Hitachi Construction Machinery (Europe) (HCME) has completed the €10 million restructure of its manufacturing sites at Oosterhout in the south of The Netherlands.
The Application Centre (AC) and Zaxis mini excavator factories have merged into one operation, which, according to HCME, will have far-reaching benefits for the firm.
“At first glance, there is no similarity between Hitachi mini excavators and special application machines,” said Tonny Engels, general manager at the Oosterhout factory. “Howev
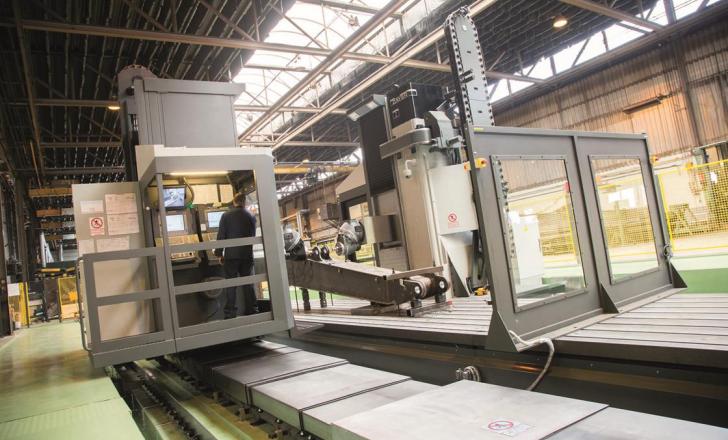
Hitachi has completed a large investment in its Oosterhout factory in the Netherlands
Hitachi Construction Machinery (Europe) (1139 HCME) has completed the €10 million restructure of its manufacturing sites at Oosterhout in the south of The Netherlands.
The Application Centre (AC) and Zaxis mini excavator factories have merged into one operation, which, according to HCME, will have far-reaching benefits for the firm.
“At first glance, there is no similarity between Hitachi mini excavators and special application machines,” said Tonny Engels, general manager at the Oosterhout factory. “However, we have successfully aligned these diverse product categories by combining the skills of our workforce for the production, painting and assembly processes.”
The challenge of combining the manufacture of these products has drawn on Engels and his team’s vast experience and specialist expertise. For example, they have had to overcome the differences between the methods involved in mass production – to build up a stock of minis – and a project-based approach for each individual special application order.
“Our priority is to increase the level of localisation in response to market demand and this is the main reason for the reorganisation of the facilities in Oosterhout,” added Engels. “We are continuing to assess the needs of our customers and how the designs can be adapted accordingly. New development teams have also been introduced for mini excavators and special application machines.
“Overall, the three main benefits to be derived from the restructure are increased operational efficiency, more reliable delivery times and reduced costs. Ultimately, we would like to have a situation in which job sharing is more commonplace and a more flexible workforce is at our disposal.”
The five main components currently produced for the mini products are the boom, arm, blade, track frame and mainframe, while the factory is focused on the front attachment for all special application products. The revamped Oosterhout facility also makes wheeled excavator brackets and compact wheeled loader front brackets for its sister factory in Amsterdam.
The production process has been revamped with the arms and booms being produced for the mini and special application machines in separate lines, before they go through the same machining process. A significant investment has been made with the installation of a new machining centre, which, HCME claims, has increased productivity by up to six times.
While the shot blasting and primary paint coat are outsourced for the special application machines, the mini components undergo a state-of-the-art process thanks to HCME’s investment in a fully automated paint booth. This can handle programming for 90 individual racks of components over an eight-hour shift to be shot blasted or degreased and primed with two high-quality coats of paint.
The implementation of the new Zaxis-5 range of special application excavators is said by HCME on track. Approximately half of the machines supplied are super long fronts – from the ZX160LC-5 to the ZX470LCH-5 – including the first product that features an 18m front attachment. The proportion of other machines is more or less divided equally between crawler and wheeled material handling, high-reach and straight-boom demolition, clamshell telescopic arm and forestry machines.
The full range of Zaxis-5 mini excavators has also been introduced to the factory floor in Oosterhout, while three models from the existing line-up are now completely produced in the factory – the ZX16-3, ZX17U-2 and ZX18-3 – with engine and hydraulic equipment supplied from Japan (along with the upper structure for the ZX17U-2).
The ZX22U-2, ZX27-3, ZX29U-3, ZX33U-5 and ZX38U-5 originate from daruma machines – the factory only has to add the front attachment and blade – and the ZX10U-2, ZX48U-5, ZX55U-5 and ZX65USB-5 are imported from Japan as complete products. In the near future, the ZX85US-5 will move from Amsterdam to Oosterhout, which will further enhance the control of the total supply chain for the compact line.
The Application Centre (AC) and Zaxis mini excavator factories have merged into one operation, which, according to HCME, will have far-reaching benefits for the firm.
“At first glance, there is no similarity between Hitachi mini excavators and special application machines,” said Tonny Engels, general manager at the Oosterhout factory. “However, we have successfully aligned these diverse product categories by combining the skills of our workforce for the production, painting and assembly processes.”
The challenge of combining the manufacture of these products has drawn on Engels and his team’s vast experience and specialist expertise. For example, they have had to overcome the differences between the methods involved in mass production – to build up a stock of minis – and a project-based approach for each individual special application order.
“Our priority is to increase the level of localisation in response to market demand and this is the main reason for the reorganisation of the facilities in Oosterhout,” added Engels. “We are continuing to assess the needs of our customers and how the designs can be adapted accordingly. New development teams have also been introduced for mini excavators and special application machines.
“Overall, the three main benefits to be derived from the restructure are increased operational efficiency, more reliable delivery times and reduced costs. Ultimately, we would like to have a situation in which job sharing is more commonplace and a more flexible workforce is at our disposal.”
The five main components currently produced for the mini products are the boom, arm, blade, track frame and mainframe, while the factory is focused on the front attachment for all special application products. The revamped Oosterhout facility also makes wheeled excavator brackets and compact wheeled loader front brackets for its sister factory in Amsterdam.
The production process has been revamped with the arms and booms being produced for the mini and special application machines in separate lines, before they go through the same machining process. A significant investment has been made with the installation of a new machining centre, which, HCME claims, has increased productivity by up to six times.
While the shot blasting and primary paint coat are outsourced for the special application machines, the mini components undergo a state-of-the-art process thanks to HCME’s investment in a fully automated paint booth. This can handle programming for 90 individual racks of components over an eight-hour shift to be shot blasted or degreased and primed with two high-quality coats of paint.
The implementation of the new Zaxis-5 range of special application excavators is said by HCME on track. Approximately half of the machines supplied are super long fronts – from the ZX160LC-5 to the ZX470LCH-5 – including the first product that features an 18m front attachment. The proportion of other machines is more or less divided equally between crawler and wheeled material handling, high-reach and straight-boom demolition, clamshell telescopic arm and forestry machines.
The full range of Zaxis-5 mini excavators has also been introduced to the factory floor in Oosterhout, while three models from the existing line-up are now completely produced in the factory – the ZX16-3, ZX17U-2 and ZX18-3 – with engine and hydraulic equipment supplied from Japan (along with the upper structure for the ZX17U-2).
The ZX22U-2, ZX27-3, ZX29U-3, ZX33U-5 and ZX38U-5 originate from daruma machines – the factory only has to add the front attachment and blade – and the ZX10U-2, ZX48U-5, ZX55U-5 and ZX65USB-5 are imported from Japan as complete products. In the near future, the ZX85US-5 will move from Amsterdam to Oosterhout, which will further enhance the control of the total supply chain for the compact line.