conveyor system features chains with automatic tensioning, while the conveyor chain cover cleans itself and reversible augers and reversible conveyors are also offered as options. Hopper capacity is 13tonnes, allowing a production throughput of 744tonnes/hour.
The dual control stations pivot at two points and the seats can be extended over the sides for visibility. The open deck is said to maximise visibility, while the operator panel can be tilted or swiveled as required. The Volvo PF6160 and PF6170 can be fitted with the Omni 318, Omni 1000 or Ultimat 200 screeds, offering screed widths of up to 3m and maximum paving widths 8m.