Major advances are being seen in the market for loading and hauling machines, with manufacturers developing new solutions for the quarry segment in particular- Mike Woof writes Wheeled loaders and rigid chassis dump trucks are key movers in many quarry operations. New develop-ments have seen the introduction of several new models from key players.
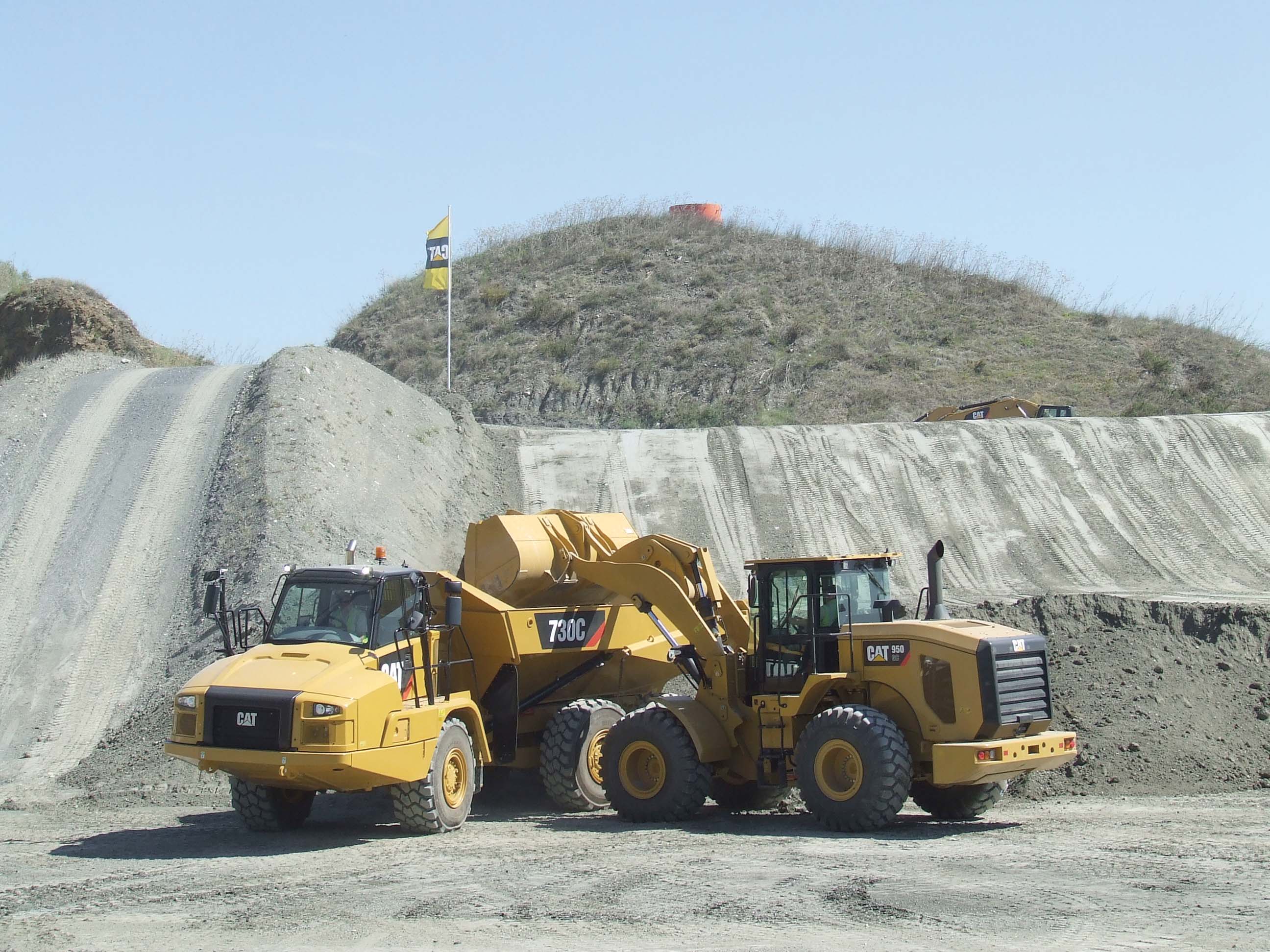
Caterpillar’s 950GC loader is designed specifically for duties such as stocking, loading and handling and is aimed at customers in emerging markets
Major advances are being seen in the market for loading and hauling machines, with manufacturers developing new solutions for the quarry segment in particular- Mike Woof writes
Wheeled loaders and rigid chassis dump trucks are key movers in many quarry operations. New develop-ments have seen the introduction of several new models from key players.
The wheeled loader sector is proving particularly strong with regard to the major manufacturers.178 Caterpillar continues to develop a number of new models that are aimed at highly specific market segments. The first example of this was the 986H model introduced last year as a mid-range machine for emerging markets and slotting into the line-up between the 980 and 988. This trend for developing market specific machines continues and the latest example comes with the new 950GC wheeled loader, which is unlike any existing models in the range.
The recently introduced 950H wheeled loader is a high performance, high quality machine aimed at use in face loading applications in quarrying. The new 950GC does share some components with the 950H, but is a completely different model aimed at a different customer base. Wheeled loader product application specialist in the Europe, Africa, Middle East territory for the existing 950H and new 950GC is Vincent Danloy. He said, “In the past we had one model of wheeled loader and we sold it to everybody.”
He explained that because of this approach, the 950H was developed as a high-end machine able to cope with tough production applications in quarries. However wheeled loaders are also used in utility applications and as support machines and Caterpillar has identified that the utility segment in particular is growing and accounts for an increasingly large percentage of sales. In this segment, duties such as stocking, handling and rehandling are prevalent, with the machines also used for truck loading.
Caterpillar's research showed that the 950H, with its heavy-duty structure designed for face loading applications, was effectively over-engineered for many wheeled loader customers. Its rugged structure and high quality transmission means that the 950H is costly and with price being a key selling point in some markets, Caterpillar identified that it had room in its range for a lower priced wheeled loader aimed primarily at stocking and handling duties, instead of the more arduous face handling operations. The company is at pains to point out though that the 950GC is by no means a lower quality machine.
Designed to compete in the popular 5tonne capacity segment that dominates the huge Chinese wheeled loader market, the 950GC is being built in Caterpillar’s Chinese facility. However this model is developed specifically for use in emerging territories such as Africa and the Middle East. Danloy said, “It’s a machine that is easy to operate, it has low fuel consumption and low owning and operating costs. This is not a 950H where we’ve removed some of the components.”
A notable difference between the existing 950H and the 950GC is with the design of the rear chassis. The articulation hinge for the rear chassis on the 950H uses far thicker section steel plate than is seen on the 950GC model.
Similarly, the rear chassis of the 950H has thick stiffening members that are absent from the 950GC. The transmissions too are different, with a powershift unit for the 950GC compared with the planetary transmission in the 950H. Power for both models comes from a C7.1 diesel but while the 18.7tonne 950H is offered in Tier 4 compliant versions, the 950GC is available in Tier 3 format so as to cope with the lower quality fuels found in the emergent markets that the model is specifically targeted at. The machine’s low fuel consumption is further aided by efficient load-sensing hydraulics and an auto-idle system that works for the 40% or so of the time that it is idling during the working day.
Like the 950H, the 950GC loader is offered with Caterpillar’s range of Performance Buckets. However, the standard capacity range for the 950GC is 3.1m3 compared with the 950H’s 3.4m3 standard bucket, while the 950GC’s loader arms give an extra 200m loading height suiting it to truck loading applications. Another notable feature is that the 950GC has Caterpillar’s latest loader cab, which offers high visibility and will be fitted to other machines (including the 950H) in due course.
Aimed at developed markets, the ZW180-5 model from Hitachi Construction Machinery is designed to meet the requirements of customers looking for highly productive yet fuel-efficient machines, with a lower Total cost of ownership. High productivity is claimed for this 15tonne class loader; the machine's 6.7litre diesel delivers 126kW and is said to maximise productivity, as well as offering good fuel consumption. It meets European emissions requirements due to a maintenance-free diesel oxidation catalyst (DOC), which operates without the need for a diesel particulate filter (DPF).
Fuel consumption is reduced by up to 10% compared to the previous model, due to the combination of a five speed transmission and the sophisticated electronically-controlled engine. An eco-system is said to further reduce the fuel burned.
The machine has two work modes, suitable for particular tasks. In standard mode the engine speed is controlled, which allows for smooth and efficient acceleration during loading, regular operations and travelling on level terrain. The P mode is useful when greater traction force is required for heavy-duty excavation and travelling uphill. When changing work modes, the ZW180-5 has a quick power switch, which boosts the power when required. Bucket capacities range from 2.4-2.8m³, with a 2.7m³ bucket as standard.
Operator comfort and cab visibility have been improved and the loader has a pillarless windshield and optional rear-view camera while its counterweight is also now visible from both sides of the machine. Maintenance has been improved and the redesigned engine and radiator cover can be opened fully, providing access for inspection while the greasing points, oil levels and fuel filters can all be accessed at ground level.
255 JCB’s new 457 wheeled loader is the first of the UK manufacturer’s machines to show off the new JCB CommandPlus cab, with a ROPS structure that has A pillars moved out to the same width as the rear of the cab. This provides a larger interior and offers a panoramic front windscreen. Power for the 457 comes from a 7.7litre MTU Tier 4 Final engine, delivering 193kW, up from 186kW on the previous machine. Notably, this cuts fuel consumption by some 16% over the previous model and as with other JCB machines, the engine meets Tier 4 Final requirements without the need for a DPF.
The sloping one-piece engine cover can be electrically raised away from the cab to provide better access to the engine and drivetrain for maintenance. The rear section can also be hinged away from the machine to provide access to the cooling pack: its hydraulically driven swing out radiators.
257 John Deere’s K Series wheeled loaders have adopted Tier 4 Final emissions standards through the use of its PowerTech engines.
The company has also improved machine durability through the addition of standard axle cooling and filtration, the use of Brake retractors and automatic adjusters to prevent wear and cut fuel consumption through Brake drag. The K Series utility wheeled loaders also feature a standard five-speed lock-up torque converter transmission that is said to cut fuel use by 5-8%.
Operator comfort is boosted due to a sound suppression kit while all John Deere wheeled loaders now come with the firm’s WorkSight telematics system as standard, providing remote maintenance and service access as well as diagnostics and geo-fencing capabilities, all of which help boost uptime and reduce unscheduled downtime.
Meanwhile7659 Volvo Construction Equipment’s new Tier 4 Final/Stage IV-compliant L250H wheeled loader has been designed to perform heavy tasks with better performance, safety and fuel economy levels using the manufacturer’s OptiShift technology.
In the North American market the L250H is ideally suited to working with on-highway trucks, and the L250H will load a 22.7tonne tri-axle on-highway truck in just two passes. Volvo CE’s OptiShift technology works by combining the company’s patented Reverse By Braking (RBB) technology and a torque converter with lock-up to eliminate power losses and reduce fuel consumption by up to 18%.
And the use of automatic Power Shift (APS) and Fully Automatic Power Shift (FAPS) technology further ensures minimal fuel consumption and fast cycle times, shifting the machine gears in line with engine and travel speed for optimal operation.
Volvo CE’s innovative eco pedal helps lower fuel consumption, by applying a mechanical pushback force when the throttle is used excessively and the engine rpm is about to exceed the economic operating range. Advanced load-sensing hydraulics supply power only when required, allowing smooth and fuel-efficient operation, as well as precise load control. The L250H’s optional Boom Suspension System (BSS) is said to boost productivity by up to 20% by absorbing shock and reducing bouncing and bucket spillage that occurs when operating on rough ground. This enables faster and more comfortable work cycles and increases machine life.
Similar gains are being seen in the haul trucks that the wheeled loaders work with on quarry sites. Increased productivity and reduced cycle times are key features of Caterpillar’s latest 770G and 772G off-highway trucks. Major upgrades have been made in emissions technology, transmission and traction control systems, helping to boost output, while optimised suspension systems give a better ride than on earlier generation machines. The new 770G has a nominal capacity of 36.3tonnes and is powered by a CAT C15 diesel rated at 356kW while the 772G offers a payload of 47.1tonnes and is driven by a CAT C18 diesel delivering 410kW. The trucks are designed to meet the needs of worldwide markets and are available in Tier 2/Stage II, Tier 3/Stage III, and Tier 4 Final/Stage IV variants.
Two programmable modes are available: Economy and Adaptive Economy. Economy Mode lets the customer reduce power by 0.5-15%. Meanwhile the Adaptive Economy Mode monitors power demand, delivering fuel savings when possible and power when needed, to ensure good fuel economy and performance.
Caterpillar's solution for the Tier 4 Final emissions standards on the C15 and C18 engines is through Selective Catalytic Reduction (SCR). The new transmission control system, Advanced Productivity Electronic Control Strategy (APECS), boosts shift quality, provides faster acceleration and better speed on grade. An optional advanced Traction-Control System is offered that uses the service brakes instead of the park Brake components to modulate wheel slip.
The frame designs have been modified to more balance weight and durability. Welds in critical stress areas are double-sided and ultrasonically tested to ensure integrity. High-strength steel is used throughout the frames to absorb the stress of impact loads, while proven box section construction manages torsion loads.
The 770G and 772G have a new four post ROPS/FOPS structure that is integral with the high visibility cab. The trucks come as standard with the firm’s sophisticated VIMS 3G, Caterpillar's Vital Information Management System; Truck Production Management System (TPMS); TKPH (tonne kilometre/hour) tyre management system, and Product Link (Standard or Cellular). The Advisor display in the cab provides an onboard interface for these information systems.
Moving up the size scale,233 Hitachi Construction Machinery has unveiled its EH1100-5 rigid dump truck, the latest version of the EH1100. The EH1100-5 retains several features, such as the long-life and highly compressible NeoconE/Helium suspension strut fluid, the robotically welded fully fabricated box section frame, trailing arm front suspension, and the body floating hinge pin design.
The EH1100-5 is said to include improvements to the operator environment, increased machine serviceability, increased payload, and more remote monitoring capability. Similar to the large Hitachi mining trucks and shovels, the EH1100-5 is equipped with a 25cm LCD display to provide the operator with information regarding hauling performance and systems condition. The truck has been designed with a capacity of 41.5m³ and has a flat floor plate for better control while dumping and its payload in standard configuration is 63.5 tonnes. For North America, the machine is offered with a Cummins QSK23 diesel but for other territories, customers have a choice of196 Cummins or MTU 12V 2000 units. Power outputs are the same at 567kW. The EH1100-5 rear wet disc Brake assemblies now include an integral wet disc parking Brake. While redesigning the rear wet brakes, Hitachi added Brake surface area to increase service braking and retarder horsepower. Hitachi offers a speed limit feature on the RH1100-5 that automatically restricts the truck’s top speed to a customer determined limit.
The new Hitachi RDT model also has technology and software improvements. The company’s active traction control system has been refined to better control wheel spin in wet and muddy conditions, resulting in improved haul cycle times and increased production.Furthermore, a transmission Optimum Shift Range has been developed to automatically alter the transmission range according to payload results provided by an onboard payload weighing system. The EH1100-5 is equipped with a data logging unit (DLU) to allow remote monitoring, which helps improve maintenance scheduling.
Many steering and Brake system valves and test ports have been relocated from the mid-frame of the truck to the service deck of the truck for easier service and troubleshooting access.
Wheeled loaders and rigid chassis dump trucks are key movers in many quarry operations. New develop-ments have seen the introduction of several new models from key players.
The wheeled loader sector is proving particularly strong with regard to the major manufacturers.
The recently introduced 950H wheeled loader is a high performance, high quality machine aimed at use in face loading applications in quarrying. The new 950GC does share some components with the 950H, but is a completely different model aimed at a different customer base. Wheeled loader product application specialist in the Europe, Africa, Middle East territory for the existing 950H and new 950GC is Vincent Danloy. He said, “In the past we had one model of wheeled loader and we sold it to everybody.”
He explained that because of this approach, the 950H was developed as a high-end machine able to cope with tough production applications in quarries. However wheeled loaders are also used in utility applications and as support machines and Caterpillar has identified that the utility segment in particular is growing and accounts for an increasingly large percentage of sales. In this segment, duties such as stocking, handling and rehandling are prevalent, with the machines also used for truck loading.
Caterpillar's research showed that the 950H, with its heavy-duty structure designed for face loading applications, was effectively over-engineered for many wheeled loader customers. Its rugged structure and high quality transmission means that the 950H is costly and with price being a key selling point in some markets, Caterpillar identified that it had room in its range for a lower priced wheeled loader aimed primarily at stocking and handling duties, instead of the more arduous face handling operations. The company is at pains to point out though that the 950GC is by no means a lower quality machine.
Designed to compete in the popular 5tonne capacity segment that dominates the huge Chinese wheeled loader market, the 950GC is being built in Caterpillar’s Chinese facility. However this model is developed specifically for use in emerging territories such as Africa and the Middle East. Danloy said, “It’s a machine that is easy to operate, it has low fuel consumption and low owning and operating costs. This is not a 950H where we’ve removed some of the components.”
A notable difference between the existing 950H and the 950GC is with the design of the rear chassis. The articulation hinge for the rear chassis on the 950H uses far thicker section steel plate than is seen on the 950GC model.
Similarly, the rear chassis of the 950H has thick stiffening members that are absent from the 950GC. The transmissions too are different, with a powershift unit for the 950GC compared with the planetary transmission in the 950H. Power for both models comes from a C7.1 diesel but while the 18.7tonne 950H is offered in Tier 4 compliant versions, the 950GC is available in Tier 3 format so as to cope with the lower quality fuels found in the emergent markets that the model is specifically targeted at. The machine’s low fuel consumption is further aided by efficient load-sensing hydraulics and an auto-idle system that works for the 40% or so of the time that it is idling during the working day.
Like the 950H, the 950GC loader is offered with Caterpillar’s range of Performance Buckets. However, the standard capacity range for the 950GC is 3.1m3 compared with the 950H’s 3.4m3 standard bucket, while the 950GC’s loader arms give an extra 200m loading height suiting it to truck loading applications. Another notable feature is that the 950GC has Caterpillar’s latest loader cab, which offers high visibility and will be fitted to other machines (including the 950H) in due course.
Aimed at developed markets, the ZW180-5 model from Hitachi Construction Machinery is designed to meet the requirements of customers looking for highly productive yet fuel-efficient machines, with a lower Total cost of ownership. High productivity is claimed for this 15tonne class loader; the machine's 6.7litre diesel delivers 126kW and is said to maximise productivity, as well as offering good fuel consumption. It meets European emissions requirements due to a maintenance-free diesel oxidation catalyst (DOC), which operates without the need for a diesel particulate filter (DPF).
Fuel consumption is reduced by up to 10% compared to the previous model, due to the combination of a five speed transmission and the sophisticated electronically-controlled engine. An eco-system is said to further reduce the fuel burned.
The machine has two work modes, suitable for particular tasks. In standard mode the engine speed is controlled, which allows for smooth and efficient acceleration during loading, regular operations and travelling on level terrain. The P mode is useful when greater traction force is required for heavy-duty excavation and travelling uphill. When changing work modes, the ZW180-5 has a quick power switch, which boosts the power when required. Bucket capacities range from 2.4-2.8m³, with a 2.7m³ bucket as standard.
Operator comfort and cab visibility have been improved and the loader has a pillarless windshield and optional rear-view camera while its counterweight is also now visible from both sides of the machine. Maintenance has been improved and the redesigned engine and radiator cover can be opened fully, providing access for inspection while the greasing points, oil levels and fuel filters can all be accessed at ground level.
The sloping one-piece engine cover can be electrically raised away from the cab to provide better access to the engine and drivetrain for maintenance. The rear section can also be hinged away from the machine to provide access to the cooling pack: its hydraulically driven swing out radiators.
The company has also improved machine durability through the addition of standard axle cooling and filtration, the use of Brake retractors and automatic adjusters to prevent wear and cut fuel consumption through Brake drag. The K Series utility wheeled loaders also feature a standard five-speed lock-up torque converter transmission that is said to cut fuel use by 5-8%.
Operator comfort is boosted due to a sound suppression kit while all John Deere wheeled loaders now come with the firm’s WorkSight telematics system as standard, providing remote maintenance and service access as well as diagnostics and geo-fencing capabilities, all of which help boost uptime and reduce unscheduled downtime.
Meanwhile
In the North American market the L250H is ideally suited to working with on-highway trucks, and the L250H will load a 22.7tonne tri-axle on-highway truck in just two passes. Volvo CE’s OptiShift technology works by combining the company’s patented Reverse By Braking (RBB) technology and a torque converter with lock-up to eliminate power losses and reduce fuel consumption by up to 18%.
And the use of automatic Power Shift (APS) and Fully Automatic Power Shift (FAPS) technology further ensures minimal fuel consumption and fast cycle times, shifting the machine gears in line with engine and travel speed for optimal operation.
Volvo CE’s innovative eco pedal helps lower fuel consumption, by applying a mechanical pushback force when the throttle is used excessively and the engine rpm is about to exceed the economic operating range. Advanced load-sensing hydraulics supply power only when required, allowing smooth and fuel-efficient operation, as well as precise load control. The L250H’s optional Boom Suspension System (BSS) is said to boost productivity by up to 20% by absorbing shock and reducing bouncing and bucket spillage that occurs when operating on rough ground. This enables faster and more comfortable work cycles and increases machine life.
Similar gains are being seen in the haul trucks that the wheeled loaders work with on quarry sites. Increased productivity and reduced cycle times are key features of Caterpillar’s latest 770G and 772G off-highway trucks. Major upgrades have been made in emissions technology, transmission and traction control systems, helping to boost output, while optimised suspension systems give a better ride than on earlier generation machines. The new 770G has a nominal capacity of 36.3tonnes and is powered by a CAT C15 diesel rated at 356kW while the 772G offers a payload of 47.1tonnes and is driven by a CAT C18 diesel delivering 410kW. The trucks are designed to meet the needs of worldwide markets and are available in Tier 2/Stage II, Tier 3/Stage III, and Tier 4 Final/Stage IV variants.
Two programmable modes are available: Economy and Adaptive Economy. Economy Mode lets the customer reduce power by 0.5-15%. Meanwhile the Adaptive Economy Mode monitors power demand, delivering fuel savings when possible and power when needed, to ensure good fuel economy and performance.
Caterpillar's solution for the Tier 4 Final emissions standards on the C15 and C18 engines is through Selective Catalytic Reduction (SCR). The new transmission control system, Advanced Productivity Electronic Control Strategy (APECS), boosts shift quality, provides faster acceleration and better speed on grade. An optional advanced Traction-Control System is offered that uses the service brakes instead of the park Brake components to modulate wheel slip.
The frame designs have been modified to more balance weight and durability. Welds in critical stress areas are double-sided and ultrasonically tested to ensure integrity. High-strength steel is used throughout the frames to absorb the stress of impact loads, while proven box section construction manages torsion loads.
The 770G and 772G have a new four post ROPS/FOPS structure that is integral with the high visibility cab. The trucks come as standard with the firm’s sophisticated VIMS 3G, Caterpillar's Vital Information Management System; Truck Production Management System (TPMS); TKPH (tonne kilometre/hour) tyre management system, and Product Link (Standard or Cellular). The Advisor display in the cab provides an onboard interface for these information systems.
Moving up the size scale,
The EH1100-5 is said to include improvements to the operator environment, increased machine serviceability, increased payload, and more remote monitoring capability. Similar to the large Hitachi mining trucks and shovels, the EH1100-5 is equipped with a 25cm LCD display to provide the operator with information regarding hauling performance and systems condition. The truck has been designed with a capacity of 41.5m³ and has a flat floor plate for better control while dumping and its payload in standard configuration is 63.5 tonnes. For North America, the machine is offered with a Cummins QSK23 diesel but for other territories, customers have a choice of
The new Hitachi RDT model also has technology and software improvements. The company’s active traction control system has been refined to better control wheel spin in wet and muddy conditions, resulting in improved haul cycle times and increased production.Furthermore, a transmission Optimum Shift Range has been developed to automatically alter the transmission range according to payload results provided by an onboard payload weighing system. The EH1100-5 is equipped with a data logging unit (DLU) to allow remote monitoring, which helps improve maintenance scheduling.
Many steering and Brake system valves and test ports have been relocated from the mid-frame of the truck to the service deck of the truck for easier service and troubleshooting access.