The rural roads near Brandýs nad Labem, in the heart of the Czech Republic, may not be as heavily travelled as their counterparts in Prague, about 25km (15.5 miles) to the southwest, but they are nevertheless crucial pipelines to the rural and agricultural areas of the country. An assessment by regional authorities indicated that these roads are in need of repair. That led to cold planing and paving work on a series of rural roads near Brandýs nad Labem. Regional authorities have two key requirements: The r
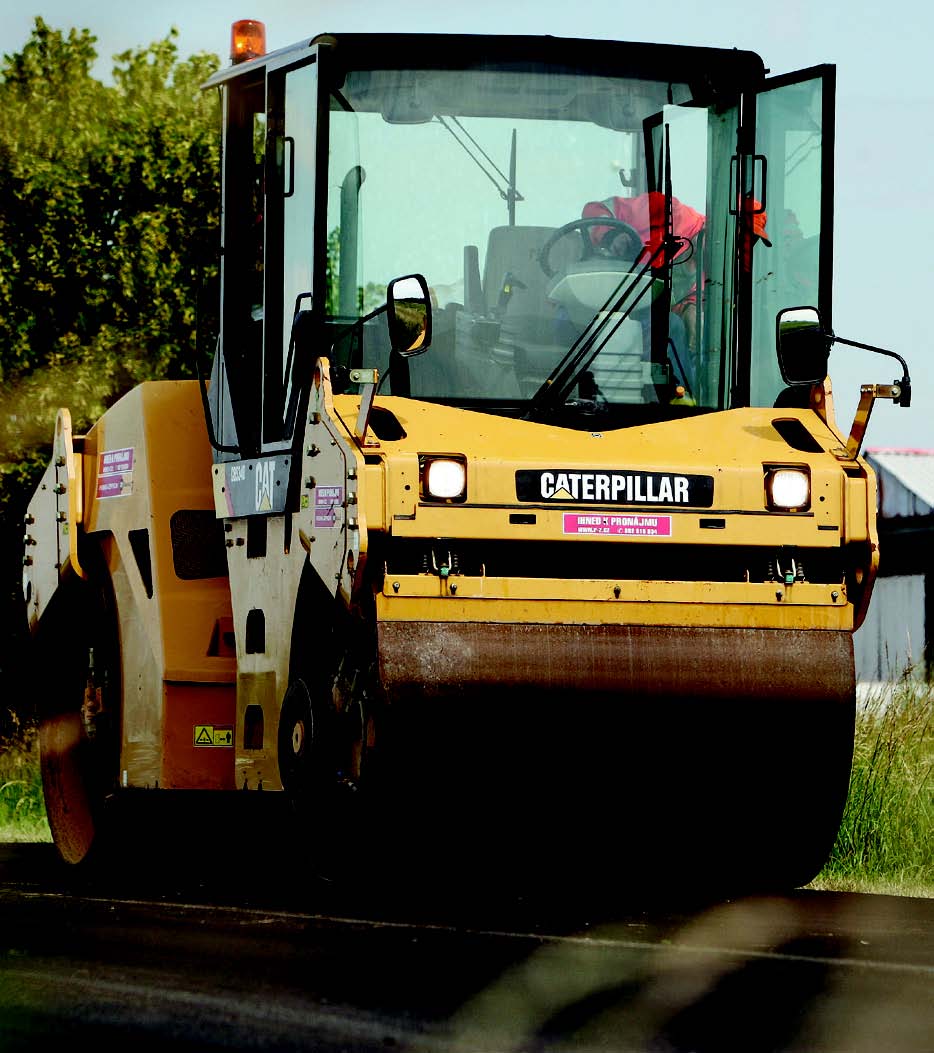
Properly planned compaction efforts are crucial to speedy paving.
The rural roads near Brandýs nad Labem, in the heart of the Czech Republic, may not be as heavily travelled as their counterparts in Prague, about 25km (15.5 miles) to the southwest, but they are nevertheless crucial pipelines to the rural and agricultural areas of the country.
An assessment by regional authorities indicated that these roads are in need of repair. That led to cold planing and paving work on a series of rural roads near Brandýs nad Labem.
Regional authorities have two key requirements: The roads must stay open during the work because many are the only viable option, and the work must be completed quickly (five days for one particular stretch of road) to permit usual traffic patterns to resume as soon as possible.
USK s.r.o., headquartered in Mladá Boleslav, was hired to handle the regional road project. The key for the firm was transferring both the knowledge and the equipment often used in urban settings to the rural project, said Ing. Jan Horák, the company’s chief executive officer.
Brandýs nad Labem-Stará Boleslav has a population of about 15,000. It remains a town with a rural feel to this day, despite its proximity to Prague and the major thoroughfares between the two. Smaller roads, meanwhile, reach out from Brandýs nad Labem-Stará Boleslav to the rural areas. This is where the work took place.
Working at the 3m (10') width, a Cat® AP555E Asphalt Paver was assigned to handle the paving. The open road also meant the crew, particularly operators, had to watch out for traffic. The paver’s platform helped with this challenge. The seats could easily be turned for better visibility. Dual control stations enabled operators to switch seats without taking their eyes off the important work at hand.
The ability to easily work from either side of the operating platform also helped keep the paving train working at a quick pace, as did the grip of the Mobil-Trac™ system. The tracks grip the surface and thus provide both excellent manoeuvrability and speed that lead to outstanding quality and pace, said Jirí Široký, Sales Manager of Road Technology at7105 Phoenix-Zeppelin, the local Cat Dealer. “The Cat AP555E track paver easily moves over soft base materials and the operator can easily maneuver it when paving,” adds Široký.
Crews worked at a pace of up to 8m (26') per minute. They consistently reached the high end of the production target. This is a very quick pace considering the mat thickness of 50mm (2"). It requires all elements—trucking, paving and compaction—to be in sync.
Whereas the travelling speed of other machines with track undercarriages is 4km (2.5 miles) per hour, the medium class AP555E paver can travel up to four times faster. “Faster travelling speed means fewer delays during work, which is then reflected in the work results in the form of lower time requirements for the completion of a job,” said Široký.
The AP555E was also enhanced by a 190 litre (50 U.S. gallon) fuel tank, which eliminated the need for frequent refuelling and minimised work delays. “We only had to refuel every second day,” said Horák. “It’s a very important advantage. With the old paver (which was not a Cat machine) we had to refuel every day.”
USK Mladá Boleslav determined the total volume of material. They factored in a project length of 4,200m (2.6 miles), multiplied by the 6m (20’) width of the road, plus exits and entrances, at about 4,000 metric tons (4,400 U.S. tons). The deadline of five days meant the firm would have to place about 800 metric tons (882 U.S. tons) per day.
Each haul truck had a capacity of 30 metric tons (33 U.S. tons), and had to travel 40km (25 miles) from the plant to the jobsite. A round trip took approximately 90 minutes to two hours, equating to four round trips per truck per day. USK Mladá Boleslav then calculated it needed six trucks to keep the paver moving steadily.
The mix had a stone size of 4-8mm (0.15-0.30"); it arrived at a temperature of 160°C (320°F) and was placed at 145°C (295°F). The material was end-dumped into the paver.
USK Mladá Boleslav, like its parent company H-INTES s.r.o., had already purchased Cat earthmoving machines and compacting equipment prior to the contract, and now is pleased to also include pavers in its equipment lineup.
“We chose a Cat machine for road paving because it is an established and reliable brand,” said Horák. “Phoenix-Zeppelin offered us very good conditions and service. I expect that we should get a full return on our investment in the machine within an acceptable timeframe.”
A story by4018 Caterpillar Paving %$Linker: 2 External <?xml version="1.0" encoding="utf-16"?><dictionary /> 0 0 0 oLinkExternal Click here www.paving-news.com/register/ false http://www.paving-news.com/register/ false false %> to register for your personal copy of Paving News
An assessment by regional authorities indicated that these roads are in need of repair. That led to cold planing and paving work on a series of rural roads near Brandýs nad Labem.
Regional authorities have two key requirements: The roads must stay open during the work because many are the only viable option, and the work must be completed quickly (five days for one particular stretch of road) to permit usual traffic patterns to resume as soon as possible.
USK s.r.o., headquartered in Mladá Boleslav, was hired to handle the regional road project. The key for the firm was transferring both the knowledge and the equipment often used in urban settings to the rural project, said Ing. Jan Horák, the company’s chief executive officer.
The region
Brandýs nad Labem-Stará Boleslav is the town nearest the roadwork. The town—a merger of the once-independent towns Brandýs nad Labem and Stará Boleslav—is in the Czech Republic, in the central Bohemian Region, and technically rests within the metropolitan area of Prague. The origins of the towns date back to the 13th century.Brandýs nad Labem-Stará Boleslav has a population of about 15,000. It remains a town with a rural feel to this day, despite its proximity to Prague and the major thoroughfares between the two. Smaller roads, meanwhile, reach out from Brandýs nad Labem-Stará Boleslav to the rural areas. This is where the work took place.
The challenges
The recently completed five-day section is 4,200m (2.6 miles) long and 6 m (20') wide. Since half the road was required to remain usable, USK Mladá Boleslav needed a paver capable of working at a width of 3m (10'). This paver also had to be capable of laying down 800 metric tons (882 U.S. tons) of asphalt per day for five days. That meant the crew and paver had to achieve good production levels.Working at the 3m (10') width, a Cat® AP555E Asphalt Paver was assigned to handle the paving. The open road also meant the crew, particularly operators, had to watch out for traffic. The paver’s platform helped with this challenge. The seats could easily be turned for better visibility. Dual control stations enabled operators to switch seats without taking their eyes off the important work at hand.
The ability to easily work from either side of the operating platform also helped keep the paving train working at a quick pace, as did the grip of the Mobil-Trac™ system. The tracks grip the surface and thus provide both excellent manoeuvrability and speed that lead to outstanding quality and pace, said Jirí Široký, Sales Manager of Road Technology at
Crews worked at a pace of up to 8m (26') per minute. They consistently reached the high end of the production target. This is a very quick pace considering the mat thickness of 50mm (2"). It requires all elements—trucking, paving and compaction—to be in sync.
Speed when not paving, too
The paver worked for a half day in a single direction, then returned to that day’s starting point and laid down the second half of the road with a longitudinal joint. Time is lost while returning to the starting point, yet the AP555E again proved to be efficient.Whereas the travelling speed of other machines with track undercarriages is 4km (2.5 miles) per hour, the medium class AP555E paver can travel up to four times faster. “Faster travelling speed means fewer delays during work, which is then reflected in the work results in the form of lower time requirements for the completion of a job,” said Široký.
The AP555E was also enhanced by a 190 litre (50 U.S. gallon) fuel tank, which eliminated the need for frequent refuelling and minimised work delays. “We only had to refuel every second day,” said Horák. “It’s a very important advantage. With the old paver (which was not a Cat machine) we had to refuel every day.”
Planning for production
Planning played a key role. USK Mladá Boleslav in particular focused on material supplies, counting trucks and loads to ensure consistent delivery of asphalt. The steady delivery kept machines moving consistently, a crucial step in segregation prevention.USK Mladá Boleslav determined the total volume of material. They factored in a project length of 4,200m (2.6 miles), multiplied by the 6m (20’) width of the road, plus exits and entrances, at about 4,000 metric tons (4,400 U.S. tons). The deadline of five days meant the firm would have to place about 800 metric tons (882 U.S. tons) per day.
Each haul truck had a capacity of 30 metric tons (33 U.S. tons), and had to travel 40km (25 miles) from the plant to the jobsite. A round trip took approximately 90 minutes to two hours, equating to four round trips per truck per day. USK Mladá Boleslav then calculated it needed six trucks to keep the paver moving steadily.
The mix had a stone size of 4-8mm (0.15-0.30"); it arrived at a temperature of 160°C (320°F) and was placed at 145°C (295°F). The material was end-dumped into the paver.
Segregation prevention
A number of precautions were taken to prevent segregation. Loads were tarped at the plant to maintain temperature. In addition, special focus on the trucking pattern ensured mix arrived at proper temperatures. Four independent sensors on spreader augers and conveyors provided the proper amount of material to the AS4252C screed—electrically heated to help keep the temperature of the mix consistent.Compaction and completion
Specified compaction values were achieved with vibrating tampers on the paver's smoothing bar, followed by compaction with a Cat CD534B vibration roller weighing 12 metric tons (13 U.S. tons). The entire job was completed on time and surface smoothness and quality goals were met.USK Mladá Boleslav, like its parent company H-INTES s.r.o., had already purchased Cat earthmoving machines and compacting equipment prior to the contract, and now is pleased to also include pavers in its equipment lineup.
“We chose a Cat machine for road paving because it is an established and reliable brand,” said Horák. “Phoenix-Zeppelin offered us very good conditions and service. I expect that we should get a full return on our investment in the machine within an acceptable timeframe.”
A story by