Based on customer demand for new, extreme duty hydraulic breakers, Rammer is launching two new PRO hammers. The Rammer 2577 PRO and Rammer 5011 PRO are said to be innovative and tough.
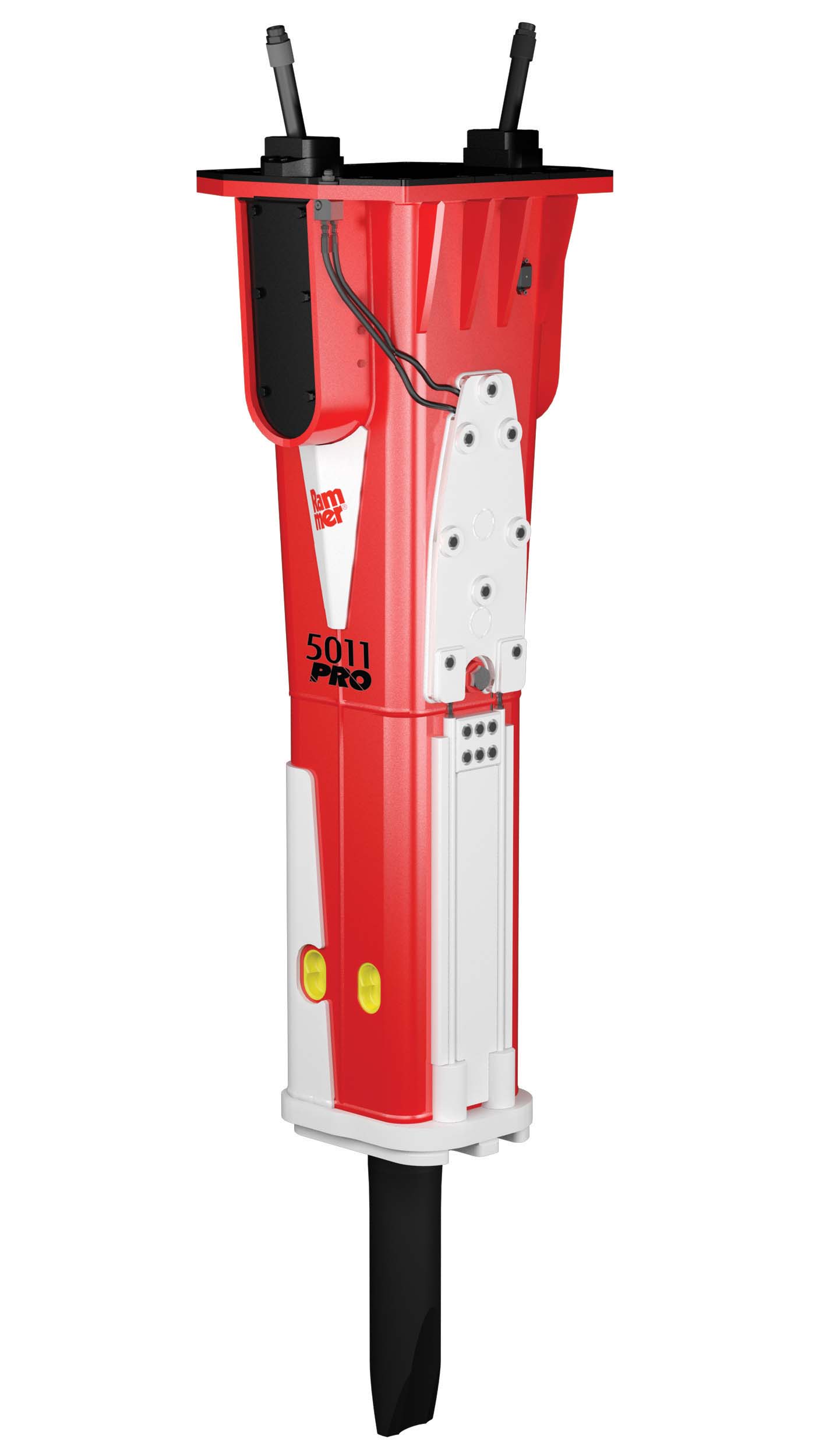
Tough and reliable, Rammer’s new breakers can be used for tunnelling applications
Based on customer demand for new, extreme duty hydraulic breakers, 5076 Rammer is launching two new PRO hammers.
The Rammer 2577 PRO and Rammer 5011 PRO are said to be innovative and tough. Suitable for carriers in the 21-32tonne and 43-80tonne weight ranges respectively, the new breakers have been specifically designed to work horizontally and undertake tunnelling duties in hard rock, being purpose built to withstand high levels of dust.
The 1.94tonne Rammer 2577 PRO and the 5.3tonne Rammer 5011 PRO are both based on the field-proven Rammer 2577 and 5011 hammers. These new models share key proven features that allow them to work in tough tunnelling duties. Both new models have an idle blow protector that provides greater levels of protection. Additionally they are equipped with long-life, high-tension VIDAT tie rods for improved reliability, extended service periods and lower operating costs.
Customers choosing the PRO range will be able to benefit from a sealed housing structure that prevents the ingress of dust and dirt, extending the working life of the hammer and the tool. A top cover plate has sealed through apertures for stump hydraulic hoses, and features sealed hose connections for grease, air and water.
The PRO hammers feature a sturdy housing design and wear resistant components to allow horizontal working duties. The Rammer PRO range models are also offered with special tools for horizontal primary breaking which have been designed to work with a broad range of auxiliary systems.
For customers working in tunnelling applications, Rammer has put together a package of auxiliary systems and solutions: the AGW unit. These have been designed to protect the hammer from the demands of this extreme application, delivering lower owning and operating costs. Special features include the proven Ramair air flush system that prevents potentially harmful dust ingress; the Ramlube I automatic lubrication system to ensure consistent and thorough greasing; and the water jet dust suppression package to minimise the creation of dust during breaking.
Hydraulically-actuated and requiring no additional power supply, the AGW Unit is said to be easy and safe to install and maintain.
The Rammer 2577 PRO and Rammer 5011 PRO are said to be innovative and tough. Suitable for carriers in the 21-32tonne and 43-80tonne weight ranges respectively, the new breakers have been specifically designed to work horizontally and undertake tunnelling duties in hard rock, being purpose built to withstand high levels of dust.
The 1.94tonne Rammer 2577 PRO and the 5.3tonne Rammer 5011 PRO are both based on the field-proven Rammer 2577 and 5011 hammers. These new models share key proven features that allow them to work in tough tunnelling duties. Both new models have an idle blow protector that provides greater levels of protection. Additionally they are equipped with long-life, high-tension VIDAT tie rods for improved reliability, extended service periods and lower operating costs.
Customers choosing the PRO range will be able to benefit from a sealed housing structure that prevents the ingress of dust and dirt, extending the working life of the hammer and the tool. A top cover plate has sealed through apertures for stump hydraulic hoses, and features sealed hose connections for grease, air and water.
The PRO hammers feature a sturdy housing design and wear resistant components to allow horizontal working duties. The Rammer PRO range models are also offered with special tools for horizontal primary breaking which have been designed to work with a broad range of auxiliary systems.
For customers working in tunnelling applications, Rammer has put together a package of auxiliary systems and solutions: the AGW unit. These have been designed to protect the hammer from the demands of this extreme application, delivering lower owning and operating costs. Special features include the proven Ramair air flush system that prevents potentially harmful dust ingress; the Ramlube I automatic lubrication system to ensure consistent and thorough greasing; and the water jet dust suppression package to minimise the creation of dust during breaking.
Hydraulically-actuated and requiring no additional power supply, the AGW Unit is said to be easy and safe to install and maintain.