With fuel-saving systems and measures to improve efficiency and safety, BOMAG hopes its second-generation pavers will make it a strong contender in the 17 to 20tonne class. Kristina Smith reports BOMAG has launched its second-generation of paving machines, the BF600-2 and the BF700-2. Unveiled at the recent manufacturer’s Asphalt Days event in Boppard, Germany, these pavers are the first to benefit from the fusion of Italian and German engineering, following the purchase of Marini in 2005 by Fayat Group whi
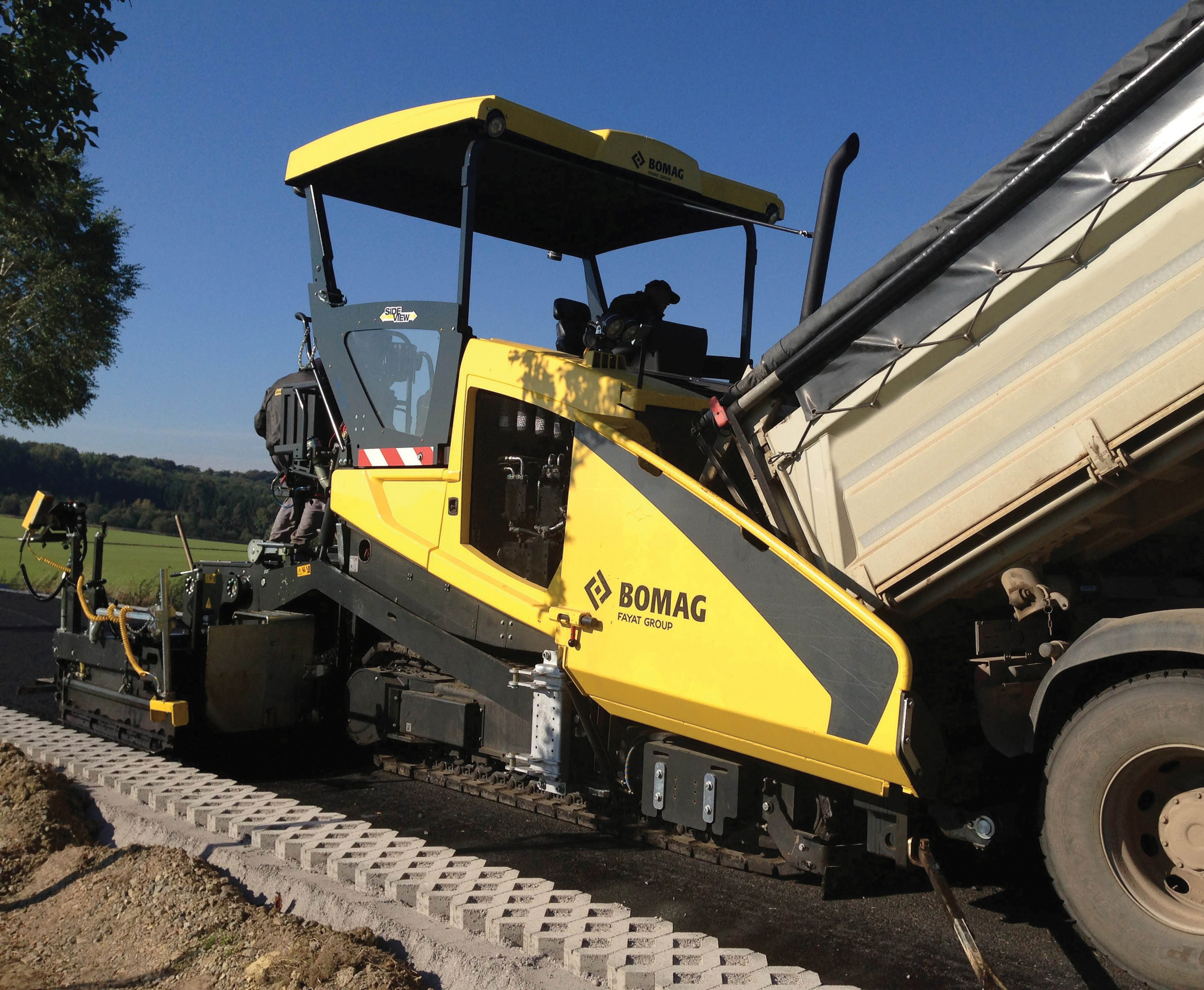
According to BOMAG, its second generation pavers offer greater efficiency and considerable improvements in performance
With fuel-saving systems and measures to improve efficiency and safety, Bomag hopes its second-generation pavers will make it a strong contender in the 17 to 20tonne class. Kristina Smith reports
172 Bomag has launched its second-generation of paving machines, the BF600-2 and the BF700-2. Unveiled at the recent manufacturer’s Asphalt Days event in Boppard, Germany, these pavers are the first to benefit from the fusion of Italian and German engineering, following the purchase of Marini in 2005 by 2779 Fayat Group which also owns Bomag.
“This new generation of paving machines is the first one where there has been a real joint development programme from the beginning,” said Jonathon Stringham, Bomag’s vice president marketing.
Bringing together engineers from two quite different cultures has taken some effort, with workshops and visits in both directions to help colleagues from Italy and Germany understand how their counterparts work and think. The hope is that the new machines appearing now will have gained the best of both approaches.
The new paving machines bring together a number of Bomag technologies which the manufacturer believes make them stand out from the competition: reduced fuel consumption, low noise levels, durable and reliable heating plates, and a patented sliding-Seat arrangement for the operator.
Bomag’s Ecomode system sees a hydraulically controlled fan automatically adapt the cooling power to the demand. Pumps regulate the flow of oil in three working circuits, depending on the power needed. This means that during work breaks or while the plates are heating up, for example, fuel consumption is reduced considerably.
“We have run it on job sites and shown that fuel consumption is significantly less than 10litres/hour, which is significantly best in class,” said Stringham. “That’s a very strong argument.”
With 5.1litre engines that are Tier 4 Interim/Stage IIIB compliant and deliver 116kW in the BF600 and 129kW in the BF700, these pavers are available with wheels or tracks. Both are compatible with Bomag’s S500 or S600 screeds which can give a paving width of up to 9m, with extensions. The quick fit sliding couplings on the screed extensions have been designed for ease of use, and give a set-up time half that for similar attachments, according to Bomag.
Another benefit highlighted by Stringham is the Magmalife heating system, with the heating elements cast into an aluminium block to make them more robust and durable. Heat-up time is also reduced to between 20 and 30 minutes, which Bomag says is gives a 25% energy saving compared to conventional machines.
“The aluminium heating plates give a much better lifetime,” said Stringham. “That is why we give a two-year warranty on heating plates. Nobody else gives that.”
Reliable heating and even distribution are important for the paving process, since cold patches can lead to unevenness. Longer life also means less whole life costs: Bomag said that when the levelling plates are routinely replaced after around two years, the heating plates can be reinstalled and reused, which is not the Case with the conventionally used heating rods.
The design of these second-generation pavers also focussed heavily on comfort, ergonomics and handling, says Bomag. The BF 600-2 and BF 700-2 benefit from the manufacturer’s patented Sideview system, where the Seat and operating console move sideways and can overhang the side of the machine by 60 cm either side. This set-up makes for safer, more efficient operation, allowing the operator to see all the working areas - the edge of the mat, the hopper, the auger and the screed – while still seated and protected by the roof.
Another feature which aims to increase efficiency is adjustable bumper rollers, with shock absorbers and integrated rocker, which are controlled hydraulically from the control stand. These can be adjusted to suit different truck lengths and allow shock-free docking of the truck.
Bomag manufactures the pavers at the ex-Marini factory at Alfonsine on the Eastern coast of Italy, 150km south of Venice. Currently both paving and milling machines are manufactured there, although by 2015 or 2016 all milling machine production will have moved over to Boppard , freeing up the Italian factory to concentrate on pavers.
The pre-series of the pavers was due out of the factory in Autumn this year, with production due to start in Spring 2014
“This new generation of paving machines is the first one where there has been a real joint development programme from the beginning,” said Jonathon Stringham, Bomag’s vice president marketing.
Bringing together engineers from two quite different cultures has taken some effort, with workshops and visits in both directions to help colleagues from Italy and Germany understand how their counterparts work and think. The hope is that the new machines appearing now will have gained the best of both approaches.
The new paving machines bring together a number of Bomag technologies which the manufacturer believes make them stand out from the competition: reduced fuel consumption, low noise levels, durable and reliable heating plates, and a patented sliding-Seat arrangement for the operator.
Bomag’s Ecomode system sees a hydraulically controlled fan automatically adapt the cooling power to the demand. Pumps regulate the flow of oil in three working circuits, depending on the power needed. This means that during work breaks or while the plates are heating up, for example, fuel consumption is reduced considerably.
“We have run it on job sites and shown that fuel consumption is significantly less than 10litres/hour, which is significantly best in class,” said Stringham. “That’s a very strong argument.”
With 5.1litre engines that are Tier 4 Interim/Stage IIIB compliant and deliver 116kW in the BF600 and 129kW in the BF700, these pavers are available with wheels or tracks. Both are compatible with Bomag’s S500 or S600 screeds which can give a paving width of up to 9m, with extensions. The quick fit sliding couplings on the screed extensions have been designed for ease of use, and give a set-up time half that for similar attachments, according to Bomag.
Another benefit highlighted by Stringham is the Magmalife heating system, with the heating elements cast into an aluminium block to make them more robust and durable. Heat-up time is also reduced to between 20 and 30 minutes, which Bomag says is gives a 25% energy saving compared to conventional machines.
“The aluminium heating plates give a much better lifetime,” said Stringham. “That is why we give a two-year warranty on heating plates. Nobody else gives that.”
Reliable heating and even distribution are important for the paving process, since cold patches can lead to unevenness. Longer life also means less whole life costs: Bomag said that when the levelling plates are routinely replaced after around two years, the heating plates can be reinstalled and reused, which is not the Case with the conventionally used heating rods.
The design of these second-generation pavers also focussed heavily on comfort, ergonomics and handling, says Bomag. The BF 600-2 and BF 700-2 benefit from the manufacturer’s patented Sideview system, where the Seat and operating console move sideways and can overhang the side of the machine by 60 cm either side. This set-up makes for safer, more efficient operation, allowing the operator to see all the working areas - the edge of the mat, the hopper, the auger and the screed – while still seated and protected by the roof.
Another feature which aims to increase efficiency is adjustable bumper rollers, with shock absorbers and integrated rocker, which are controlled hydraulically from the control stand. These can be adjusted to suit different truck lengths and allow shock-free docking of the truck.
Bomag manufactures the pavers at the ex-Marini factory at Alfonsine on the Eastern coast of Italy, 150km south of Venice. Currently both paving and milling machines are manufactured there, although by 2015 or 2016 all milling machine production will have moved over to Boppard , freeing up the Italian factory to concentrate on pavers.
The pre-series of the pavers was due out of the factory in Autumn this year, with production due to start in Spring 2014