Crushing equipment from Metso is helping boost production and efficiency at the Barrasford Quarry in the UK. Run by Tarmac Quarry products, the operation is now using a Lokotrack LT140 track-mounted mobile crusher, a pair of Lokolink mobile conveyors and several field conveyors. The company is changing the operation from a static to a mobile crushing operation, and it says installing the Metso machinery has helped reduce manpower at the site.
The crusher and the conveyors have replaced a pair of static c
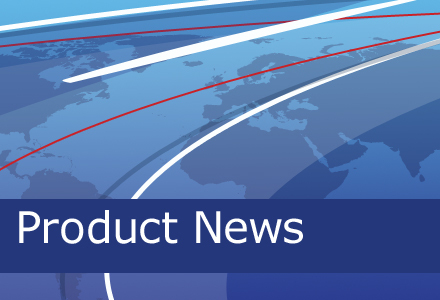
Crushing equipment from 6934 Metso is helping boost production and efficiency at the Barrasford Quarry in the UK.
Run by2399 Tarmac Quarry products, the operation is now using a Lokotrack LT140 track-mounted mobile crusher, a pair of Lokolink mobile conveyors and several field conveyors. The company is changing the operation from a static to a mobile crushing operation, and it says installing the Metso machinery has helped reduce manpower at the site.
The crusher and the conveyors have replaced a pair of static crushers and a rigid dump truck haulage fleet at the 135ha site. However, this changeover has required considerable interaction between Tarmac and engineers from both Metso Minerals (UK) and from its parent company in Finland.
The site has reserves of around 45 million tonnes, has been in use since 1880 and at present produces around 500,000tonnes/year. Some 85% of the product is a hard and abrasive quartz dolorite (whinstone) that is used in Tarmac road products and is very suitable for this purpose. The remaining 15% is blue limestone that is used for aggregates.
The quarry is 20m deep, and there are plans to lower the base still further to around 35m, which is unusual as most other local deposits lie at a depth of 13-15m.
Material is won by blasting, which takes place every three weeks, with each blast freeing around 30,000 tonnes. As the site has no immediate neighbours, noise and dust from blasting are not an issue, although the site is closely monitored and water suppression is used at the face.
The new LT140 has replaced a pair of ageing static jaw crushers and worked for eight months as a stand-alone machine before the firm made the further step of buying the conveyors. This move meant there was no longer a need to run the site's two2294 CAT 771 haul trucks and reduced manpower at the face as well. However, this change did face challenges as the floor of the quarry slopes at over 10º to allow for the working of the beds. This required additional input from Metso engineers both from the UK and from Finland as it is the first of its kind in Europe on such a significant slope.
Initially, there were issues with manoeuvrability as it took over three hours to get the crusher and the links just right. However this operation takes just 30 minutes now and the site is able to move its entire crusher and conveyor train every other day. The site says that the crushers work more efficiently than before and that the operation is now regularly exceeding productivity levels of 400tonnes/hour.
Run by
The crusher and the conveyors have replaced a pair of static crushers and a rigid dump truck haulage fleet at the 135ha site. However, this changeover has required considerable interaction between Tarmac and engineers from both Metso Minerals (UK) and from its parent company in Finland.
The site has reserves of around 45 million tonnes, has been in use since 1880 and at present produces around 500,000tonnes/year. Some 85% of the product is a hard and abrasive quartz dolorite (whinstone) that is used in Tarmac road products and is very suitable for this purpose. The remaining 15% is blue limestone that is used for aggregates.
The quarry is 20m deep, and there are plans to lower the base still further to around 35m, which is unusual as most other local deposits lie at a depth of 13-15m.
Material is won by blasting, which takes place every three weeks, with each blast freeing around 30,000 tonnes. As the site has no immediate neighbours, noise and dust from blasting are not an issue, although the site is closely monitored and water suppression is used at the face.
The new LT140 has replaced a pair of ageing static jaw crushers and worked for eight months as a stand-alone machine before the firm made the further step of buying the conveyors. This move meant there was no longer a need to run the site's two
Initially, there were issues with manoeuvrability as it took over three hours to get the crusher and the links just right. However this operation takes just 30 minutes now and the site is able to move its entire crusher and conveyor train every other day. The site says that the crushers work more efficiently than before and that the operation is now regularly exceeding productivity levels of 400tonnes/hour.