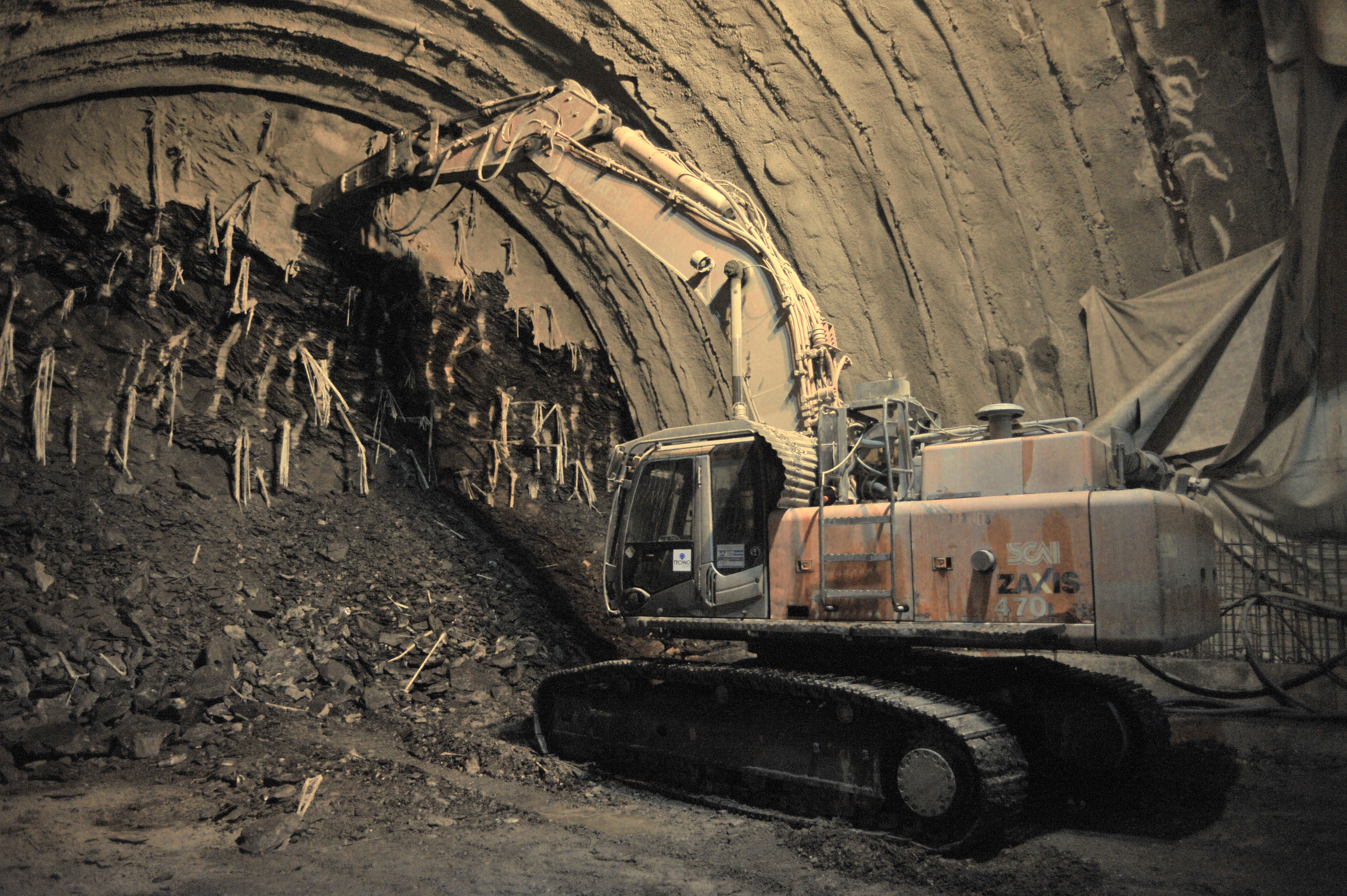
Upgrading Italy’s A3 highway is of prime importance for developing the south of the country and is a project that has been prioritised for construction. The A3 Salerno-Reggio-Calabria highway is a non-toll road managed by ANAS, Italy’s state-owned company that constructs and maintains highways. The route runs a total of 443km, with the road having originally been built between 1966 and 1974. However, the original route has a somewhat unenviable reputation for congestion as well as safety. Some of the sections of the route feature a number of curves that are considered too sharp for highway use, while there are also shortcoming with regard to several on- and off-ramps, as well as the width of the route.
Part of the problem with much of the original highway is that it was built in areas where road construction presents major challenges due to the orography, geology and in certain sections, levels of seismicity. Since 2001, the A3 has been the subject of major improvement works as part of a project that includes upgrading the old highway and building sections of a new and parallel route. So far, 339km of the A3 route has been rebuilt with the remaining 68.5km originally targeted for upgrading currently undergoing construction.
A key link in the new route is the Serra Rotonda Tunnel, a twin tube stretch of the highway being handled by the contractor GLF. The tunnel is located in the Basilicata region and lies close to the town of Lauria. The northern tube of the two measures 3.7255km long, while it also includes a 135.9m section at the north portal as well as a 7.1m section at its southern portal. Meanwhile the southern tube measures 3.74km long, as well as having a 128.65m entrance at the northern portal and 7.1m section at its southern portal.
Because of the difficult geological conditions, a combination of blasting alternating with the use of hydraulic breakers, has been used to drive the tunnels. The contractor selected blasting and breakers as this method suits excavation of hard rock masses. Two
The geomechanical profile of the rock presents numerous challenges. For the first circa 600m after the north portal, the tunnel cuts through deposits of Lagonegro, alternations of siliceous marl, argillite and calcilulite. This stretch has poor geotechnical characteristics, which can give rise to settlement or subsidence on the surface. To ensure the excavation could be carried out productively and safely, it was necessary to drive the tunnel ahead in sections, so as to balance out the stresses.
The remaining stretch of the tunnel runs through carbonate formations. These consist of limestone and graded calcarenite and dolomitic limestone, with maximum overburdens of about 430m. In the central zone the excavation cut through dolomitic limestone and dolomites that were intensely fractured.
It was realised early on that blasting and breaking would best suit the difficult conditions. These techniques were chosen for the excavation due to the characteristics and lack of homogeneity of the geological model. In addition, using blasting and breaking had another advantage, as at one end both tunnel tubes would lead out directly onto a viaduct under construction. For this latter instance, there would be no room for a large TBM.
The excavation started at the south entrance on the Reggio Calabria side. The contractor then used breakers in the north tube for a length of 2,424m and in the south tube for a length of 2,357m.
Not all of the rock had the fracturing and hardness levels that suited excavation using breakers however. Using the breakers, the production advance rate averaged 4m/day, with peaks of 6-7m/day. However, as the rock conditions became more challenging, this advance rate decreased progressively until reaching levels below 1m/day. The rock formations here featured limestone and graded calcarenite, which are slightly fractured and with pronounced karst phenomena and have hardnesses of up to 70MPa.
Because the productivity rate had fallen due to the conditions, it was decided by the tunnelling team to switch to drilling and blasting. However the rock conditions along a 50m stretch were so poor also meant that after each round of blasting, the breakers then had to brought back in to complete excavation and profiling of the tunnel. Meanwhile emergency access links were also driven between the north and south tubes, which are design to be sufficiently large to be used by vehicles.
The sub-contractor working on the project, Castellano, also managed to increase productivity by working in both directions. This was achieved by crossing over through the emergency access tunnel from a completed section of the other tube.
Castellano used the Indeco HP 7000 hydraulic breakers from the opening in the north tube for 1,156m. Meanwhile, the contractor used drilling and blasting in the north tube for a distance of around 806m. For the south tube, Castellano used the breakers to advance around 1,064m, with drilling and blasting being used for around 753m.
In certain stretches the rock mass features siliceous marl, argillite and calcilulite with poor geotechnical characteristics. To ensure stability, the firm reinforced the face with the ADECO RS fibreglass elements. A further complexity in this stretch came with presence of methane gas, which had been noted during the early surveys and was then detected by the safety monitoring systems in place. To ensure safety, special excavators equipped with explosion-proof technology were provided by Technoscavi.
Excavators fitted with the Indeco HP 7000 breakers were used on a 344m section that was minimally cohesive and highly fractured, with hardness values in some cases of less than 8Mpa.
Overall for the tunnel project, the breakers were highly effective for much of the work, even when gas was present. Good overall advance rates were achieved using the breakers, allowing the contractor to carry out the tunnel excavation within the planned schedule. Drilling and blasting would not have proven so efficient had this method been used for all the tunnelling work due to the widely varying rock conditions. The highly fractured rock in some sections would have resulted in a low advance rate using drilling and blasting.