It was in the early 1980s when Luck Stone, a third generation American crushed stone, sand and gravel company, purchased its first Philippi-Hagenbuch Heavy Duty Autogate Tailgates. Nearly 30 years later the Richmond, Virginia-based firm claims its ongoing investment in Philippi-Hagenbuch (PHIL) Heavy Duty Autogate Tailgates has saved a fortune in equipment repairs and replacements.
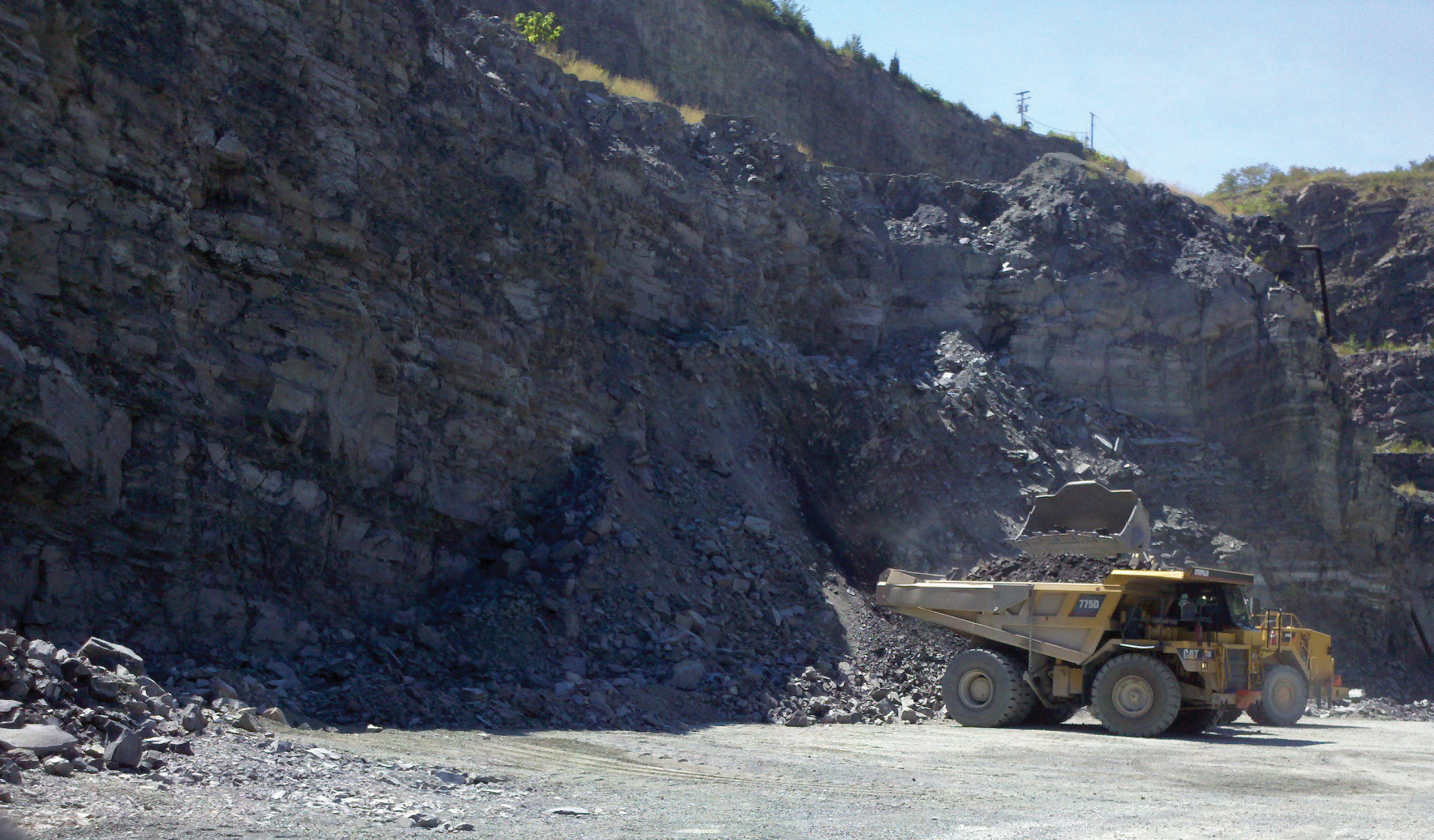
Luck Stone said nearly 30 years of using PHIL tailgates on its trucks has saved the crushed stone, sand and gravel company a fortune in maintenance costs
RSS6510 Philippi-Hagenbuch (PHIL) Heavy Duty Autogate Tailgates has saved a fortune in equipment repairs and replacements.
“Investing in our equipment is the best thing we can do, not only for our company, but for our customers as well,” said Butch Rakes,6511 Luck Stone’s mobile equipment manager.
Prior to purchasing their first PHIL tailgates, Luck Stone bosses noted day-to-day that material rolling off the onsite trucks had become a huge maintenance, safety and efficiency issue. Debris such as stones had the potential to fall on an operator or damage another piece of equipment. A debris-cluttered road is also hazardous for all drivers and equipment travelling on that route, with significant potential vehicle damage to undercarriages, suspensions and tyres. With some tyres alone costing more than $20,000 to replace, Luck Stone turned to PHIL to help with their maintenance dilemma.
“Before tailgates we were often forced tostop the equipment and clean the roads on a frequent basis,” said Jim Van Ness, vicepresident of Luck Stone operational support.
“But that approach significantly hampered our efficiency.”
As an example Ness said occasionally, in the case of larger stones, the crew would have to bring in a separate loader to move spillage that had fallen off the back of the truck body.
Not only did the addition of the PHIL tailgates reduce maintenance costs, they also increased overall jobsite safety. The tailgates eliminated the debris roll-off, in turn eliminating the need to have the crew cleaning the haul roads on the mine site.
“Before we purchased the gates, we noticed a serious threat to our workers’ safety,” said Rakes. “We had guys jumping in and out of haul trucks and pickups to move heavy rocks out of the haul roads. It was time for a better system.”
In addition to eliminating the need to move rock off the haul roads, the tailgates are said to offer the loader operator a better loading target and eliminate the need to reposition rocks in the body to keep them from falling off the back.
Van Ness said the pre-tailgates truck loading process was less than desirable. “Before we implemented the tailgates, the loading process felt slow because the loader operator was focusing on loading the front portion of the truck bed. In extreme cases it would be necessary to stop during loading for the operator to reposition the rock in the truck’s bed in order to even the load.
“Rock spillage and the difficulty loading the trucks had been a recurring problem. And what I really remember noticing was how it was adversely affecting the cycle times on our loaders. The process simply was not meeting efficiency expectations.”
Van Ness said the PHIL tailgates had an immediate impact. “Spillage was reduced and the cycle times on our loaders definitely increased. And of course, it was great to see our guys were no longer clearing debris out on those busy haul roads.
“We initially chose Philippi’s Standard Autogate Tailgate models for our2294 CAT rigid frame haul units. Those trucks have a 70tonne payload capacity,” he added. “We’ve continued to use the tailgates ever since.”
Van Ness noted that another added benefit of utilising the tailgates was the ability to achieve the rated capacity of the trucks. But he stressed that Luck Stone don’t ever use the tailgates as a means to overload the truck.RSS
It was in the early 1980s when Luck Stone, a third generation American crushed stone, sand and gravel company, purchased its first Philippi-Hagenbuch Heavy Duty Autogate Tailgates.
Nearly 30 years later the Richmond, Virginia-based firm claims its ongoing investment in“Investing in our equipment is the best thing we can do, not only for our company, but for our customers as well,” said Butch Rakes,
Prior to purchasing their first PHIL tailgates, Luck Stone bosses noted day-to-day that material rolling off the onsite trucks had become a huge maintenance, safety and efficiency issue. Debris such as stones had the potential to fall on an operator or damage another piece of equipment. A debris-cluttered road is also hazardous for all drivers and equipment travelling on that route, with significant potential vehicle damage to undercarriages, suspensions and tyres. With some tyres alone costing more than $20,000 to replace, Luck Stone turned to PHIL to help with their maintenance dilemma.
“Before tailgates we were often forced tostop the equipment and clean the roads on a frequent basis,” said Jim Van Ness, vicepresident of Luck Stone operational support.
“But that approach significantly hampered our efficiency.”
As an example Ness said occasionally, in the case of larger stones, the crew would have to bring in a separate loader to move spillage that had fallen off the back of the truck body.
Not only did the addition of the PHIL tailgates reduce maintenance costs, they also increased overall jobsite safety. The tailgates eliminated the debris roll-off, in turn eliminating the need to have the crew cleaning the haul roads on the mine site.
“Before we purchased the gates, we noticed a serious threat to our workers’ safety,” said Rakes. “We had guys jumping in and out of haul trucks and pickups to move heavy rocks out of the haul roads. It was time for a better system.”
In addition to eliminating the need to move rock off the haul roads, the tailgates are said to offer the loader operator a better loading target and eliminate the need to reposition rocks in the body to keep them from falling off the back.
Van Ness said the pre-tailgates truck loading process was less than desirable. “Before we implemented the tailgates, the loading process felt slow because the loader operator was focusing on loading the front portion of the truck bed. In extreme cases it would be necessary to stop during loading for the operator to reposition the rock in the truck’s bed in order to even the load.
“Rock spillage and the difficulty loading the trucks had been a recurring problem. And what I really remember noticing was how it was adversely affecting the cycle times on our loaders. The process simply was not meeting efficiency expectations.”
Van Ness said the PHIL tailgates had an immediate impact. “Spillage was reduced and the cycle times on our loaders definitely increased. And of course, it was great to see our guys were no longer clearing debris out on those busy haul roads.
“We initially chose Philippi’s Standard Autogate Tailgate models for our
Van Ness noted that another added benefit of utilising the tailgates was the ability to achieve the rated capacity of the trucks. But he stressed that Luck Stone don’t ever use the tailgates as a means to overload the truck.RSS