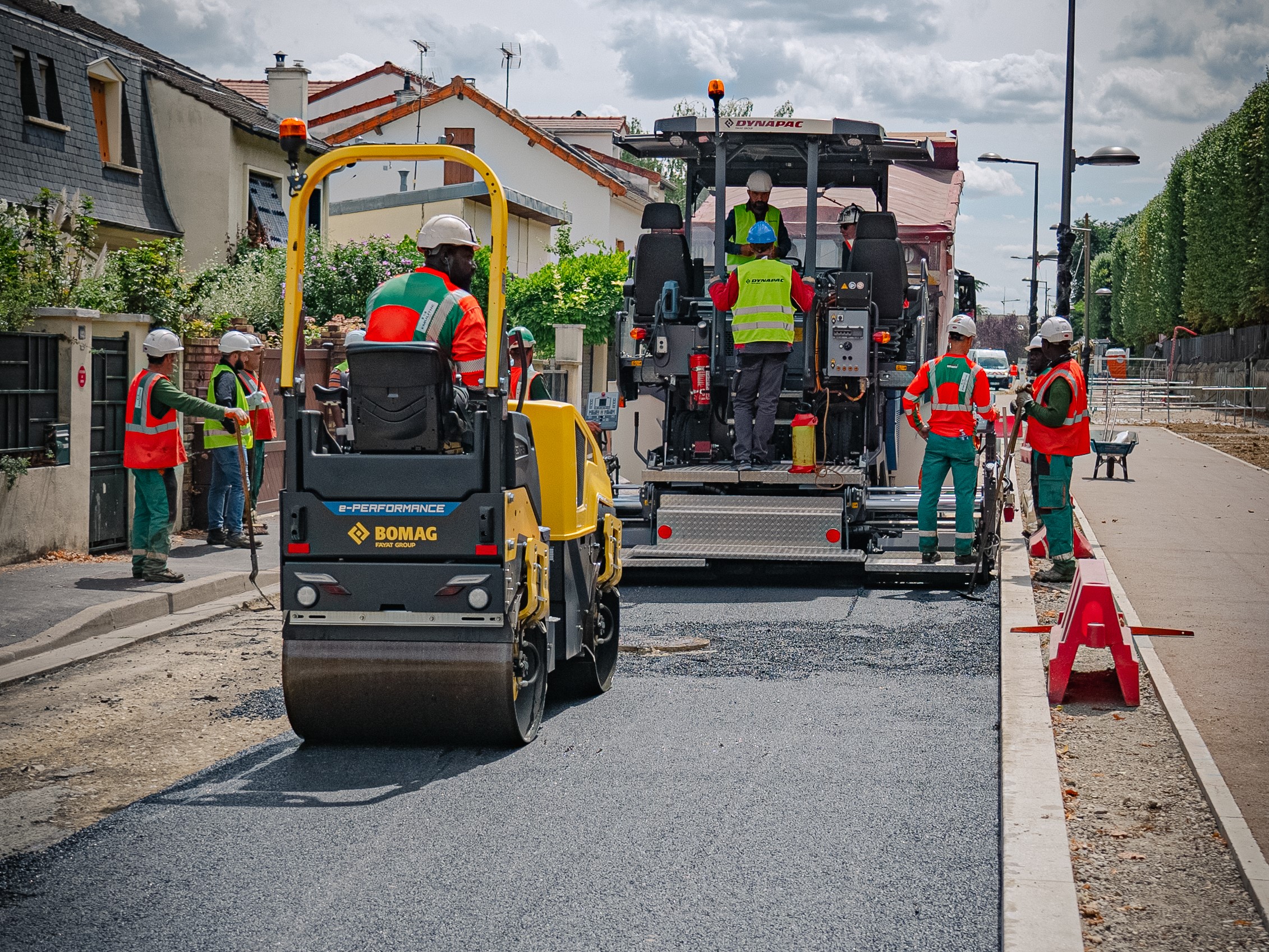
French contractor VINCI Construction has used construction machines from the FAYAT Group to deliver a low-carbon roadworks project using 100% electric equipment. Both VINCI and Fayat believe this to be a world first for a roadworks site.
VINCI Construction subsidiary Emulithe carried out the project using 100% electric equipment, as part of the works to resurface Rue du Lieutenant-Petit-Le-Roy in Chevilly-Larue (Val-de-Marne). The project involved making the street one-way and building a cycle path.
Following two days of familiarisation and training, Emulithe’s teams used – as part a 100% electric, rechargeable and silent sprayer, paver and roller, reducing greenhouse gas emissions and noise pollution compared with those produced by conventional worksite equipment. This was the first time that all-electric models of these three essential roadworks machines had been used on a single worksite.
THE BOX, from Secmair, is a sprayer designed with decarbonisation in mind. It boasts good range and insulation, usability and simple operation – all designed, engineered and manufactured in France.
The SD1800W e is the first mass-produced electric urban paver and is manufactured by Dynapac. Its 98kWh battery provides long range and fast recharging. Its low noise level, zero fine-particle emissions and zero smoke emissions make it ideal for urban use and mean it has a much lower carbon footprint.
The BOMAG BW 100 ADe-5 electric roller is rechargeable and equipped with sophisticated battery, motor and inverter technology. The manufacturer has integrated all these components to give the user a smooth and quiet driving experience, with performance matching those of conventional diesel models. Its silent operation and simple information display on the dashboard give drivers visibility and control, making the working day effective and stress-free.
The job provided a suitable opportunity to trial the performance of these new electric machines and see how their batteries would last during a working day. It also confirmed the significant reduction in CO2 emissions, with this low-carbon worksite saving 0.25 tonnes of CO2-eq/day compared with a worksite using conventional machines.
VINCI Construction has been working for a number of years on implementing measures and developing management tools1 aimed at reducing CO2 emissions by 40% by 2030. The use of electric-powered vehicles, light equipment, excavators and even lorries on worksites is growing.
VINCI Construction’s trial on a roadworks site of 100% electric versions of three key roadworks vehicles is a further step in its ongoing search for solutions to improve the energy and environmental performance of its operations, with the aim of gradually integrating low-carbon vehicles into its fleet.